Pololu 3pi Robot User Manual
Page 28
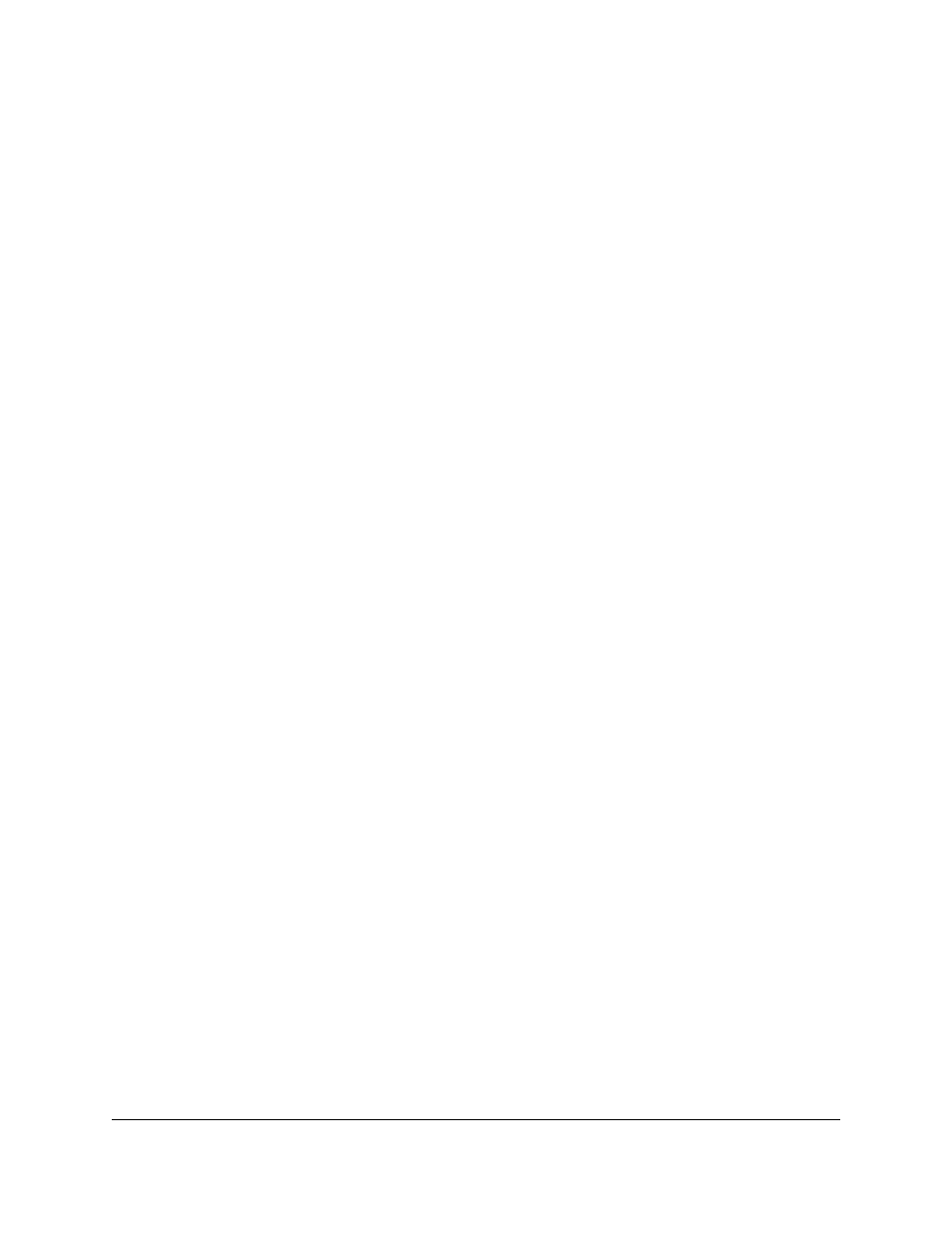
// Compute the derivative (change) and integral (sum) of the
// position.
int derivative = proportional - last_proportional;
integral += proportional;
// Remember the last position.
last_proportional = proportional;
Note that we cast the variable
position
to an int type in the formula for proportional. An unsigned int can only
store positive values, so the expression
position-2000
, without casting, would lead to a negative overflow. In this
particular case, it actually wouldn’t affect the results, but it is always a good idea to use casting to avoid unexpected
behavior.
Each of these input values provides a different kind of information. The next step is a simple formula that combines
all of the values into one variable, which is then used to determine the motor speeds:
// Compute the difference between the two motor power settings,
// m1 - m2. If this is a positive number the robot will turn
// to the right. If it is a negative number, the robot will
// turn to the left, and the magnitude of the number determines
// the sharpness of the turn.
int power_difference = proportional/20 + integral/10000 + derivative*3/2;
// Compute the actual motor settings. We never set either motor
// to a negative value.
const int max = 60;
if(power_difference > max)
power_difference = max;
if(power_difference < -max)
power_difference = -max;
if(power_difference < 0)
set_motors(max+power_difference, max);
else
set_motors(max, max-power_difference);
The values 1/20, 1/10000, and 3/2 represent adjustable parameters that determine how your 3pi will react to the line.
The particular values chosen for this example were somewhat arbitrarily picked, and while they work sufficiently for
typical line following, there is plenty of room to improve them. In general, increasing these PID parameters will make
power_difference
larger, causing stronger reactions, while decreasing them will make the reactions weaker. It’s up
to you to think about the different values and experiment with your robot to determine what effect each parameter has.
This example gives the motors a maximum speed of 100, which is a safe initial value. Once you have adjusted the
parameters to work well at a speed of 100, try increasing the speed. You’ll probably need to readjust the parameters
as the maximum speed increases. By gradually increasing the maximum speed and tuning the parameters, see if you
can get your 3pi to run as fast as possible! We have been able to run 3pis with a maximum speed of 255 on courses
with 6"-radius curves, all by finding the right PID parameters.
Please see
of the
gallery for videos of 3pi line followers
using tuned PID and higher maximum speeds.
Pololu 3pi Robot User's Guide
© 2001–2014 Pololu Corporation
7. Example Project #1: Line Following
Page 28 of 63