AMMCO 7700 Drum and Disc Brake lathe User Manual
Page 16
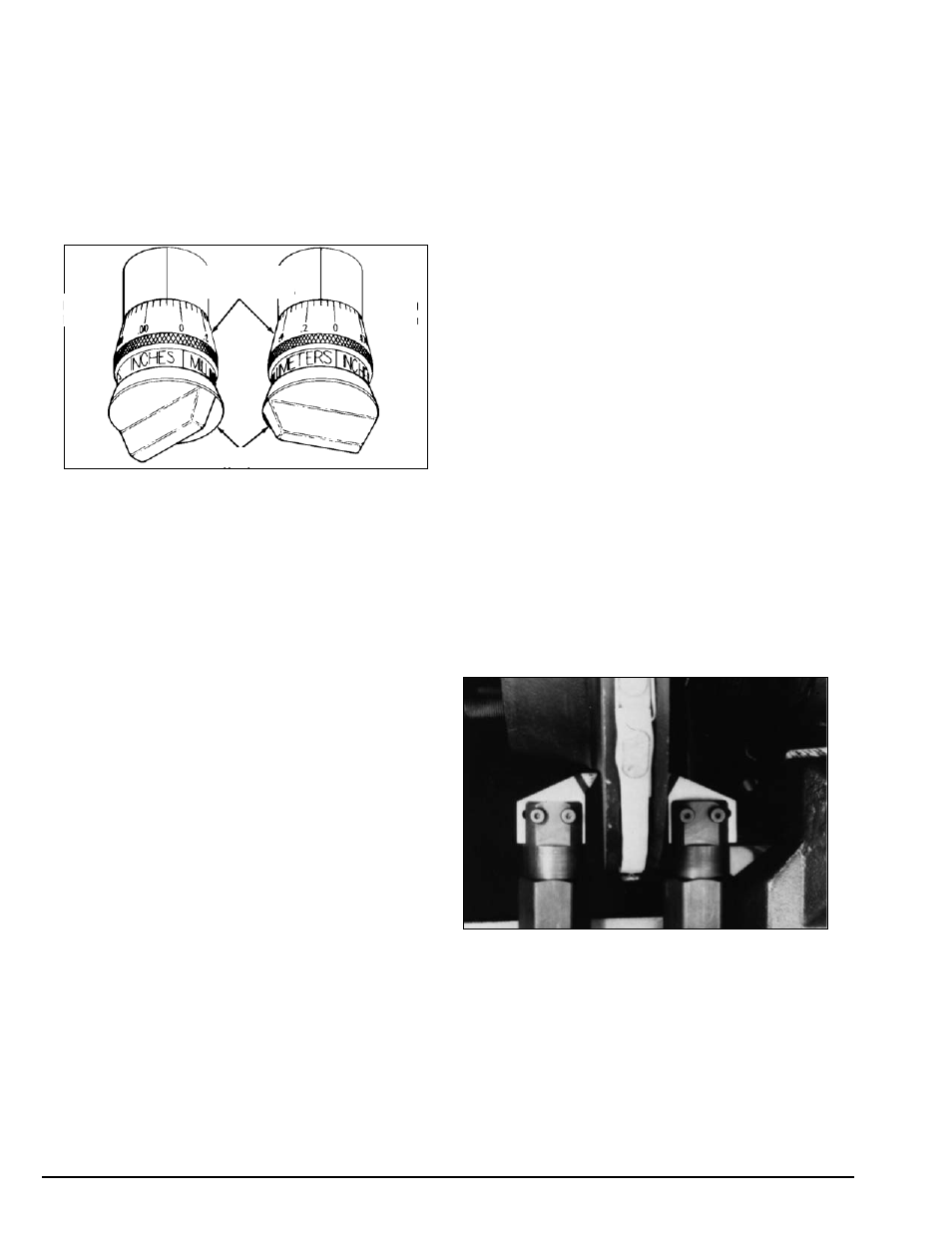
12 • AMMCO Drum & Disc Brake Lathes
Model 7900 Twin Cutter – 4100
The 7900 twin cutter mounts on the cross feed tool
post to resurface both rotor surfaces simultaneously.
Each tool bar is individually adjustable (in thousandths
of an inch or millimeters) to permit precise depth-of-cut
settings.
The tool bars mount on top of the tool bar support,
carbide tips up, and are used to recondition both brake
surfaces of a rotor at the same time.
Figure 31 – 7900 twin cutter controls
Installation
1.
Remove the self-aligning nut/washer assembly
retaining the boring bar clamp.
2.
Remove the clamp and boring bar.
Note: Older lathes have a tool post pivot screw which
must be loosened before the lower clamp can be
removed.
3.
Place the tool bar support over the cross feed tool
post stud and replace self-aligning nut/washer assem-
bly.
4.
Align the tool bar support parallel with the arbor
and wrench tighten the nut.
Preparation
1.
Inspect the rotor carefully for scoring, rust ridges
(at the inner and outer circumference of the rotor), and
hard spots. Any excessive wear or deformity should be
noted and, if not within acceptable limits, the rotor
should be replaced.
2.
Use a micrometer to check the thickness of the
rotor at no less than 3 points around the circumference
about 1” (2.54 mm) in from the outer diameter.
If the rotor thickness varies between readings, it
should be reconditioned. However, if the thickness is
less than the minimum established by the manufac-
turer, or if it will be less after reconditioning, the rotor
should be replaced.
Note: Most often the DISCARD thickness dimension
is cast or stamped into the rotor, not the minimum
machine-to thickness.
Rotor Mounting
Follow the rotor mounting guidelines and examples
provided on pages 10 and 11 and mount the rotor on
the arbor.
Set Up and Reconditioning Rotors
1.
Install a weighted silencer band on vented rotors,
a non-weighted silencer band on non-vented rotors, or
an optional friction rotor silencer to dampen vibrations
during machining.
2.
Use the cross feed handwheel to position the tool
bar support about
1
2
” from the rotor or silencer band.
3.
Loosen the tool post nut and center the tool bar
support to the rotor. Wrench tighten the nut.
If the tool bar support cannot be centered with the
rotor by moving the tool bar support, it may be neces-
sary to move the rotor in or out by using the spindle
feed handwheel to make the adjustment.
4.
Install the tool bar, carbide tip up, on the right side
of the rotor slide with the T-bolt and clamp. Slide the
tool bar into the clamp.
5.
Repeat step 4 for the left side tool bar.
6.
Turn the end knob of each tool bar micrometer
counterclockwise to fully withdraw the tool bit holders.
7.
Position the left tool bar approximately parallel to
the outer brake surface so that the tool bit is 1/8” away
from the brake surface and reaches to the groove at
the base of the brake surface. tighten the T-bolt nut.
8.
Repeat step 7 for the right tool bar.
Figure 32 – Positioning the tool bars
9.
Turn the cross feed handwheel counterclockwise
until the tool bits are about
1
2
” in from the outer edge
of the brake surface.
10.
Turn the lathe ON.
11.
Turn the end knob on the left boring bar microm-
eter clockwise to advance the tool bit until it lightly con-
tacts the outer brake surface and makes a scratch cut.
Inch/Millimeter
Micrometer Dials
Set to
0.004”
Set to
0.1 mm
Adjustment Knobs