Tweco CutMaster 12mm-20mm-25mm User Manual
Page 39
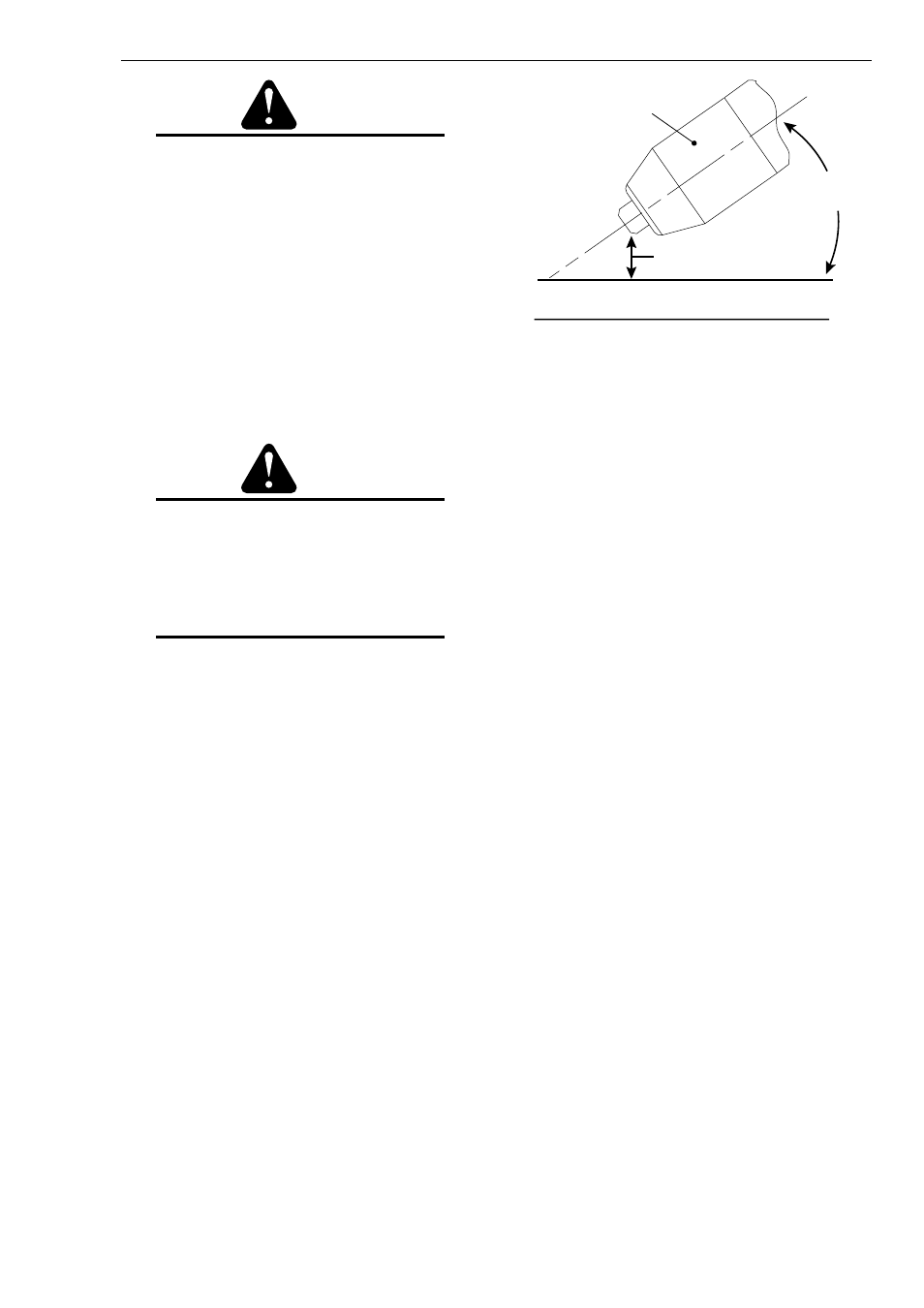
CUTMASTER 12mm, 20mm, 25mm
Manual 0-5117 4T-7 OPERATION
CAUTION
Sparks from plasma gouging can cause
damage to coated, painted or other sur-
faces such as glass, plastic, and metal.
Check torch parts. The torch parts must
correspond with the type of operation.
for Manual and Mechanized Torch Cutting".
Gouging Parameters
Gouging performance depends on parameters
such as torch travel speed, current level, lead angle
(the angle between the torch and workpiece), and
the distance between the torch tip and workpiece
(standoff).
CAUTION
Touching the torch tip or shield cup to the
work surface will cause excessive parts
wear.
Torch Travel Speed
NOTE
Refer to Appendix Pages for additional
information as related to the Power Supply
used.
Optimum torch travel speed is dependent on cur-
rent setting, lead angle, and mode of operation
(hand or machine torch).
Current Setting
Current settings depend on torch travel speed,
mode of operation (hand or machine torch), and
the amount of material to be removed.
Lead Angle
The angle between the torch and workpiece de-
pends on the output current setting and torch
travel speed. The recommended lead angle is
35°. At a lead angle greater than 45° the molten
metal will not be blown out of the gouge and may
be blown back onto the torch. If the lead angle
is too small (less than 35°), less material may be
removed, requiring more passes. In some appli-
cations, such as removing welds or working with
light metal, this may be desirable.
35°
Workpiece
Torch Head
Standoff Height
A-00941_AB
Gouging Angle and Standoff Distance
Standoff Distance
The tip to work distance affects gouge quality and
depth. Standoff distance of 1/8 - 1/4 inch (3 - 6
mm) allows for smooth, consistent metal removal.
Smaller standoff distances may result in a sever-
ance cut rather than a gouge. Standoff distances
greater than 1/4 inch (6 mm) may result in mini-
mal metal removal or loss of transferred main arc.
Slag Buildup
Slag generated by gouging on materials such as
carbon and stainless steels, nickels, and alloyed
steels, can be removed easily in most cases. Slag
does not obstruct the gouging process if it accumu-
lates to the side of the gouge path. However, slag
build - up can cause inconsistencies and irregular
metal removal if large amounts of material build
up in front of the arc. The build - up is most often
a result of improper travel speed, lead angle, or
standoff height.