Stuffing box lubrication – Goulds Pumps 3408 - IOM User Manual
Page 22
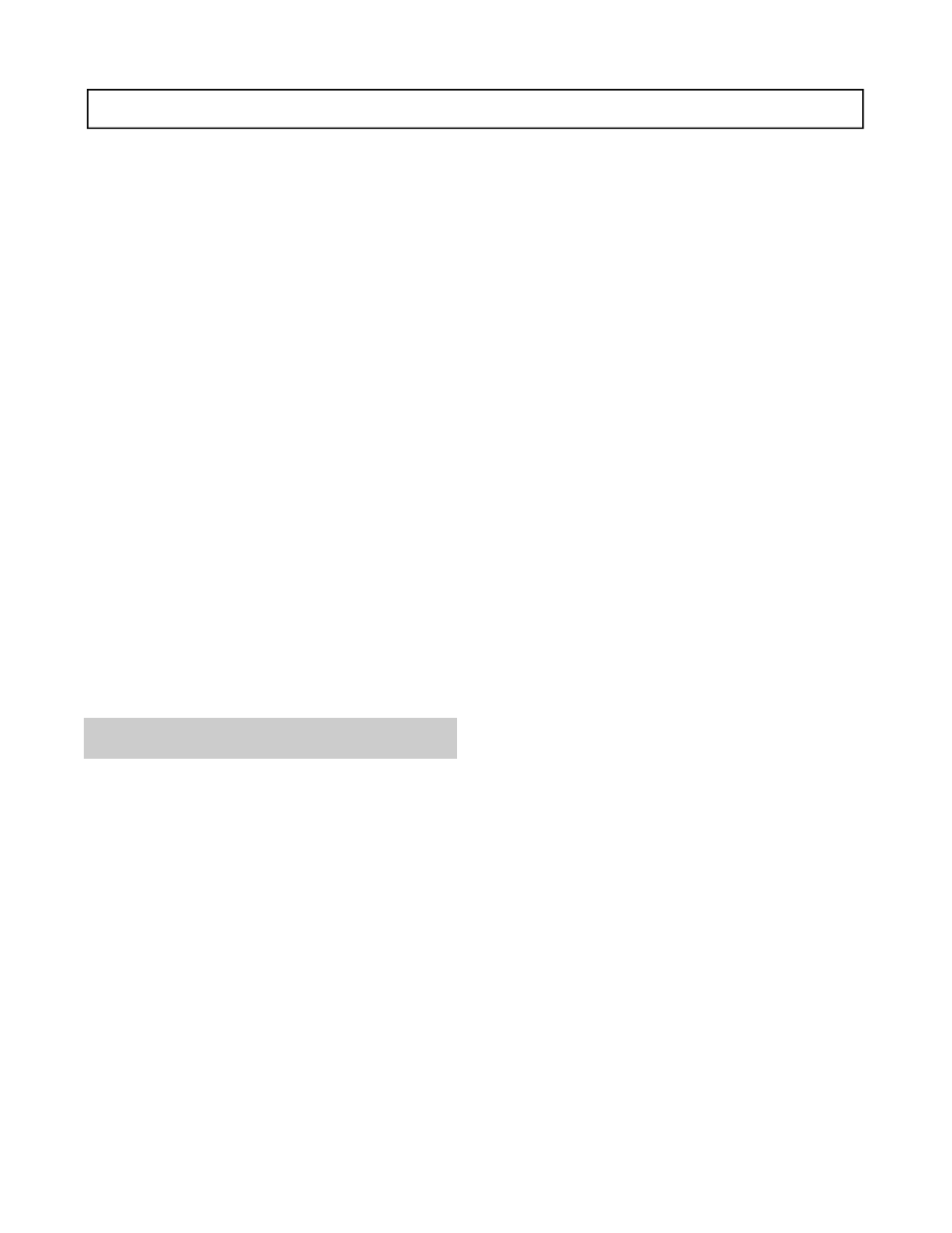
20
3408 IOM 03/99
STUFFING BOX LUBRICATION
Contaminants in the pumped liquid must not enter the
stuffing box. These contaminants may cause severe
abrasion or corrosion of the shaft, or shaft sleeve, and
rapid packing or mechanical seal deterioration; they
can even plug the stuffing box flushing and lubrication
system. The stuffing box must be supplied at all times
with a source of clean, clear liquid to flush and
lubricate the packing or seal. The most important
consideration is to establish the optimum flushing
pressure that will keep contaminants from the stuffing
box cavity. If this pressure is too low, fluid being
pumped may enter the stuffing box. If the pressure is
too high, excessive packing or seal wear may result;
and extreme heat may develop in the shaft causing
higher bearing temperatures. The most desirable
condition, therefore, is to use a seal water pressure
15-20 psig above the maximum stuffing box pressure.
If the pump system pressure conditions vary, packing
adjustment becomes difficult. Consideration should be
given to using a mechanical seal. (See Mechanical
Seals.)
Packing
Standard pumps are normally packed before ship-
ment. If the pump is installed within 60 days after
shipment, the packing will be in good condition with a
sufficient supply of lubrication. If the pump is stored
for a longer period, it may be necessary to repack the
stuffing box. In all cases, however, inspect the
packing before the pump is started.
NOTE: Packing adjustment is covered in the
MAINTENANCE SECTION of this manual.
On some applications, it is possible to use internal
liquid lubrication (pumped liquid) to lubricate packing.
Only when all of the conditions prevail, can this be
done:
1.
Liquid is clean, free from sediment and chemical
precipitation and is compatible with seal
materials.
2.
Temperature is above 32° F and below 160° F.
3.
Suction pressure is below 75 psig.
4.
Lubrication (pumped liquid) has lubricating
qualities.
5.
Liquid is non-toxic and non-volatile.
When the liquid being pumped contains solids or is
otherwise not compatible with packing materials, an
outside supply of seal liquid should be furnished. In
general, external-injection liquid (from an outside
source) is required when any of the above conditions
cannot be met.
The standard stuffing box consists of rings of packing
(see assembly section for number of rings), a seal
cage (optional), and a gland. A shaft sleeve which
extends through the box and under the gland is
provided to protect the shaft.
A tapped hole is supplied in the stuffing box directly
over the seal cage to introduce a clean, clear sealing
medium. The stuffing box must, at all times, be
supplied with sealing liquid at a high enough pressure
to keep the box free from foreign matter, which would
quickly destroy the packing and score the shaft
sleeve.
Only a sufficient volume of sealing liquid to create a
definite direction of flow from the stuffing box inward
to the pump casing is required, but the pressure is
important. Apply seal water at a rate of approximately
.25 GPM at a pressure approximately 15 to 20 psig
above the suction pressure. (Approximately one (1)
drop per second.)
One recommended method to minimize error in
regulating flushing water is a “Controlled Pressure
System.” (Fig. 14) Most important is the pressure
reducing valve adjusted to a value slightly exceeding
the maximum stuffing box operating pressure
(assuming it is reasonably constant). A flow indicating
device will serve to indicate a failing of the bottom
packing rings allowing leakage in the pump.
External sealing liquid should be adjusted to the point
where the packing runs only slightly warm, with a very
slow drip from the stuffing box. Excess pressure from
an external source can be very destructive to packing.
More pressure is required, however, for abrasive
slurries than for clear liquids. Examination of the
leakage will indicate whether to increase or decrease
external pressure. If slurry is present in the leakage,
increase the pressure until only clear liquid drips from
the box. If the drippage is corrosive or harmful to
personnel, it should be collected and piped away.
A common error is to open the external piping valve
wide and then control the drippage by tightening the
packing gland. Actually, a combination of both
adjustments is essential to arrive at the optimum
condition. The life of packing and sleeve depends on
this careful control more than any other factor.