Maintenance – Multiquip MQ600TD80 User Manual
Page 29
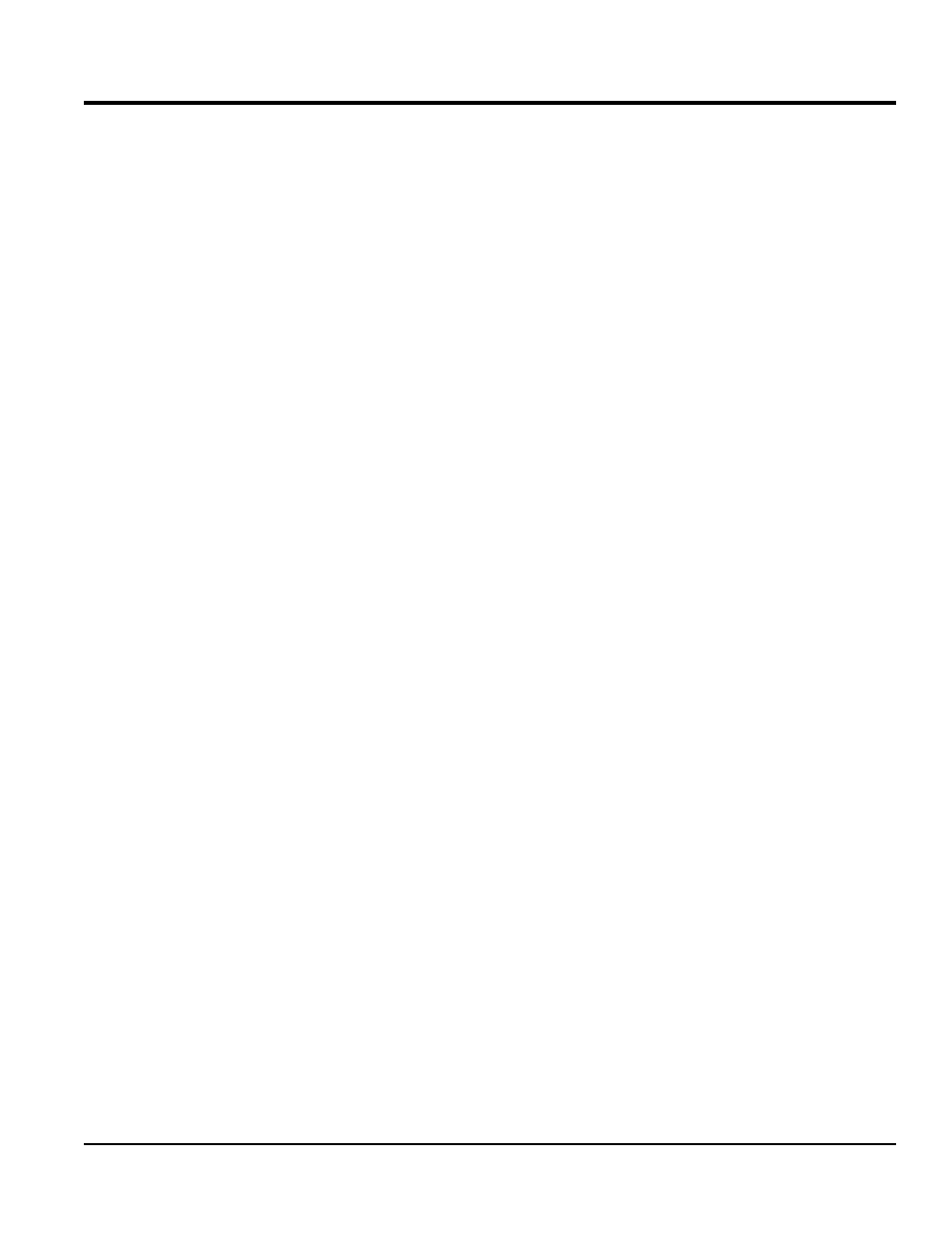
mq600Td80 TRaSH pUmp• opeRaTion and paRTS manUal — Rev. #11 (10/10/11) — page 29
Maintenance
pUmp mainTenanCe
This section is intended for the experienced, qualified
technician as a guideline to service the pump. All service
precautions must be observed to avoid injury. Read and
understand all safety information and the operation section.
Before servicing this equipment be sure to do the following:
1. Turn off the engine
2. Follow lock out procedures.
3. Vent the pump cautiously.
4. Drain the pump.
5. Allow the pump to cool if overheated.
6. Use appropriate lifting devices.
mechanical Seal Replacement instructions
Disassembly
1. It is recommended to remove the main casing body.
2. Remove the impeller by first locking (using a wrench)
the front engine crankshaft pulley.
3. Using a soft-faced mallet, remove impeller by tapping
vane in counterclockwise direction.
4. Remove mechanical seal components.
5. Remove the rear adaptor cover, sight glass, and vent
tubes.
6. Using a punch, remove adaptor plate mechanical seal
stationary seal plate.
7. Remove stationary oil seal.
Installation
1. Install new stationary oil seal into adaptor case
housing. The seal spring should face inward towards
the impeller.
2. Lightly lubricate the mechanical seal stationary seal
plate O-ring and gently tap into adaptor plate making
sure it is level with the O-ring groove facing the
impeller.
3. Install the adaptor plate bolting onto the intermediate
bearing housing.
4. Inside the adaptor plate cavity, assemble the stationary
plate by installing the O-ring then the tungsten carbide
stationary element squarely onto the stationary seal
plate. (Note: Tungsten element chamfer side towards
pump end). A slight amount of grease can be used to
allow retention. Double check that the Tungsten carbide
element surface is free of dirt contamination including
fingerprints.
5. Coat the mechanical seal bellows with a light drop of
lubricating oil. Slide the seal bellows onto the shaft
sleeve until flush with the sleeves chamfered end.
Place the Tungsten carbide rotating element onto seal
cage, the chamfered side towards engine. Inspect the
rotating Tungsten for cleanliness. Use a slight amount
of grease for retention. Carefully push and rotate the
sleeve assembly onto the shaft until the Tungsten
element faces are mated. The sleeve should firmly
rest against the shaft shoulder. Use extreme care not
to damage or roll over the oil seal lip.
6.
Alternative mechanical seal installation method —
After installation of adaptor plate assembly, slide the
sleeve chamfered side toward engine. Use extreme
care not to damage the oil seal. Utilize secondary
sleeve as installation tool, installing over shaft butting
against primary sleeve. Lubricate seal bellows slowly
sliding seal assembly onto primary sleeve until the
Tungsten carbide faces are squarely mated. Remove
installation tool.
7. Assemble the spring then add the necessary
adjustment shims.
8. Inspect the impeller and shaft threads and make sure
they are clean before installation. Apply "Anti-Seize"
compound. Even the slightest amount of dirt on the
thread can cause the impeller to seize or make future
removal difficult. At the slightest sign of binding,
immediately back impeller off inspecting threads. Do
not force the impeller onto the shaft. The impeller rear
to adaptor plate clearance is 0.25 - 0.40 inches (0.64
- 1.02 mm). Make positively sure that the impeller is
fully tightened utilizing all the threads. If not properly
tightened, the impeller could further tighten jamming
into the adaptor plate during pump operation, seizing
the engine.
9. Reinstall the main pump body, checking for proper wear
plate to impeller clearance.