Lubrication instructions for fan ball bearings, Storage of equipment, Fan bearings – Aerovent IM-100 User Manual
Page 3: Motors
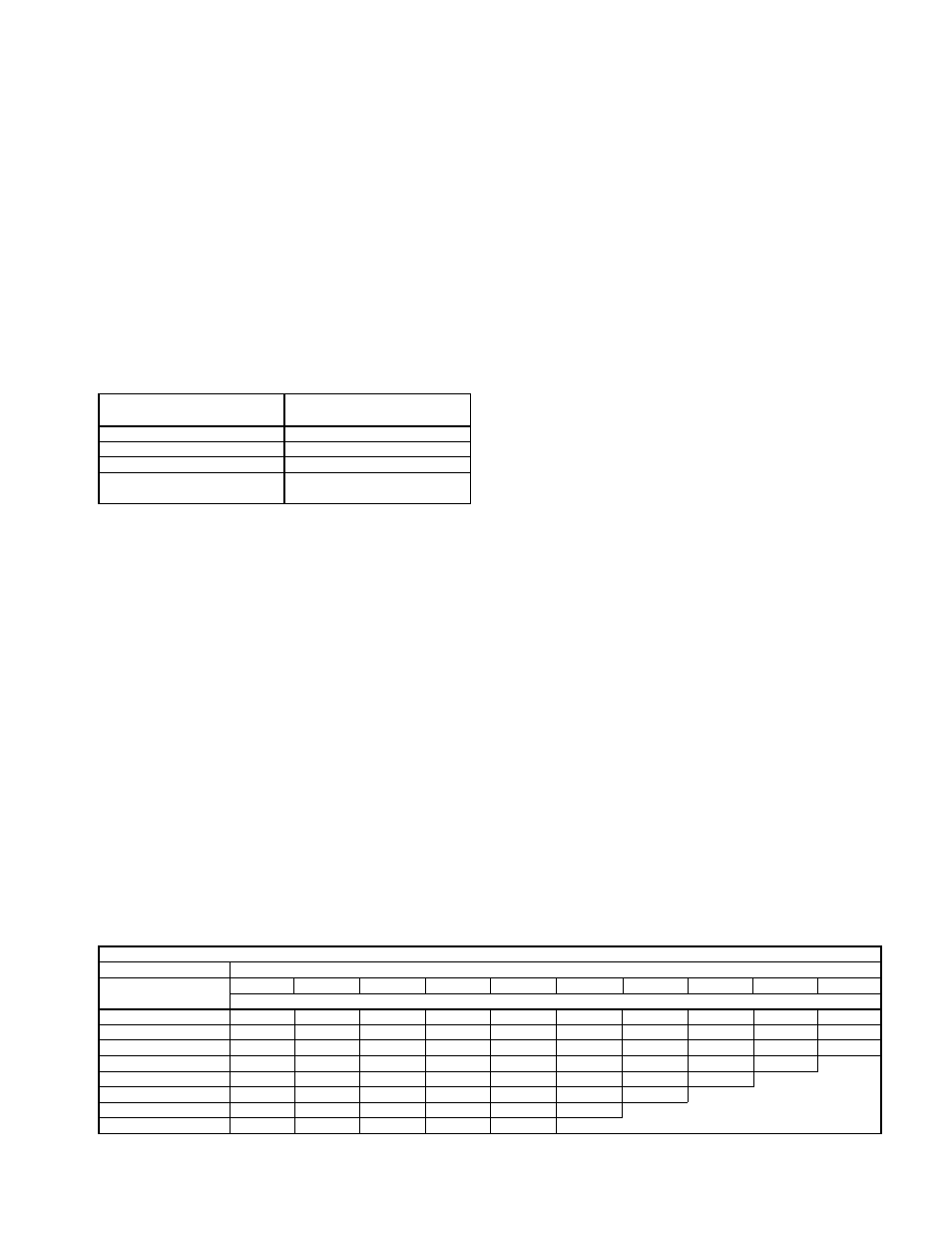
Aerovent IM-100
3
Lubrication Instructions for
Fan Ball Bearings
Bearings and grease lines on belt driven fans are lubri-
cated in assembly. When lubrication is required, add
grease slowly while the shaft is rotating until grease
comes rapidly out of the seal.
For extreme conditions, lubricate according to experi-
ence. For normal conditions, lubricate the bearings with
Mobilith AW2 or an equivalent.
Bearings and grease lines on axial fans that are
ordered for high moisture or above normal temperatures
have been lubricated with a special lubricant, Plastilube
#2. Lubricate at regular intervals with Plastilube #2 as
indicated in the special lubrication chart listed below.
Plastilube #2 is available from Sulflo, Inc. 1158 Erie
Avenue, North Tonowanda, New York 14120.
Storage of Equipment
Fan Bearings
Since bearings tend to “breathe” on equipment stored
in areas with other than a constant temperature, mois-
ture will condense internally. Therefore, it is necessary
to keep the bearings completely full of grease and
periodically rotated to make certain that all internal
parts are coated with grease. Even a full bearing will
eventually pick up moisture and, therefore, must be
periodically purged with new grease.
Grease should be purged from the bearings to
remove condensed moisture, and the fan wheel rotated
by hand every thirty (30) days. This practice should be
done more often if weather is severe or if there is a
wide variation in temperature.
CAUTION IN PURGING: The fan should be rotated
while greasing and high pressure pneumatic greasers
should be avoided. See “Lubrication Instructions for Fan
Ball Bearings.”
To rotate the fan, follow the procedure listed below:
The blade marked number 1 should be rotated to
top center. The blade number and date should be
recorded in a log book which is to be stored in a
protective pouch attached to the fan. During storage,
the fan propeller should be rotated by hand at least
ten (10) revolutions every thirty (30) days to circulate
the lubricant in the bearings in the motor or on the fan
shaft. After the tenth revolution, stop with a blade at
top center which is not the same one as is listed for
the previous date in the log book.
Fans which are V-belt driven should be prepared for
storage as follows:
Carefully remove the belts, coil them (without kinks)
in matched sets and place them in a heavy carton.
Mark the carton with fan identification and store the
carton in a dry, well-ventilated area. Belts must not be
left exposed to sunlight or subjected to storage ambient
conditions exceeding 85°F, 70% relative humidity. Belts
which show signs of deterioration should be replaced
prior to startup. Before reinstalling belts, review the sec-
tion on “Belt Tension.”
NOTE: Procedures for storage of Aerovent equipment
as outlined above are intended as a general guide only.
Storage conditions will vary depending on the loca-
tion. Common sense and practical experience should
determine to what extent the above procedures will be
followed.
Motors
Motors must be stored under cover in a clean, dry,
vibration-free location. Remove sufficient packaging
material to allow circulation of air around the motor.
Maintain the temperature of the windings a few degrees
above that of the surrounding air to protect against
condensation. If the motor is equipped with internal
heaters, the heaters should be energized throughout
the storage period to prevent this condensation. If
the motor does not have internal heaters, this can be
accomplished using any other safe, reliable method of
heating. Measure and record the ambient air tempera-
ture and winding temperature monthly.
In the event that the motor is not equipped with
internal heaters and space heating equipment is unavail-
able, wrap the motor as tightly as possible with heavy
duty polyethylene. Enclose bags of desiccant (such as
silicagel) with the motor to minimize moisture problems.
Check the desiccant regularly and replace it periodically
as dictated by climate requirements.
Lubrication Frequency for Horizontal Shaft Installations
(see Note for vertical shaft installations)
LUBRICATION FREQUENCY
OPERATING SPEED (RPM)
SHAFT SIZE
500
1000
1500
2000
2500
3000
3500
4000
4500
5000
(INCHES)
RELUBRICATION CYCLE (MONTHS)
1
⁄
2
– 1
6
6
6
6
6
6
4
4
2
2
1
1
⁄
16
– 1
7
⁄
16
6
6
6
6
6
6
4
4
2
1
1
1
⁄
2
– 1
3
⁄
4
6
6
6
4
4
2
2
2
1
1
1
7
⁄
8
– 2
3
⁄
16
6
6
4
4
2
2
1
1
1
2
1
⁄
4
–2
7
⁄
16
6
4
4
2
2
1
1
1
2
1
⁄
2
– 3
6
4
4
2
1
1
1
3
7
⁄
16
– 3
1
⁄
2
6
4
2
1
1
1
3
15
⁄
16
– 4
6
4
2
1
1
NOTES: Reduce this lubrication frequency schedule by half for vertical shaft installations.
Consult manufacturer for specific recommendations.
Special Lubrication Frequency For
High Temperature and High Moisture
AIRSTREAM
TEMPERATURE
HOURS
TO 250°F
4500
TO 350°F
1500
TO 500°F
1000
WET ATMOSPHERE AT
ROOM TEMPERATURE
1000 TO 1500