E - doc, Revision authorization, Connector – Rockwell Automation 2030-MLXxxx-SYSx System Multiplexer / Permissive Module User Manual
Page 2: Description function, Sheet
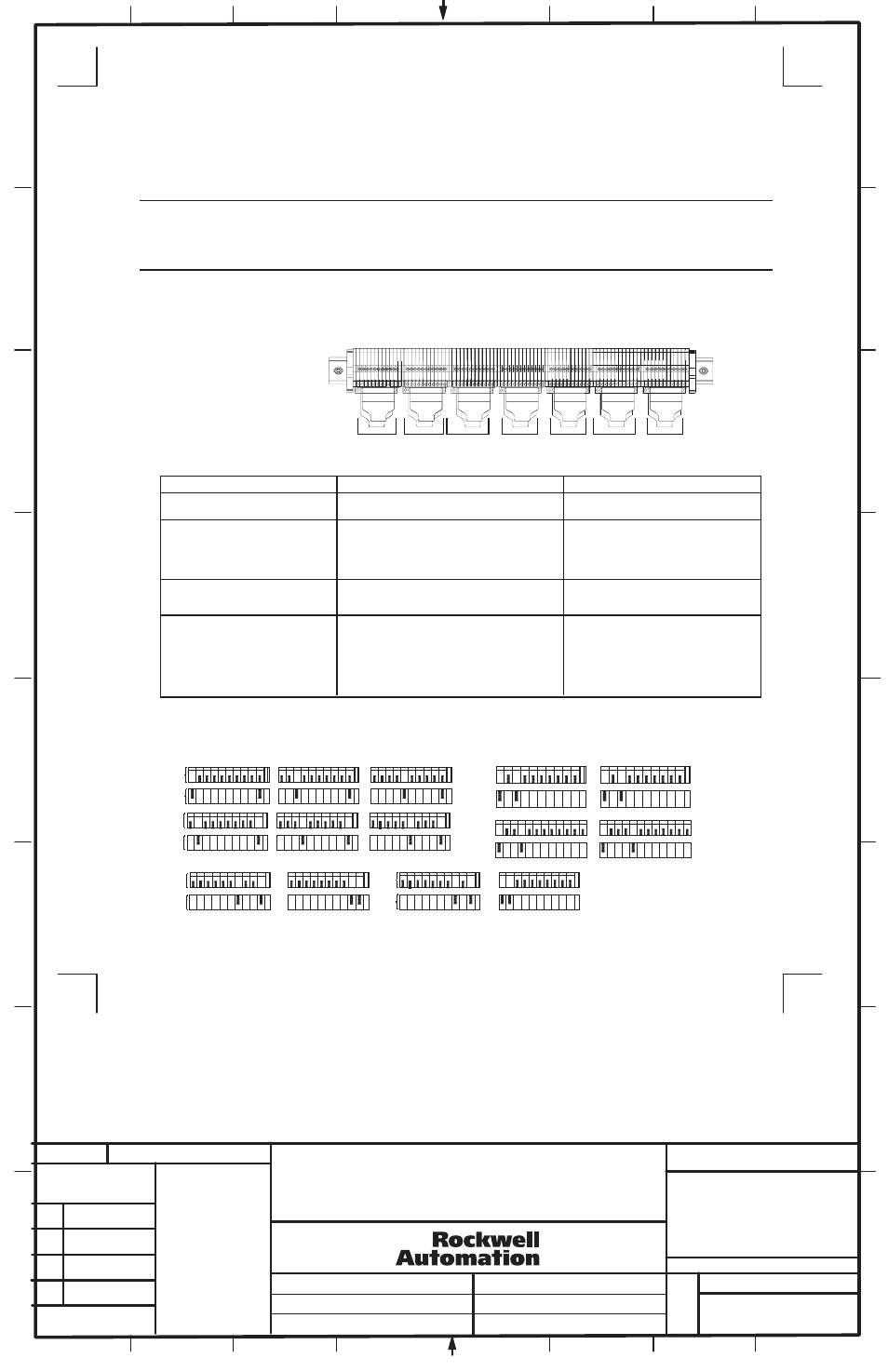
Section 2
Installation of an Enclosed System Multiplexer / Permissive Module
To install a factory or customer enclosed System Multiplexer / Permissive Module, perform the following steps:
1. Determine a suitable location for mounting the System Multiplexer / Permissive Module enclosure.
2. Based on the enclosure selected, locate and mark the necessary mounting bolt hole locations on the mounting surface. Drill and tap as needed
for mounting bolts suitable for the support of the enclosed System Multiplexer / Permissive Module.
IMPORTANT: Before mounting an enclosed System Multiplexer / Permissive Module and based upon installation requirements, the openings for conduit or cable
fittings should be made to the enclosure.
If enclosure is customer supplied, conduit or cable fitting openings should be made before installing the open style System Multiplexer / Permissive Module in the
enclosure. This should be done to avoid contaminating the module with fabricating debris.
If enclosure is factory supplied, the System Multiplexer / Permissive Module should be removed from the enclosure, prior to making any openings for conduit or
cable fittings, to help avoid module contamination (see Section 1 for instructions on removing the System Multiplexer / Permissive Module from an enclosure).
3. Support the enclosure while aligning it with the mounting bolt holes.
4. Install enclosure mounting bolts and tighten to torque required for mounting bolt size selected.
5. Mount the System Multiplexer / Permissive Module inside the enclosure (see Section 1 for instructions on installing the System Multiplexer /
Permissive in an enclosure).
6. Select which System Multiplexer / Permissive Module connector plugs will require wiring (see Table 1 and Figures 1 and 3).
Connector
RLS S#_A thru RLS S#__F
System Multiplexer / Permissive Module Remote
Lockout Station
C o n n e c t s R e m o t e L o c k o u t S t a t i o n t o
System Multiplexer / Permissive Module.
EXB1 THRU EXB4
S y s t e m M u l t i p l e x e r / P e r m i s s i v e M o d u l e
Connectors to ElectroGuard® Systems (See
Section 3)
Permissive inputs from the PLC and safety relay
output status
The permissive input allows the machine
controlling the process or drive system to
b r i n g t h e m a c h i n o r p r o c e s s t o a
predetermined stopping point prior to
removal of power by the ElectroGuard®
system. Output terminals provide the
status of safety relays SR1 and SR7.
PLC1EXB
PER1
Remote Lockout Station status to customer
remote PLC (See Section 5)
Connects RLS auxiliary signals to Remote
P L C o r o p t i o n a l R e m o t e I / O o r
Communication Modules.
Interconnects the System Multiplexer /
Permissive Module to the Control Modules
in ElectroGuard® Systems, or to series
connected System Multiplexer / Permissive
Module.
Description
Function
(2)
Table 1
System Multiplexer / Permissive Module Connectors
Figure 1
Connectors in
4 Port System Multiplexer /
Permissive Module
RLS_A
RLS_B
RLS_C
RLS_D
RLS_E
RLS_F
EXB1
EXB2
EXB3
EXB4
PLC1EXB
PLC2EXB
PER1
PER2
Figure 2
Keying of RLS Connectors at System Multiplexer / Permissive Module
The connectors at System Multiplexer / Permissive Module are "Keyed" in order to uniquely identify each connector, in the event they are
removed and re-inserted (See Figure 2).
7. Follow the specified System Multiplexer / Permissive Module Connector's section (Table 1) to wire connectors.
SYSTEM MULTIPLEXER / PERMISSIVE MODULE
INSTALLATION INSTRUCTIONS
1
1024403
42052-164
OF
N/A
N/A
N/A
REVISION
AUTHORIZATION
DR.
CHKD.
APPD.
DATE
DATE
DATE
E - DOC
LOCATION: MILWAUKEE, WISCONSIN U.S.A.
B-vertical.ai
DWG.
SIZE
SHEET
B
1
2
3
4
5
6
7
8
A
B
C
D
E
F
G
H
REFERENCE
DIMENSIONS APPLY BEFORE
SURFACE TREATMENT
(DIMENSIONS IN INCHES)
TOLERANCES UNLESS
OTHERWISE SPECIFIED
.XX:
.XXX:
ANGLES:
42052
------------
----------
----------
----------
------------
------------
2
8
THIS DRAWING IS THE PROPERTY OF
ROCKWELL AUTOMATION, INC.
OR ITS SUBSIDIARIES AND MAY NOT BE COPIED,
USED OR DISCLOSED FOR ANY PURPOSE
EXCEPT AS AUTHORIZED IN WRITING BY
ROCKWELL AUTOMATION, INC.
RLS_A
RLS_C
RLS_E
PER1
PLC1 EXB
PLC2 EXB
RLS_B
RLS_D
RLS_F
EXB1
EXB2
EXB3
EXB4
T
1
2
3
4
5
6
7
8
9
G
N
D
10
1
2
3
4
5
6
7
8
9
G
N
D
10
1
2
3
4
5
6
7
8
9
G
N
D
10
1
2
3
4
5
6
7
8
9
G
N
D
10
1
2
3
4
5
6
7
8
9
G
N
D
10
1
2
3
4
5
6
7
8
9
G
N
D
10
1
2
3
4
5
6
7
8
9
G
N
D
10
1
2
3
4
5
6
7
8
9
G
N
D
10
8
1
2
3
4
5
6
7
9
G
N
D
10
PER2
8
1
2
3
4
5
6
7
9
G
N
D
G
N
D
10
8
1
2
3
4
5
6
7
9
10
11
12
8
1
2
3
4
5
6
7
9
10
11
12
1
2
3
4
5
6
7
8
9
G
N
D
10
1
2
3
4
5
6
7
8
9
G
N
D
10
B
P
L
U
G
T
B
P
L
U
G
T
B
P
L
U
G
T
B
P
L
U
G