Motors, Lubrication instructions for ball bearing motors, Common causes of excessive vibration – Aerovent IM-100 User Manual
Page 2: Procedure for relubrication, Type of grease
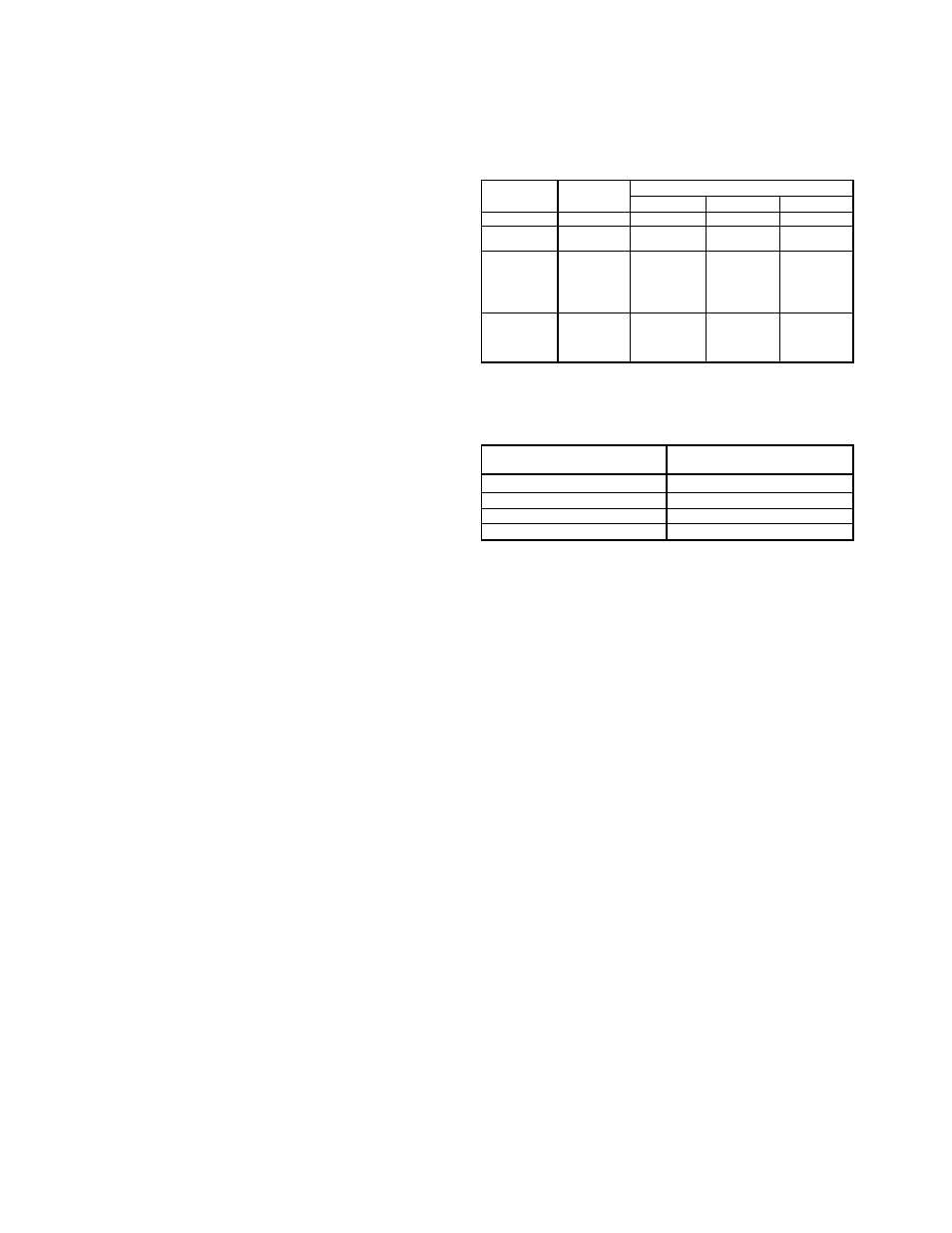
2
Aerovent IM-100
All Aerovent fan assemblies are statically and dynam-
ically balanced to Balance Quality Grade G6.3. Each
fan is factory run tested for vibration in accordance
with ANSI/AMCA 204-96 "Balance Quality and Vibration
Levels for Fans" to Fan Application Category BV-3, to
the following peak velocity values, filter-in, at the fan
test speed:
Fan Application
Rigidly Mtd.
Flexibly Mtd.
Category
(in./sec.)
(in./sec.)
BV-3
0.15
0.20
While fans are test run and carefully balanced in
the factory, vibration cannot be guaranteed under field
conditions due to mounting and installation variables.
Vibration measurements, when possible, should be
taken at each fan shaft bearing in two planes per-
pendicular to the axis of rotation (planes to have 90
degree interval), and one measurement parallel to the
axis of rotation. On direct drive units, the perpendicular
measurements will be taken at each end of the motor
casing, taking care not to take measurements on the
fan shroud on TEFC motors. The axial measurement
can be taken on the motor foot or mounting base. In
some cases, primarily on axial flow units, it will not
be possible to take measurements at the bearings or
motor. On these units, the measurements should be
taken on the inner shell near the bearings. If this is not
possible, then take the readings on the outer shell near
the bearing locations.
If vibration is excessive, shut down the fan and
determine the cause.
Common Causes of Excessive Vibration
1. Support structure not sufficiently rigid or level.
Vibration amplified by resonance in ductwork or sup-
port structure.
2. V-belt drive misalignment. Belt tension is too tight or
too loose.
3. Bearing locking collar or mounting bolts loose.
Propeller set screw loose.
4. Material accumulation on propeller.
5.
Centrifugal Fans: Wheel rubbing on inlet cone.
Motors
Most integral horsepower totally-enclosed motors have
drain plugs in the end bells for drainage of condensa-
tion. On all roof ventilators, the bottom or lower plug
has been removed for continuous drainage.
All other style fans are shipped with the drain plugs
installed. The user should remove the proper drain plug.
For horizontally mounted units with the motor in the
airstream, remove the downstream drain plug. For verti-
cally mounted units, remove the bottom or lower drain
plug.
With motors supplied by the user, drain plugs may
not have been provided. Check with the motor manu-
facturer regarding drainage and condensation.
Lubrication Instructions for Ball
Bearing Motors
Grease-lubricated bearings, as furnished, are adequate
for a long period of operation without relubrication. A
good maintenance schedule for regreasing will vary
widely depending on motor size, speed and environment.
The table below suggests relubrication intervals for
motors on normal, steady running, light duty indoor
loads in relatively clean atmosphere at 40°C (105°F)
ambient temperature or less. Fractional horsepower
motors follow a schedule similar to that shown under
frames 143T to 215T.
Motor Lubrication Intervals
TYPE OF
INSULA-
FRAME SIZE
ENCLOSURE
TION
143T–215T
254T–326T
364T–449T
Open-DP
B
2 yrs.
18 mos.
1 yr.
Enclosed-FC
B
Open-DP
F
18 mos.
1 yr.
9 mos.
Enclosed-NV
B
Enclosed-FC
F
Open-DP
H
1 yr.
9 mos.
6 mos.
Enclosed-Lint
Free-FC
B
Enclosed-NV
F
Enclosed-FC
H
Enclosed-Lint
9 mos.
6 mos.
3 mos.
Free-FC
F
NOTE: For motors over 1800 RPM, use
1
⁄
2
of tabled period. For heavy
duty, dusty locations, use
1
⁄
2
of tabled period. For severe-duty high vibra-
tion/shock, use
1
⁄
3
of tabled period.
VOLUME - REFERENCE TABLE
SHAFT DIAMETER
AMOUNT OF
(AT FACE OF BRACKET)
GREASE TO ADD
3
⁄
4
" to 1
1
⁄
4
"
1/8 cu. in. or 0.1 oz.
1
1
⁄
4
" to 1
7
⁄
8
"
1/4 cu. in. or 0.2 oz.
1
7
⁄
8
" to 2
3
⁄
8
"
3/4 cu. in. or 0.6 oz.
2
3
⁄
8
" to 3
3
⁄
8
"
2 cu. in. or 1.6 oz.
Motors with no provision for lubrication are equipped
with sealed bearings and require no maintenance.
Motors mounted in inaccessible locations are provided
with extended grease lines to facilitate lubrication if
provisions for lubrication are provided. The bearings are
equipped with relief fittings to prevent over-lubrication.
The grease lines are filled with lubricant at the factory.
Procedure for Relubrication
1. Stop motor.
2. Remove grease relief plugs in bearing housings.
3. Grease with hand gun until new grease appears at
relief hole.
4. Run motor for ten (10) minutes before replacing relief
plugs.
CAUTION: Do not over-lubricate. This is a major cause
of bearing and motor failure. Make sure dirt and con-
taminants are not introduced when adding grease.
Type of Grease
Lubricate with the following greases or their equivalent:
Amoco Rykon Premium #2
Chevron BRB-2 – Standard Oil or Calif.
SRI-2 – Standard Oil Company
Gadus S2 V100 2 - Shell Oil Company
Mobilith AW2
For motors lubricated with special greases, check lubri-
cation tag on motor.