03 publications, Cutmaster 42 – Tweco 42 CutMaster Operating Manual User Manual
Page 5
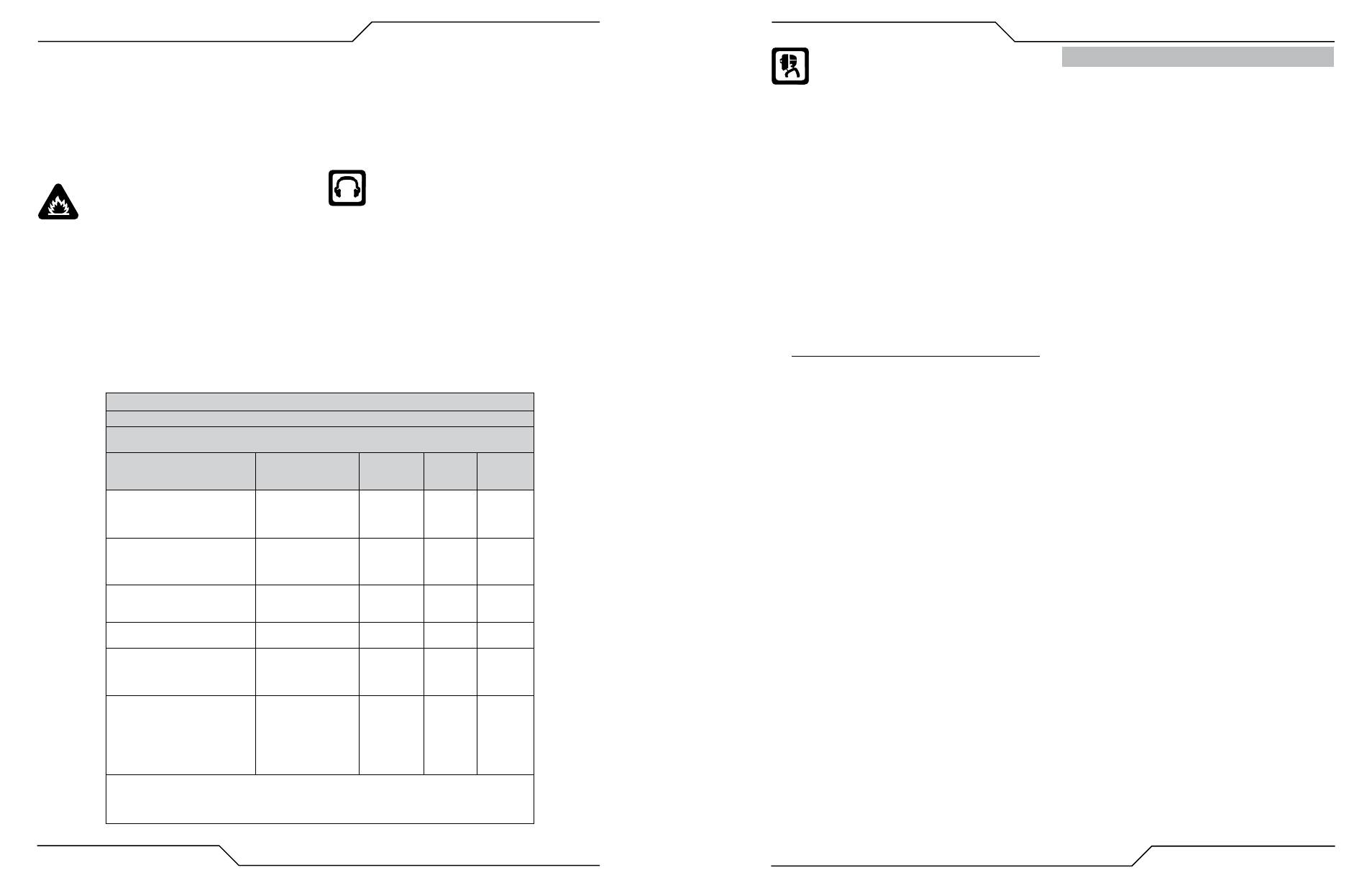
GENERAL INFORMATION 1-2 Manual 0-5141
Manual 0-5141
1-3 GENERAL INFORMATION
CUTMASTER 42
CUTMASTER 42
• Extra care must be taken when the workplace is moist or
damp.
• Install and maintain equipment according to NEC code,
refer to item 9 in Subsection 1.03, Publications.
• Disconnect power source before performing any service
or repairs.
• Read and follow all the instructions in the Operating
Manual.
FIRE AND EXPLOSION
Fire and explosion can be caused by hot slag, sparks, or the
plasma arc.
• Be sure there is no combustible or flammable material
in the workplace. Any material that cannot be removed
must be protected.
• Ventilate all flammable or explosive vapors from the
workplace.
• Do not cut or weld on containers that may have held
combustibles.
• Provide a fire watch when working in an area where fire
hazards may exist.
• Hydrogen gas may be formed and trapped under alu-
minum workpieces when they are cut underwater or
while using a water table. DO NOT cut aluminum alloys
underwater or on a water table unless the hydrogen gas
can be eliminated or dissipated. Trapped hydrogen gas
that is ignited will cause an explosion.
NOISE
Noise can cause permanent hearing loss. Plasma arc processes
can cause noise levels to exceed safe limits. You must protect
your ears from loud noise to prevent permanent loss of hearing.
• To protect your hearing from loud noise, wear protec-
tive ear plugs and/or ear muffs. Protect others in the
workplace.
• Noise levels should be measured to be sure the decibels
(sound) do not exceed safe levels.
• For information on how to test for noise, see item 1 in
Subsection 1.03, Publications, in this manual.
PLASMA ARC RAYS
Plasma Arc Rays can injure your eyes and burn your skin. The
plasma arc process produces very bright ultra violet and infrared
light. These arc rays will damage your eyes and burn your skin
if you are not properly protected.
• To protect your eyes, always wear a welding helmet or
shield. Also always wear safety glasses with side shields,
goggles or other protective eye wear.
• Wear welding gloves and suitable clothing to protect your
skin from the arc rays and sparks.
• Keep helmet and safety glasses in good condition. Re-
place lenses when cracked, chipped or dirty.
• Protect others in the work area from the arc rays. Use
protective booths, screens or shields.
• Use the shade of lens as suggested in the following chart.
Minimum Protective Suggested
Arc Current
Shade No.
Shade No.
Less Than 300*
8
9
300 - 400*
9
12
400 - 800*
10
14
* These values apply where the actual arc
is clearly seen. Experience has shown that
lighter filters may be used when the arc is
hidden by the workpiece.
1.03 Publications
Refer to the following standards or their latest revisions for
more information:
1. OSHA, SAFETY AND HEALTH STANDARDS, 29CFR 1910, obtain-
able from the Superintendent of Documents, U.S. Government
Printing Office, Washington, D.C. 20402
2. ANSI Standard Z49.1, SAFETY IN WELDING AND CUTTING, ob-
tainable from the American Welding Society, 550 N.W. LeJeune
Rd, Miami, FL 33126
3. NIOSH, SAFETY AND HEALTH IN ARC WELDING AND GAS
WELDING AND CUTTING, obtainable from the Superintendent of
Documents, U.S. Government Printing Office, Washington, D.C.
20402
4. ANSI Standard Z87.1, SAFE PRACTICES FOR OCCUPATION AND
EDUCATIONAL EYE AND FACE PROTECTION, obtainable from
American National Standards Institute, 1430 Broadway, New York,
NY 10018
5. ANSI Standard Z41.1, STANDARD FOR MEN’S SAFETY-TOE
FOOTWEAR, obtainable from the American National Standards
Institute, 1430 Broadway, New York, NY 10018
6. ANSI Standard Z49.2, FIRE PREVENTION IN THE USE OF CUTTING
AND WELDING PROCESSES, obtainable from American National
Standards Institute, 1430 Broadway, New York, NY 10018
7. AWS Standard A6.0, WELDING AND CUTTING CONTAINERS
WHICH HAVE HELD COMBUSTIBLES, obtainable from American
Welding Society, 550 N.W. LeJeune Rd, Miami, FL 33126
8. NFPA Standard 51, OXYGEN-FUEL GAS SYSTEMS FOR WELDING,
CUTTING AND ALLIED PROCESSES, obtainable from the National
Fire Protection Association, Batterymarch Park, Quincy, MA 02269
9. NFPA Standard 70, NATIONAL ELECTRICAL CODE, obtainable
from the National Fire Protection Association, Batterymarch Park,
Quincy, MA 02269
10. NFPA Standard 51B, CUTTING AND WELDING PROCESSES,
obtainable from the National Fire Protection Association, Bat-
terymarch Park, Quincy, MA 02269
11. CGA Pamphlet P-1, SAFE HANDLING OF COMPRESSED GASES
IN CYLINDERS, obtainable from the Compressed Gas Association,
1235 Jefferson Davis Highway, Suite 501, Arlington, VA 22202
12. CSA Standard W117.2, CODE FOR SAFETY IN WELDING AND
CUTTING, obtainable from the Canadian Standards Association,
Standards Sales, 178 Rexdale Boulevard, Rexdale, Ontario, Canada
M9W 1R3
13. NWSA booklet, WELDING SAFETY BIBLIOGRAPHY obtainable
from the National Welding Supply Association, 1900 Arch Street,
Philadelphia, PA 19103
14. American Welding Society Standard AWSF4.1, RECOMMENDED
SAFE PRACTICES FOR THE PREPARATION FOR WELDING AND
CUTTING OF CONTAINERS AND PIPING THAT HAVE HELD HAZ-
ARDOUS SUBSTANCES, obtainable from the American Welding
Society, 550 N.W. LeJeune Rd, Miami, FL 33126
15. ANSI Standard Z88.2, PRACTICE FOR RESPIRATORY PROTEC-
TION, obtainable from American National Standards Institute, 1430
Broadway, New York, NY 10018
AWS F2.2:2001 (R2010), Adapted with permission of the American Welding Society (AWS), Miami, Florida
Guide for Shade Numbers
(from AWS F2.2, Lens Shade Selector)
Shade numbers are given as a guide only and may be varied to suit individual needs.
Process
Electrode Size in. (mm)
Arc Current
(Amperes)
Minimum
Protective
Shade
Suggested*
Shade No.
(Comfort)
Shielded Metal Arc Welding (SMAW)
Less than 3/32 (2.4)
3/32-5/32 (2.4-4.0)
5/32-1/4 (4.0-6.4)
More than 1/4 (6.4)
Less than 60
60-160
160-250
250-550
7
8
10
11
-
10
12
14
Gas Metal Arc Weding (GMAW) and
Flux Cored Arc Welding (FCAW)
Less than 60
60-160
160-250
250-550
7
10
10
10
-
11
12
14
Gas Tungsten arc Welding (GTAW)
Less than 50
50-150
150-500
8
8
10
10
12
14
Air Carbon Arc Cutting (CAC-A)
(Light)
(Heavy)
Less than 500
500-1000
10
11
12
14
Plasma Arc Welding (PAW)
Less than 20
20-100
100-400
400-800
6
8
10
11
6 to 8
10
12
14
Plasma Arc Cutting (PAC)
Less than 20
20-40
40-60
60-80
80-300
300-400
400-800
4
5
6
8
8
9
10
4
5
6
8
9
12
14
* As a rule of thumb, start with a shade that is too dark to see the weld zone. Then go to a lighter shade
which gives sufficient view of the weld zone without going below the minimum. In oxyfuel gas welding,
cutting, or brazing where the torch and/or the flux produces a high yellow light, it is desirable to use a
filter lens that absorbs the yellow or sodium line of the visible light spectrum.
Table 1-1