S&S Cycle Sidewinder 3 5⁄8 Big Bore Cylinders for Harley-Davidson Sportster Models—1986–2003 User Manual
Page 14
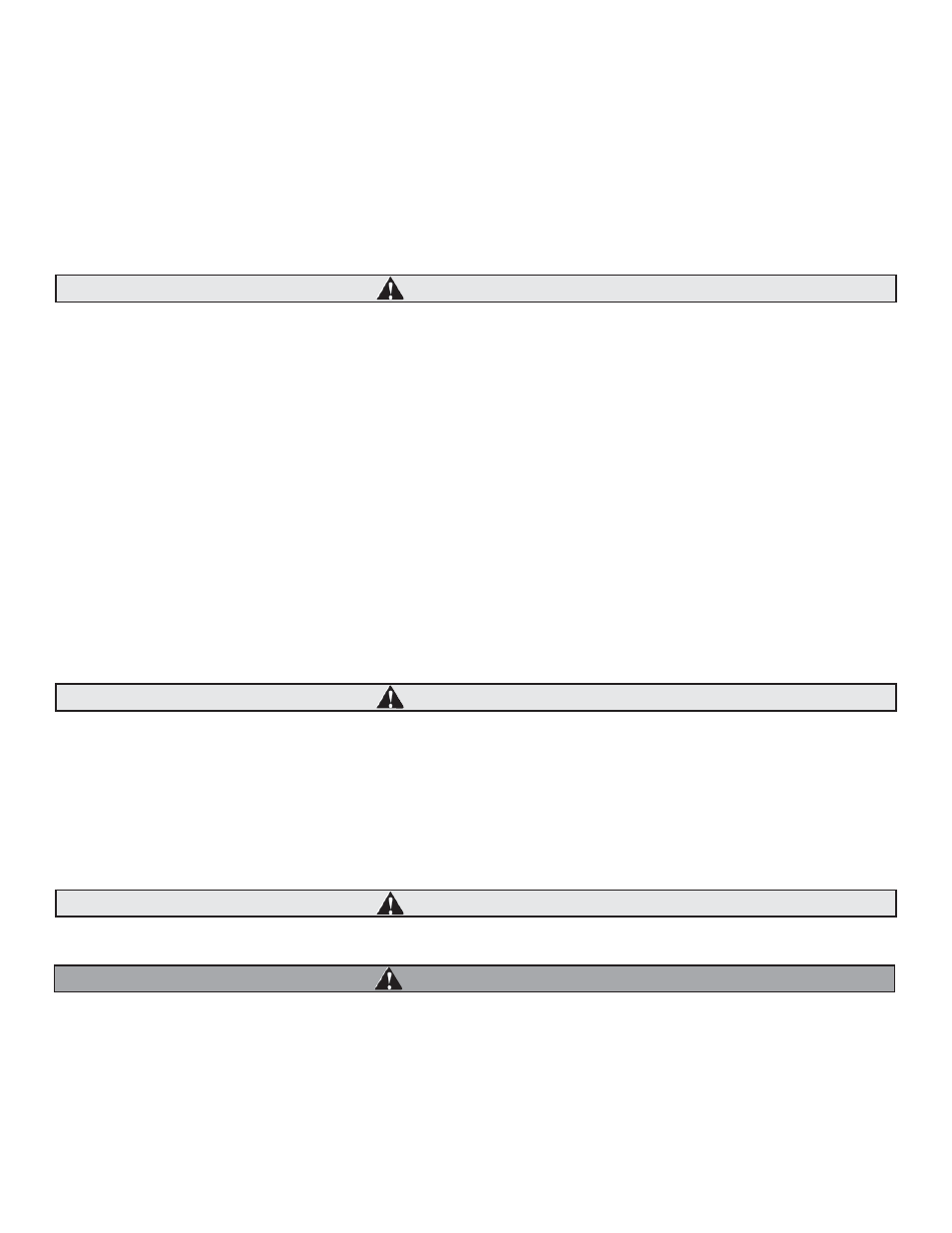
14
B. Piston to Valve Clearance
1. Turn engine over until piston in front cylinder is at top dead center. Paint area around valve pockets on pistons with machinist’s blue.
2. Place valves in cylinder head leaving off springs and retainers. Place head on cylinder and secure with one bolt.
3. Lower valves until they contact piston. Rotate valve marking painted area.
4. Remove head and check points of contact. Valve should fit in recessed area machined in piston dome.
NOTE: S&S recommends at least .060" clearance around periphery of valve.
5. If insufficient clearance exists, remove piston and grind valve pocket until head of valve fits flush with proper clearance. Clean parts
thoroughly before reassembly.
Do not remove more material than needed when performing piston to valve clearancing. Removal of excessive amounts of material
may weaken top ring land of piston causing piston breakage and serious engine damage.
6. Repeat procedure for other cylinder head.
7. Spread layer of putty into valve pockets in both pistons.
8. Assemble cylinder heads and bolt assemblies on cylinders with head gaskets in place. Install pushrods and adjust to simulate final
assembly.
NOTE: If hydraulic lifters are used, pushrods should be adjusted so that lifters are completely collapsed for this test. This will insure that lifters do not
collapse due to valve spring pressure, and that full valve lift is achieved.
9. Turn engine over in normal direction of travel two complete revolutions.
10. Remove cylinder heads and check thickness of putty in valve pockets.
11. If clearance is sufficient, disassemble top end and proceed to final assembly.
12. If less than .060" clearance in any area exists, remove piston from engine and grind area until proper clearance is achieved. Clean
parts thoroughly before reassembly.
NOTE: S&S® recommends at least .060" clearance between valve and piston valve pocket recess. While .060" clearance is recommended minimum, it is
advisable to have more, if possible.
Insufficient clearance between piston and valves may cause them to contact each other during operation resulting in damage to piston
and valve train components.
13. Final Assembly and Engine Installation
NOTE: Cleaning parts prior to and during assembly and keeping parts clean after final assembly are imperative to minimize contaminants that may
circulate in oil and shorten engine life. Many parts can be cleaned with soap and water first. Then, reclean all internal parts and gasket mating
surfaces using high quality solvent that does not leave any harmful residues. Be sure to read and follow manufacturer’s instruction label before
use. Use drills and compressed air to clean all oil passageways of dirt, filings, etc. whenever possible. During actual final assembly, recoat all
internal parts with high quality engine oil or assembly lube such as S&S 51-9000.
Manufacturing chips, dirt and/or other contaminants circulating in engine oil may possibly damage engine components resulting in
shorter engine life and possible engine failure.
• Some solvents, degreasers and other chemicals are harmful to skin, eyes and other body parts. Many items are flammable and
present a fire hazard. Read manufacturer’s instruction label for proper use. Use in well ventilated area and wear protective clothing
when using them to avoid personal injury.
• Compressed air and particles dislodged by compressed air are harmful to eyes and body. Wear protective goggles when using
compressed air and always direct air stream away from body parts such as hands and eyes. Never direct compressed air toward other
people.
A Spin each head bolt down on its respective stud to be sure threads are clean and free of contamination.
B. Install cylinder base gaskets provided dry. Be sure gaskets match cylinder base line-up dowels and oil return passageways.
CAUTION
CAUTION
CAUTION
WARNING