Air pump maintenance and troubleshooting, Sensor information, Correcting lean air fuel readings – Dynojet Compressed Air Air/Fuel Ratio Module User Manual
Page 23
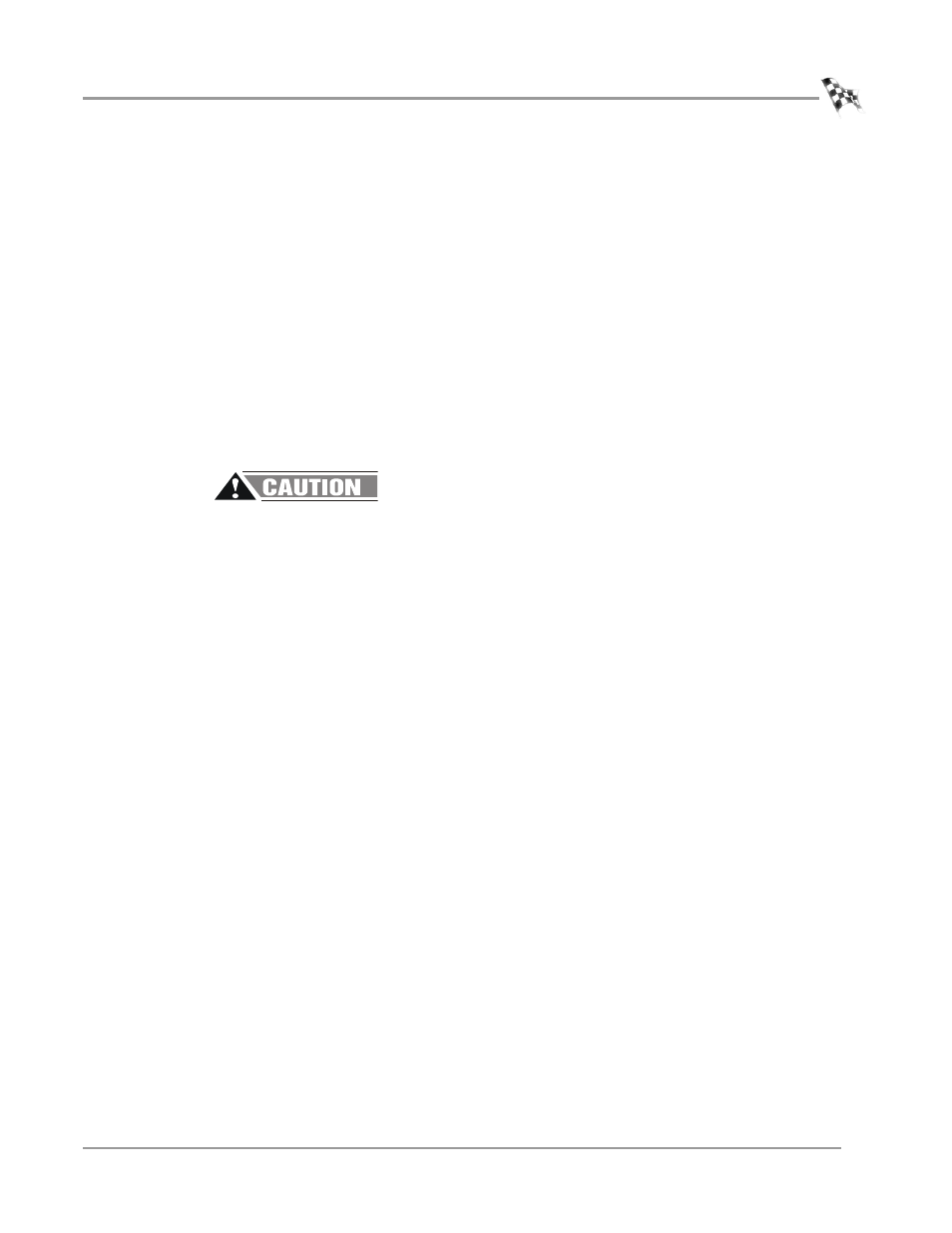
U S I N G T H E A I R F U E L R A T I O M O D U L E
Air Pump Maintenance and Troubleshooting
Version 5
Compressed Air Air Fuel Ratio Module Installation and User Guide
2-7
. . . . . . . . . . . . . . . . . . . . . . . . . . . . . . . . . . .
AIR PUMP MAINTENANCE AND TROUBLESHOOTING
This section contains sensor information and describes the procedures for
maintaining and troubleshooting the pump assembly.
Make sure you are aware of the following items:
• Keep the air pump upright. Tipping the pump may result in damage to the sensor.
• Leaks in the system will result in erroneous readings. Verify there are no cracks or
holes in the hoses. Verify the sensor is seated properly in the sensor block.
S
ENSOR
I
NFORMATION
Under optimal conditions, the sensor life can exceed 1500 hours. When using leaded
race fuel, 2.5 grams of lead per gallon of fuel will reduce the expected life of the
sensor to less than 100 hours.
The sensor is not covered by a warranty. Be sure to read and understand the
Compressed Air Air Fuel Ratio Module Installation and User manual.
C
ORRECTING
L
EAN
A
IR
F
UEL
R
EADINGS
Refer to the instructions below if you are experiencing air fuel ratio readings that are
leaner than you expected.
1
Verify the pump is on.
2
Check the system for restrictions in the air flow such as a kinked hose or dirty
pump.
3
Verify the copper sample tube is not kinked or clogged and is inserted into the
exhaust as far as possible. Refer to Figure 2-1.
4
Check for leaks in the system.
4a
Verify all hoses are securely attached to the fittings.
4b
Verify there are no cracks or holes in the hoses.
4c
Verify the sensor is seated properly in the sensor block.