Det-Tronics MOS H2S Gas Sensor User Manual
Page 22
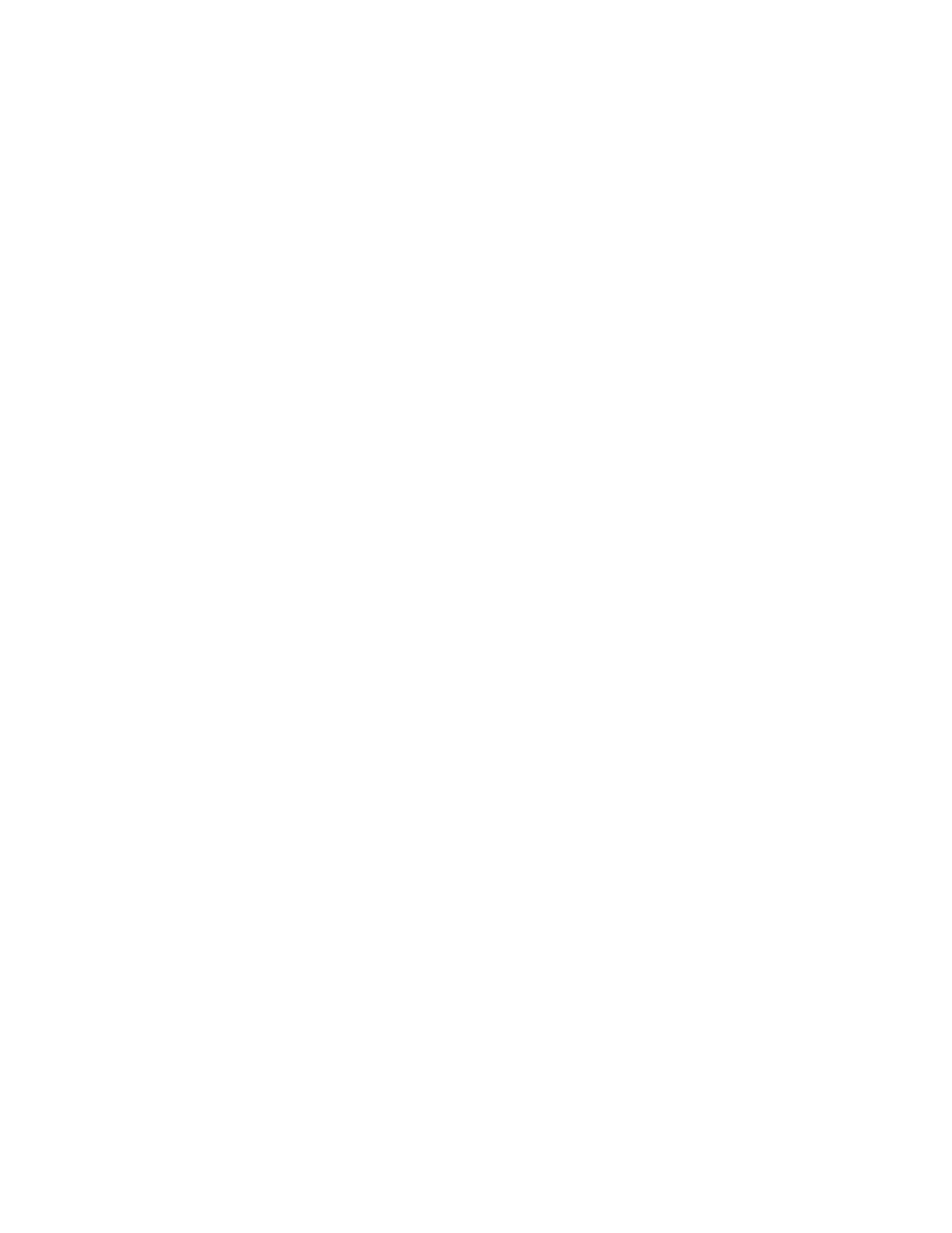
95-8532
1.4
20
MAINTENANCE
A routine maintenance schedule is recommended to
ensure that the detector is in peak operating condition at
all times. To ensure top performance, service the device
as follows.
VISUaL INSpECTION
A visual inspection of the detector approximately once
per week is recommended to ensure that physical
obstructions such as trash, debris, mud, snow, or oil
have not blocked or impeded hazardous gas access to
the sensor. This includes visually inspecting the sintered
metal filter on the sensor.
RESpONSE TEST
It is acceptable to perform a detector response
verification test in lieu of a complete calibration if the
detector output in clean air appears stable and the
device has been calibrated recently. This test involves
simply applying calibration gas to the detector while in
normal operating mode and confirming that the detector
output is proportional to the applied gas concentration.
It is the operator’s responsibility to bypass any and all
system alarm output devices, if necessary, prior to
conducting the detector response test. If the response
test results are not acceptable, a complete calibration
must be performed.
NOTE
Fault detection circuitry continuously monitors
for problems that could prevent proper system
response. It does not monitor external response
equipment or the wiring to these devices. It is
important that these devices be checked initially
when the system is installed, as well as periodically
during the ongoing maintenance program.
The system must be checked periodically in
the Normal mode to ensure that those items not
checked by the transmitter diagnostic circuitry
(such as output relays) are functioning properly.
CaLIbRaTION
Calibrate the detector following the schedule in the
“Calibration” section of this manual.
SINTERED METaL fILTER
H
2
S gas enters the sensor through the sintered metal
filter on the front of the sensor housing. A dirty filter can
significantly reduce the amount of H
2
S gas that is able to
reach the sensing element, thereby impairing the ability
of the system to respond to a hazardous condition. If the
filter becomes dirty and cannot be properly cleaned or if
it is damaged, the sensor must be replaced.
NOTE
If the detector cannot be calibrated or responds
slowly to the calibration gas, check the condition of
the filter before replacing the sensor.
SENSOR REpLaCEMENT
The MOS sensor is not field repairable. If calibration can
no longer be properly performed, the sensor must be
replaced.
The area must be de-classified or power to the detector
should be removed prior to replacing the sensor in a
hazardous area.
Follow the procedure below to replace the sensor.
Remove power to the transmitter prior to replacing
1.
the sensor.
Remove the transmitter cover and the wire shield
2.
within the transmitter.
Unplug the sensor from the transmitter module and
3.
unscrew it from the conduit entry.
Thread the wires for the replacement sensor through
4.
the conduit entry, then screw the sensor into the
conduit entry and plug it in. Replace the wire
shield.
Replace the junction box cover.
5.
Re-apply power. Allow time for the unit to warm
6.
up and stabilize (approximately 24 hours for best
results), then calibrate.
An adequate supply of spare sensors should be kept
on hand for field replacement. For maximum protection
against contamination and deterioration, they should not
be removed from the original protective packaging until
the time of installation. To ensure maximum storage life,
sensors should be stored at a temperature between 32°F
and 68°F (0 to 20°C) and a relative humidity between
15 and 90 percent. Always calibrate after replacing the
sensor.