Great Plains NP3000A Operator Manual User Manual
Page 35
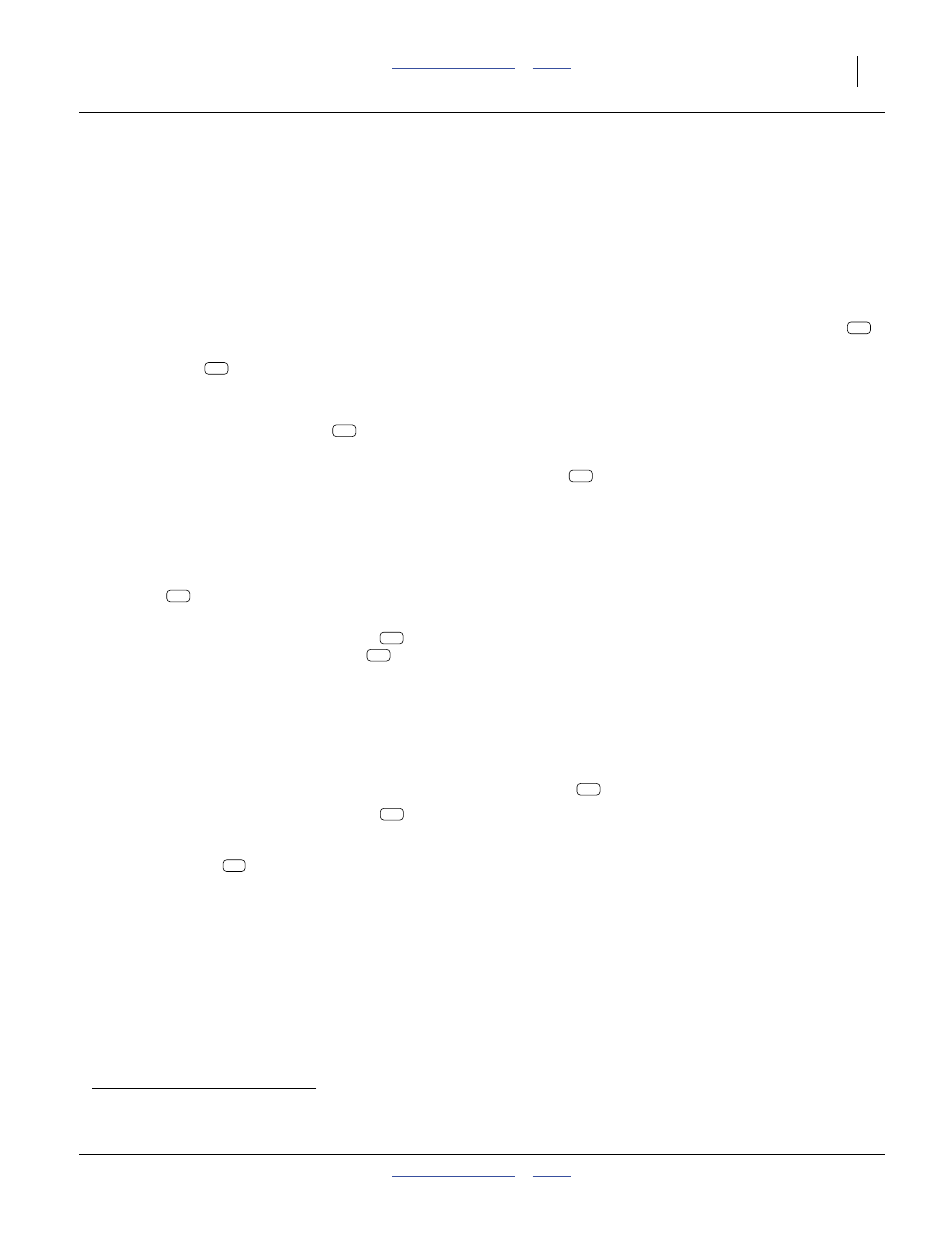
Great Plains Manufacturing, Inc.
Application Overview
31
2014-04-22
407-613M
L22. Passive Manifold
Ground Drive Option:
The factory configuration of this fitting has two
outlets capped. The third is plumbed to the optional
front boom.
With user-provisioned fittings and hoses, this
manifold can split the flow across two booms, or
across three sections of a single boom.
However configured, equal flow is assured by the
orifice plates
.
L23. Gauge Protector
Ground Drive Option: This fitting transmits manifold
pressure to the pressure gauge
, and protects
the gauge from direct contact with corrosive
fertilizer.
L24. Pressure Gauge
Ground Drive Option: This 0-to-100 psi gauge
reports the pressure in the manifold, which is
typically 15-to-40 psi during application. The
pressure should be above zero only when fertilizer
is flowing. The back-pressure at the nozzle
orifices
falls quickly when the pump stops.
Check the pressure periodically during application.
If it rises to over 65 psi, the relief valve
may be
activating. See also pressure sensor
.
L25. Relief Valve
Ground Drive Option: Adjust this valve to activate at
65 psi (page 94). This valve protects the manifold
against blockages, and from over-pressure due to
orifice sizes too small for the application rate or the
material viscosity.
L26. Dump Line
Ground Drive Option: If the relief valve
operates, material is jettisoned at this tube. If you
observe dumping, check the pressure and review
the orifice plate
configuration.
L27. Hydraulic Drive Pump
Hydraulic Drive Option: The Ace
FMC-150F-HYD-206 has a capacity of up to
150 gallons/minute (560 liters/minute). See the
HYD-MAN Ace Pump Instruction manual for
maintenance.
L28. Air Bleed Line
This line to the tank enabled pump priming by
bleeding off air. If using an off-applicator tank, a
user-provisioned bleed line or bleed valve must be
provided for pump priming.
L29. Flow Control Valve
Hydraulic Drive Option: Under the control of the
console (not shown) this valve is being constantly
adjusted to regulate pump output to the current
application rate (as reported by the flow meter
).
Only one flow control valve can be controlled by a
single Raven SCS 450 console.
L30. Flow Meter
Hydraulic Drive Option: This sensor reports the
actual material rate entering the hydraulic drive
manifold. As it detects variations from your desired
rate, it signals the console to adjust the control
valve
. Only one flow meter can be monitored by
a single Raven SCS 450 console.
L31. Section Valves
Hydraulic Drive Option:
There are three On/Off solenoid valves (1, 2 & 3).
The factory configuration uses only valve 1.
Valves 2 and 3 have their outlets capped.
The valves open and close under the control of
BOOMS switches on the Raven SCS 450
a
or other
compatible console.
L32. Pressure Sensor
Hydraulic Drive Option: The optional Raven
SCS 450 console displays the manifold pressure
during operation. This is measuring essentially the
same pressure as the mechanical pressure
gauge
. Only one pressure sensor can be
monitored by a single Raven SCS 450 console.
L33. Boom
Boom Option: There is one boom assembly per
applicator section. Booms may be different lengths,
and have different drop counts at center and on
wings.
The factory configuration provides the booms
interconnected as a single section.
L34. End Cap
Boom Option: In the factory configuration, the wing
booms each have a cap. These caps are removed
for clean-out (see page 118).
L38
L24
L38
L25
L32
L25
L38
a. Although the Raven SCS 450 has six section valves, the harness provided has only four Valve leads. Controlling more than three
valves with a single SCS 450 would require the purchase of an alternate harness from Raven.
L30
L29
L24