1 pressure checks and adjustments, 4 hydraulic circuits, 1 hydraulic pressures – JLG G12-55A Service Manual User Manual
Page 120: Hydraulic circuits, To section 8.4, “hydraulic, Circuits, Section 8.4, “hydraulic, To section 8.3.1, “pressure checks and adjustments, Pressure checks and adjustments, Hydraulic pressures
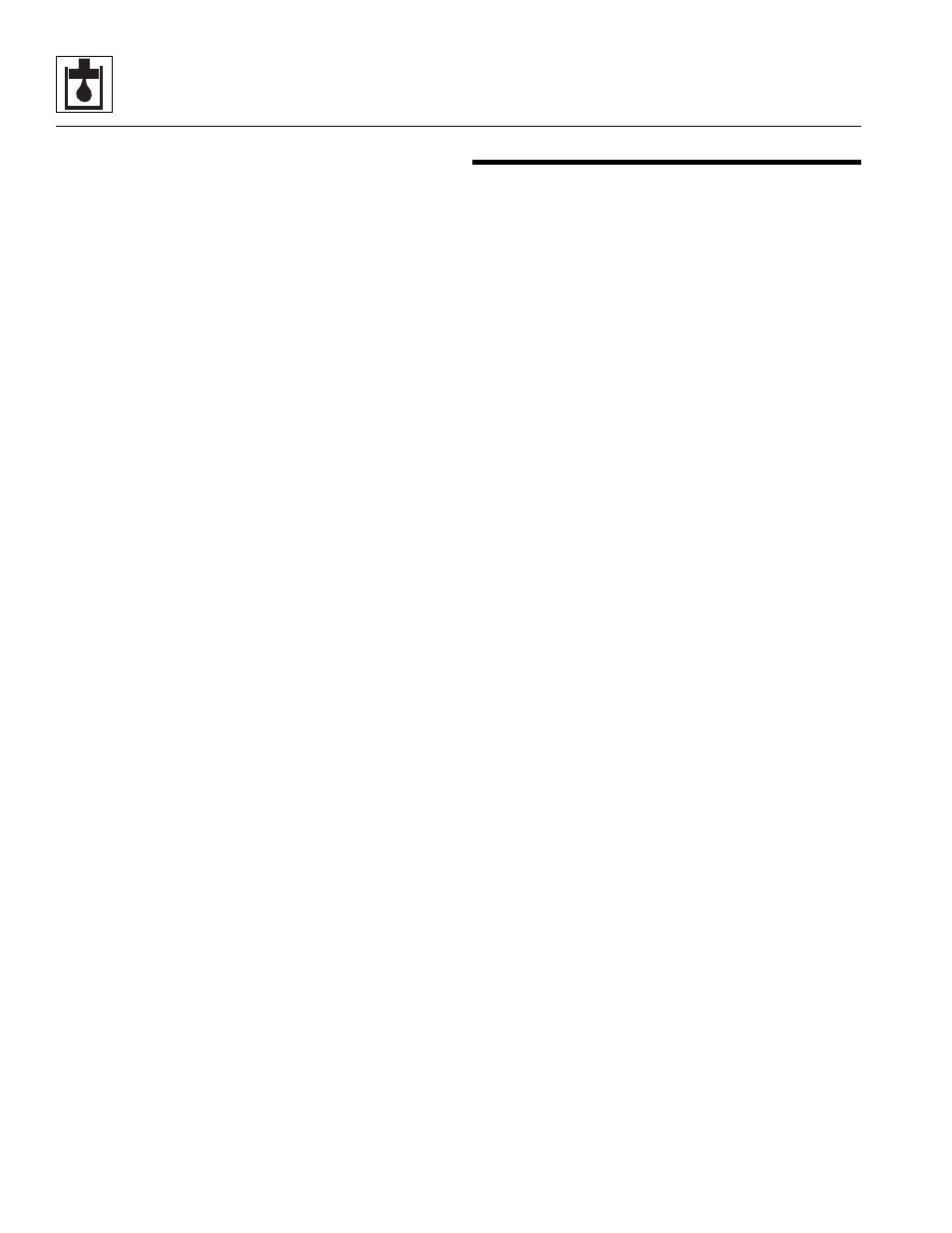
Hydraulic System
8-4
G10-55A, G12-55A
8.3.1
Pressure Checks and Adjustments
When diagnosing trouble in the hydraulic system, use the
hydraulic testing information in Section 8.4.1, “ Hydraulic
Pressures.”
In general, follow the steps below whenever conducting
pressure checks and performing adjustments:
1. Park the machine on a firm, level surface. Engage
the park brake, place the travel select lever in (N)
NEUTRAL, level the boom and turn the engine OFF.
2. The test port is located at the top right corner of the
main control valve. Install a pressure gauge capable
of measuring at least 10% more pressure than that
which the circuit being checked operates under.
3. Start the engine. Operate machine functions several
times to allow hydraulic oil to reach operating
temperature. The hydraulic oil temperature should
be between 100-120°F (38-49° C). If a temperature
gauge or thermometer is unavailable, the hydraulic
oil reservoir should be warm to the touch.
4. Refer to Section 8.4.1, “ Hydraulic Pressures.” for
testing procedures.
5. Fully depress the accelerator pedal if required. Place
and hold the joystick in the position needed to
operate the particular machine function being
checked. Continue holding the joystick in position
until pressure readings are taken.
6. Check the pressure gauge reading. It should read as
specified in the Pressure Readings column of the
charts found in Section 8.4.1, “ Hydraulic
Pressures.” If the reading is not as specified, turn the
engine OFF and check other components in the
system. Verify that all related hydraulic components
and electrical switches, sensors, solenoids, etc. are
operating correctly.
7. Adjust the relief valve by turning the adjustment
screw Turning clockwise will increase the pressure;
turning the screw counterclockwise will decrease the
pressure.
8. Start the engine and check the pressure again. Turn
the engine OFF. If there is pressure reading in the
gauge, bleed it off then disconnect or remove the
pressure gauge from the machine.
8.4
HYDRAULIC CIRCUITS
This section covers the hydraulic circuits and includes
listings for all hydraulic function pressures, where and
how to check those pressures and a hydraulic schematic.
Electrical and hydraulic functions are often related. Verify
that the electrical components of the circuit are
functioning properly whenever troubleshooting the
hydraulic circuit.
Always check the following before beginning to
troubleshoot a circuit that is not functioning correctly.
1. Check the hydraulic oil level in the reservoir. Oil level
should be to the middle of the sight glass with all
cylinders retracted.
2. Check hoses, tubes, fittings and other hydraulic
components for leaks, bends, kinks, interference, etc.
3. Check for air in the hydraulic system. Erratic machine
performance and/or spongy cylinder operation are
signs of air in the hydraulic system.
If air in the hydraulic system is suspected, you will
hear air leakage when hydraulic fittings are loosened
and see air bubbles in the hydraulic fluid.
Loose fittings, faulty o-rings or seals, trapped oil,
leaks, system opened for service, etc., can cause air
in the system. Determine what is causing air to enter
the system and correct it. Bleed air from the system.
8.4.1
Hydraulic Pressures
a. Checking Pressure
1. Start the machine and warm the hydraulic system to
operating temperature.
2. Shut off the machine and install a digital or a
5000 psi (345 bar) gauge to the appropriate test port
on the hydraulic manifold.
3. Start the machine, run the engine at high idle and
bottom the appropriate hydraulic function. Refer to
Section 8.4.1, “ Hydraulic Pressures.” for the correct
pressure rating.
b. Adjusting Hydraulic Pressure
1. Shut the machine off. Remove the cap on the relief
(if necessary).
2. Start the machine and loosen the jam nut on the
relief. Turn the relief clockwise to increase pressure
or counter-clockwise to decrease pressure. Set to
the correct pressure.