Great Plains 2525A Operator Manual User Manual
Page 65
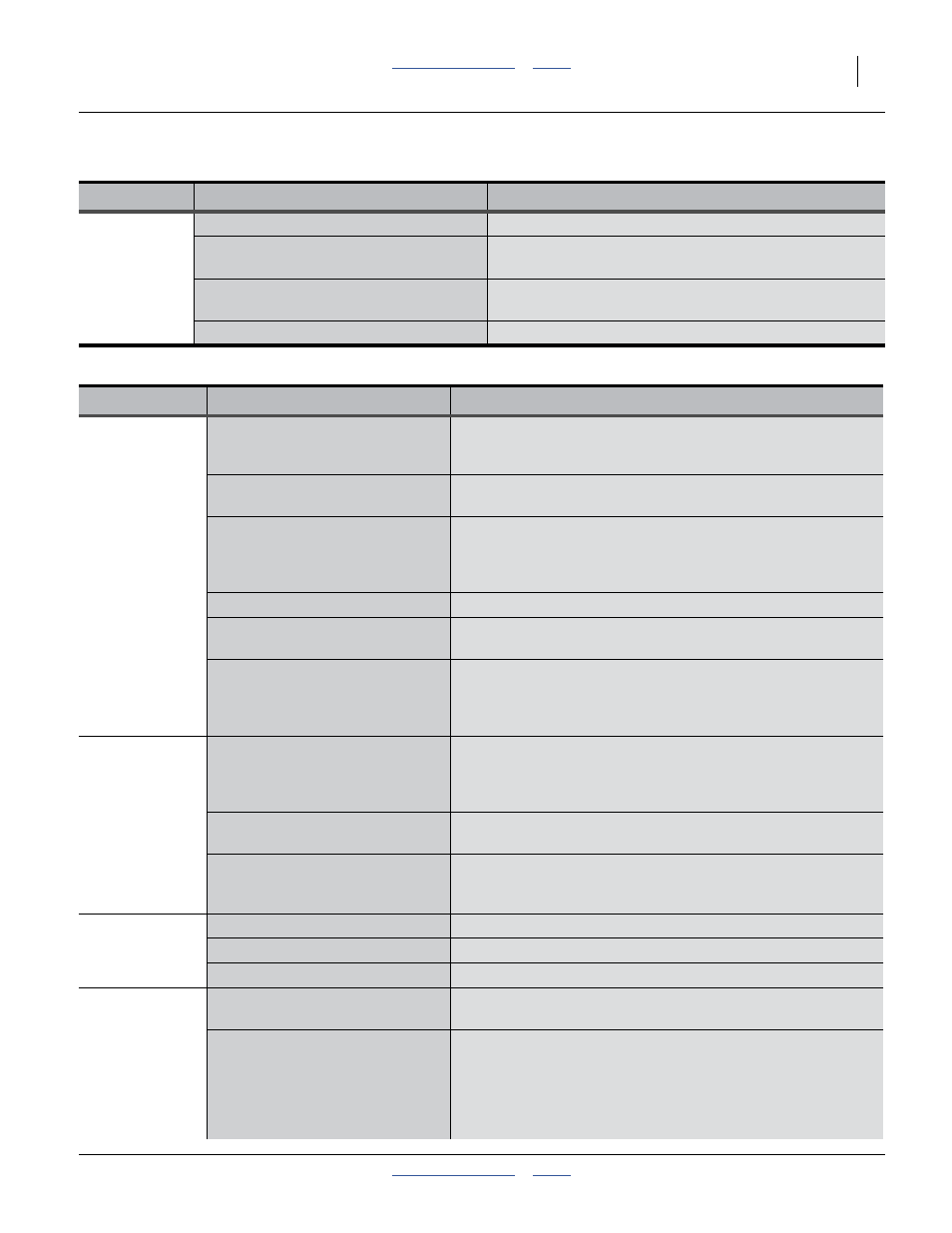
Great Plains Manufacturing, Inc.
Troubleshooting
61
2013-06-04
118-999M
High
Population,
Single Row
Excess meter pressure causing doubles
Check shutter.
Worn seed-drop brush and/or strip
brushes allowing excess seed to pass
Replace worn brushes.
Worn meter bearing causing seed disk
wobble and doubles
Replace meter bearing.
Incorrect seed disk with higher cell count. Install correct disk.
Population Too High
Problem
Cause
Solution
Population Related
Problem
Cause
Solution
Overall
Population
Alarms
(with optional
seed monitor)
False alarms or actual rate errors
due to monitor setup with incor-
rect [active] row count or spacing
When troubleshooting population issues, always first rule out
seed monitor setup. Review drill configuration and monitor
setup.
Incorrect cell count
Replace seed disks with correct disks, or reset rate for current
disks (if within range).
(option) Improper gap on mag-
netic speed sensor.
Check speed sensor on drill for a gap to toothed wheel of:
1
⁄
32
in (0.020-0.040in, 0.5-1.0mm). Improper gap can cause
erratic speed signal causing monitor to falsely report improper
planting rate.
Incorrect speed sensor constant
Perform speed calibration per monitor manual.
(option) Incorrect radar speed
sensor angle.
With planter lowered, check radar speed sensor angle per
DICKEY-john® recommendations.
Seed run-out. Due to unequal
outlets per box division, and if
planting across slopes, some
rows will run out before others.
Re-distribute seed to favor rows that have run out, and plan to
re-fill shortly.
Mismatch
Between
Reported and
Furrow
Population
(with optional
seed monitor)
Small seeds (example milo) are
not reliably sensed in the seed
tube
Run with rain covers in place to minimize ambient light intru-
sion. Use the population scaling factor in the seed monitor
system to compensate for missed seeds. Remember to set
this back to 100% for large seeds.
Seed tube sensor is not counting
all seeds
Clean the seed tube of graphite and dust buildup with long
narrow seed tube brush. Replace sensors that malfunction.
Seeds / revolution value in the
monitor setup does not match the
disk cell count.
Correct the value in a setup screen or install the correct cell
count disc.
Excessive
Seed
Cracking
Incorrect seed pocket size
Use correct disk for seed.
Damaged, old or dried-out seed
Use new seed.
Unclean seed
Use clean seed.
Skips and
Bare Spots
After Turns
Fan was turned off at turns
Leave fan running; meter pressure must be maintained during
turns, or seed will fall out of disk pockets.
Insufficient hydraulic flow to keep
fan running at speed required to
maintain meter pressure
Check tractor capability against requirements (page 88).
If sufficient:
• Fold markers before engaging lift.
• Use a less aggressive lift rate.
• Monitor meter pressure during end-of-pass operations.