Fan bearing replacement procedure, Replacing fan belts, Belt tension procedure – Aerovent IM-100 User Manual
Page 4
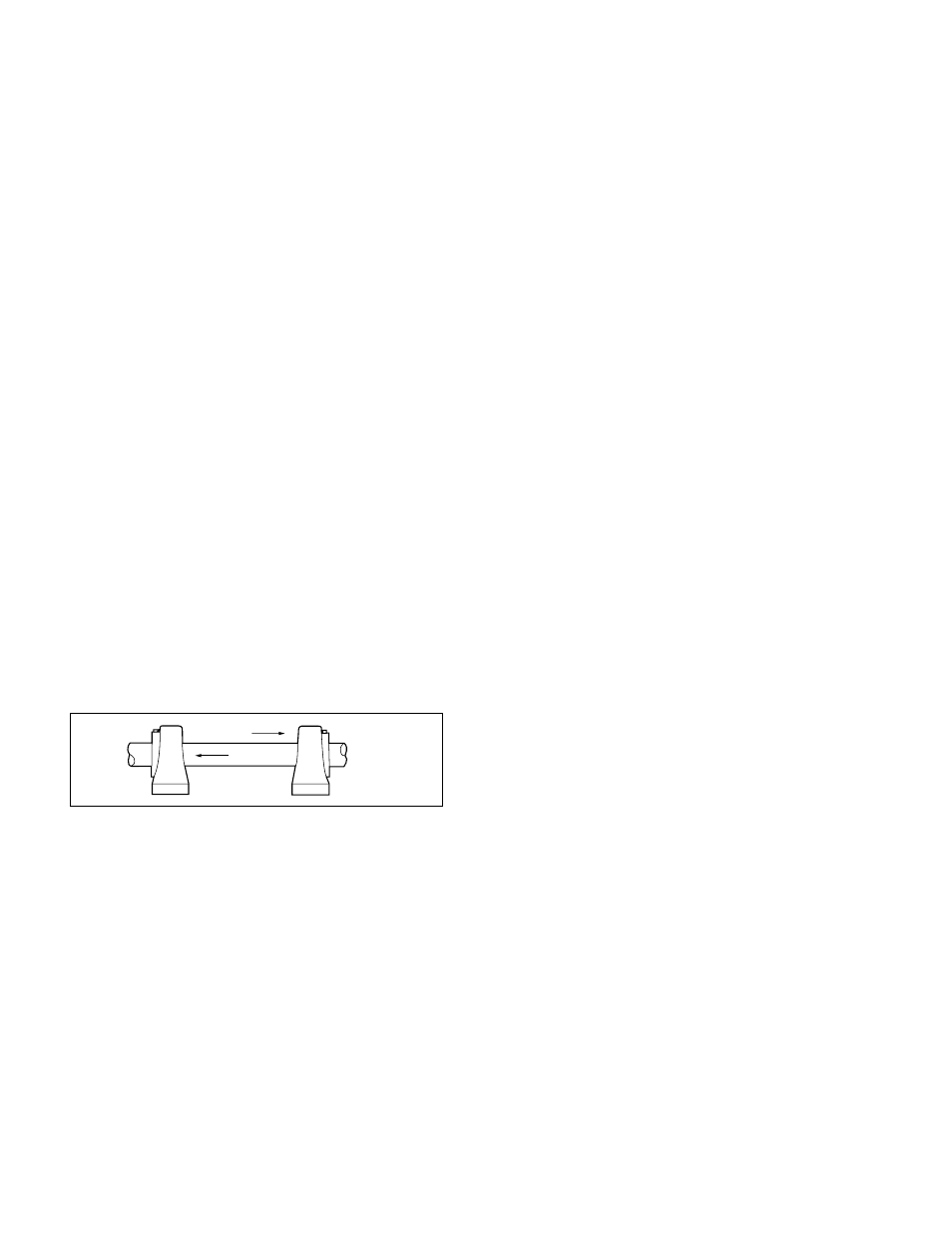
4
Aerovent IM-100
To prevent rusting of bearing parts, the rotor must
be rotated at regular intervals (30 days) to assure these
parts are well covered with oil or grease.
Prior to energizing the motor, it is to be inspected
and meggered by a motor manufacturer’s field service
engineer. The charges for this service to the customer
will be in accordance with the manufacturer’s published
service rates in effect at the time of the inspection.
In addition, it is strongly recommended that the
motor manufacturer be contacted for specific long-term
storage instructions.
Fan Bearing Replacement
Procedure
It is important to follow the assembly and alignment
procedure when making an installation of replacement
bearings. Inspect the shaft for wear at the bearing
mounting positions. Shaft diameter should not be under-
sized more than commercial ground and polished toler-
ances. Excessive undersizing will result in rapid wear.
1. Place new bearings loosely on the shaft. Locking
collars may be located on either end of the bearings
for ease of installation. The illustration shows one
locking collar on the drive end and one locking collar
on the fan end which is typical for a tubeaxial type
fan. A typical SWSI centrifugal fan would have both
collars mounted on the sheave side of the bearings.
Drop the mounting bolts in place, snug them and
adjust the position of the shaft with proper spacing
at either end.
2. Center both ends of the shaft in the housing of
tubeaxial fans using the propeller as a guide. On
centrifugal fans, the shaft is positioned 90° to the
scroll side with the wheel inlet centered in the scroll
inlet. Use the clearance in the mounting holes for
horizontal adjustment and shims, if necessary, for
vertical adjustment.
3. Tighten the bearings to the base plate and check
the position of the shaft again. Before tightening the
locking collars, be sure the shaft and bearings are in
proper alignment. The shaft should slide freely end
to end.
4. Tighten the eccentric cam locking collar of the bear-
ing at the propeller/wheel end. (The locking collar
design provides a positive lock of the wide inner
ring bearing to the shaft. To tighten, turn the locking
collar in the direction of shaft rotation to the lock
position, then tighten the collar set screw.) Repeat
this procedure for the sheave end locking collar on
DWDI and open wheel centrifugals. For other fan
types, proceed to Step 5.
5. Axial flow propellers and single inlet centrifugal
wheels with back plates exert an air thrust toward
the fan inlet. (See Figure 1.) To help balance the
bearing loading, we allow the fan end bearing (belt
driven units) to carry the majority of this thrust load-
ing while the sheave end bearing carries most of
the radial load. (Direct coupled units would be just
the opposite.) To accomplish this, grasp the sheave
end of the shaft and pull or push on it toward the
fan inlet. At the same time, tap the locking collar of
the sheave end bearing (fan end on direct coupled
units) in the opposite direction with a soft mallet.
6. The final step is to tighten the sheave end bearing
eccentric cam locking collar while maintaining con-
stant pressure on the shaft toward the fan inlet.
For special heavy duty bearings, a spring locking
collar is used. The two knurled cup-point set screws
extend through the inner ring of the bearing and lock
firmly onto the shaft. Tighten the propeller end collar
first, then take hold of the sheave end of the shaft, pull
and then tighten the locking collar. The locking collar is
tightened by using the two set screws mentioned above.
Replacing Fan Belts
Worn belts may be easily replaced without removing the
fan from the system.
1. Loosen the motor hold-down bolts and move the
motor toward the fan. (This is done by turning a
jackscrew which is a part of the motor base on mod-
els having larger motors.) The belt may be slipped
off the motor sheave and then easily removed from
the sheave on the propeller shaft.
2. Check the numbers on the belt and make the
replacement with a belt having the same length and
section.
3. Adjust the motor outward to tighten the belt (see
instructions on belt tension, below) and tighten the
motor hold-down bolts. Be sure that the motor is
not cocked at an angle and that the end face of
the motor sheave is parallel to the end face of the
driven sheave.
Belt Tension Procedure
Belt tension is very important to the proper operation of
a fan and to the service life of a V-belt drive. A new
fan will be received with its belts properly adjusted;
however, all V-belts stretch in the first few hours of
operation. It is necessary to readjust the belt tension
after eight hours of running. After 100 hours the belts
should again be adjusted. Thereafter, periodic inspection
is recommended so belts may be adjusted or replaced
when necessary.
1. To adjust the belts, loosen the motor hold-down
bolts. Tighten the belt using the motor base adjusting
screw until the belt appears to be taut. You should
be able to deflect the belt slightly by squeezing the
two sides between thumb and forefinger and the belt
should snap back into position when released.
2. Retighten the motor hold-down bolts and start the
fan. If the belt screeches on startup it is too loose
and should be tightened further.
3. Allow the fan to run for a while, stop the fan, and
check the temperature of the sheave with your hand.
If the sheave is too hot to touch, the belt is probably
too tight.
V-belt drives on Aerovent fans are purposely sized to
handle considerably more load than would be necessary
for normal drive design. This is done to prolong the
life of the drive and provide for minimum maintenance.
Belts should be replaced when they have obviously
become worn, even though they are still operating.
A badly worn belt will also cause undue wear of the
Figure 1. Two Bearing Drive
Airflow
Thrust