Det-Tronics PIR9400 PointWatch Infrared Hydrocarbon Gas Detector User Manual
Page 21
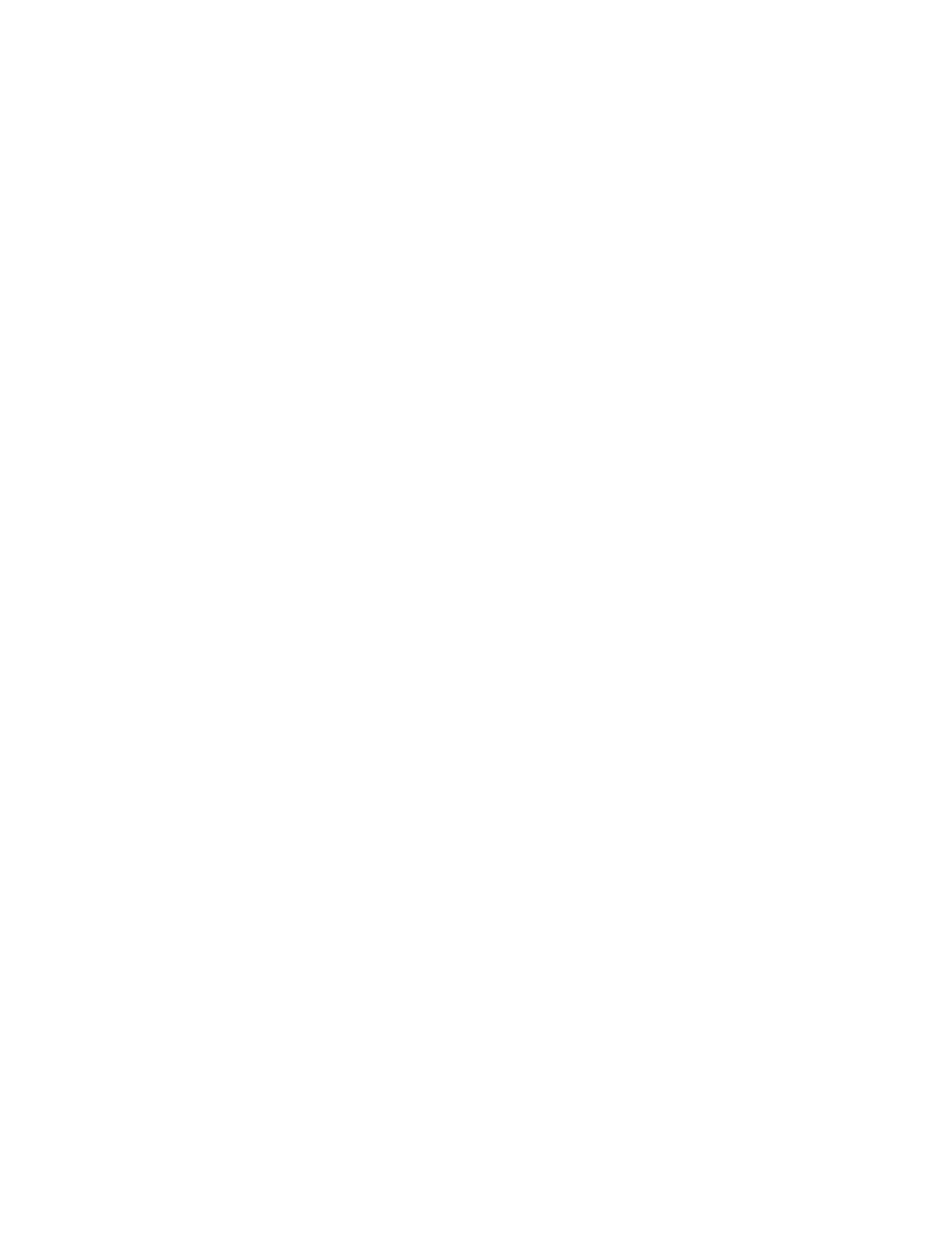
19
95-8440
9.3
4. Connect the calibration gas canister, valve and
tubing to the direct input nozzle as shown in either
Figure
24
(aluminum model) or Figure
25
(stainless
steel model) depending on the method used.
5. Apply
50%
LFL calibration gas to the detector.
This is accomplished by opening the valve on the
calibration gas canister (see Figure
24
or Figure
25
).
A
2.5
liter per minute flow rate is recommended.
– The LED will continue flashing
– The current output will increase proportionally as
the gas concentration increases.
6. The detector will automatically accept the span
calibration when the detected gas level is stable
(typically
1
to
2
minutes).
After successful span calibration:
– The LED will turn off steady
– The current will lock in steadily at
12.0
mA,
indicating a successful span calibration.
Proceed to step
7
.
If for any reason a successful calibration is not
accomplished within
10
minutes, a calibration fault
will occur:
– The LED will turn off
– The current output will drop to 1.6 mA.
Turn off the gas, then reset the detector by cycling
power to the detector or by holding the Cal Magnet
near the Cal Switch. Begin the calibration sequence
again at step
1
.
7. After successful calibration, close the valve on
the calibration gas canister, remove the flexible
tube from the calibration nozzle and replace the
nozzle cap. If the calibration wind shield was used,
remove it from the detector. After the detector
output falls below
45%
LFL, the current loop
will unlock and will track the declining gas
concentration back to
4
mA.
iMPoRtant
The calibration ports must be capped to prevent
dirt and water from entering the direct path into the
optics. Failure to protect the optics can result in
a fouled optics fault. If a permanent gas delivery
system is used, the delivery tube must be plugged
when not in use.
MAINTENANCE
The PointWatch Detector requires less routine
maintenance than other combustible gas detectors.
This is accomplished through its design that allows no
undisclosed internal failures, and an optics protection
system that is extremely resistant to fouling by external
contamination. The most significant benefit of this design
is reduced calibration requirements. When installed
and used per the manufacturer’s recommendations,
the Model PIR
9400
Detector does not require routine
calibration, although an annual calibration inspection
is recommended as a good practice. More frequent
calibrations may be performed at the discretion of the
user without adverse impact.
Other recommended maintenance practices include
periodic visual inspections of the sensor and/or weather
protection system. External contaminants and/or debris,
if allowed to accumulate, can reduce sensitivity by
physically blocking vapor access to the sensor. Common
examples include plastic bags, litter, heavy oil and tar,
paint, mud, and snow. This simple visual inspection of
all gas sensors is a good idea, especially for outdoor
installations.
In the unlikely event that the PIR
9400
indicates a
fouled optics condition, it is possible to disassemble
and clean the optics. However, it is recommended that
a spare device be kept on hand to enable complete
exchange of the electronics/optics module in the field,
enabling the disassembly and cleaning operation to
be performed in a clean lab environment.
iMPoRtant MaintEnanCE notES
• use only low vapor pressure silicone grease when
lubricating threads on the PointWatch Detector
and associated termination box. Do not get this
grease on the optics of the detector. A suitable grease
is listed in the “Spare Parts” section at the end of this
manual. Do not use Hydrocarbon-based grease.
Doing so will emit hydrocarbon vapors that will be
measured by the detector, resulting in inaccurate gas
level readings.
• In applications where both PIR
9400
and catalytic
type sensors are used, ensure that the silicone
grease used to lubricate the detector threads does
not come into contact with the catalytic sensors or
poisoning of the catalytic sensors will result. It is
strongly recommended that maintenance personnel
wash their hands between handling the two types of
sensors.