Flexible couplings, Propeller/wheel alignment, Propeller fan alignment – Aerovent IM-100 User Manual
Page 6
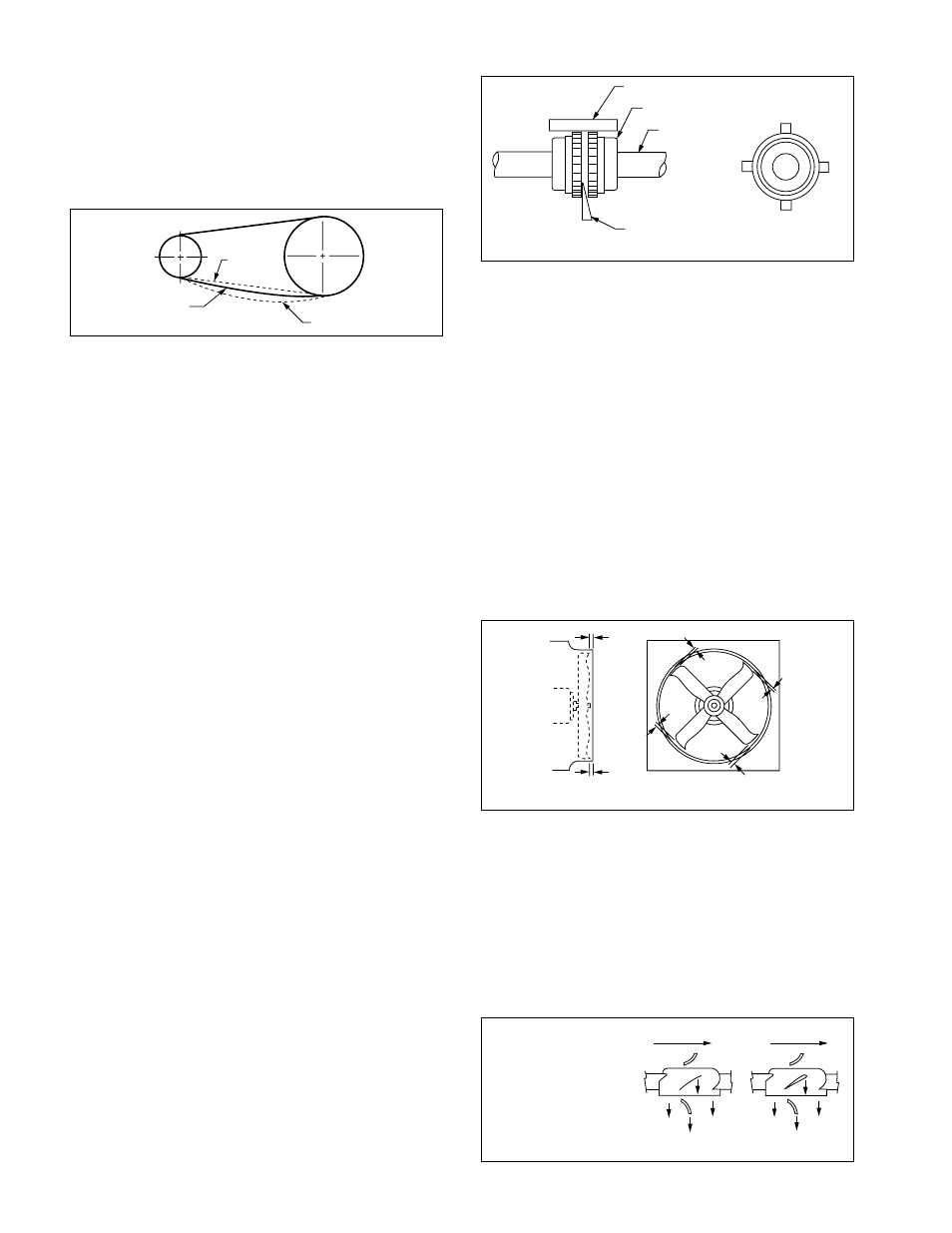
6
Aerovent IM-100
3. Sheaves must have no noticeable eccentricity.
4. Belts must have the proper tension. Belts either too
loose or too tight cause vibration and excessive wear
(Figure 5). See instructions for belt tension adjust-
ment procedure.
5. After proper installation of drives, recheck the com-
plete assembly for smoothness of operation.
Flexible Couplings
Direct-coupled fans, which are received factory assem-
bled, on a common base plate, are accurately aligned
before shipment. However, base plates are flexible to
some extent and therefore must not be relied upon to
maintain the factory alignment. Realignment is neces-
sary after the fan has been leveled, grouted, and the
foundation bolts tightened. Also, check the lubricant,
where applicable, following the manufacturer’s recom-
mendations for the type and amount of lubricant.
For field installation, the coupling should be mounted
as follows:
1. Remove dirt or rust from fan and motor shafts and
coat with grease or oil for ease of mounting.
2. Check fan and fan shaft alignment, making sure that
the bearings are secure. Mount the fan shaft cou-
pling half flush to the end of the shaft and secure.
3. Mount the motor shaft coupling half flush to the end
of the shaft and secure.
4. Move the motor into position, with the coupling faces
separated by the coupling manufacturer’s specified
gap.
5. With a straightedge, tapered wedge, or a feeler
gauge, check for parallel and angular alignment
(Figure 6a).
6. Align the shafts until a straightedge appears to be
parallel to the shafts. Repeat at three additional
points at approximately 90° from each other (Figure
6b). Recheck the hub separation gap.
7. For more accurate alignment, use a dial indicator
clamped on one hub. With the dial button resting on
the other hub, rotate the hub on which the indicator
is clamped and observe the indicator reading. Take
readings at four locations, 90° apart. With correct
alignment, the faces of the couplings should be par-
allel within 0.002".
8. Once proper alignment is assured, secure the motor,
examine the alignment, complete the assembly, and
lubricate the coupling (when required) before putting
the unit into operation.
Propeller/Wheel Alignment
Fans, which are received factory assembled, have the
propellers already aligned and in place before shipment.
However, fans being flexible to some extent are some-
times subject to movement during shipment. To insure
smooth operation and proper performance, the following
propeller alignment should be checked before putting a
fan into operation.
Propeller Fan Alignment
The fan shaft should be centered and parallel to the fan
casing. Center by checking gap (B) between the propel-
ler tip and the fan casing. Repeat at three additional
points at approximately 90° from each other (Figure
7b). Parallelism can be observed by measuring the
axial distance (A) from one blade to the end of the fan
casing at four points at approximately 90° from each
other (Figure 7a).
Do not confuse parallelism with blade track (axial
deviation of one blade to another). Blade track can be
checked by measuring the axial distance from one point
on the fan casing to the same point on each blade as it
passes by. (Some blades are mistracked for balancing.)
While checking the propeller alignment, it is good
practice to check its rotation. Normally the fan rotation
is marked by arrows on both the propeller and the fan
casing. If omitted, obliterated, or misapplied, check for
proper rotation as in Figure 8.
Figure 8. Checking for Proper Rotation
Too Loose
Slight Bow
Too
Tight
Figure 5. Proper Belt Tension
A
A
B
B
B
B
Figure 7. Propeller Fan Alignment
7a
7b
Figure 6. Flexible Coupling Alignment
Straightedge
Coupling
Shaft
Steel Wedge
3
1
2
4
6a
6b
Inlet
Guide Vanes
Outlet
Guide Vanes
Airflow
Airflow
Rotation
Rotation
RH rotation.
Vaneaxial shown.
Standard propellers
similar, but less
guide vanes.