Lubricant, Bearings, Services – COOK Propeller Inline User Manual
Page 5: Replacement, Lubricants, Motor bearings, Fan bearings, Motor services, Changing shaft speed, Pulley and belt replacement
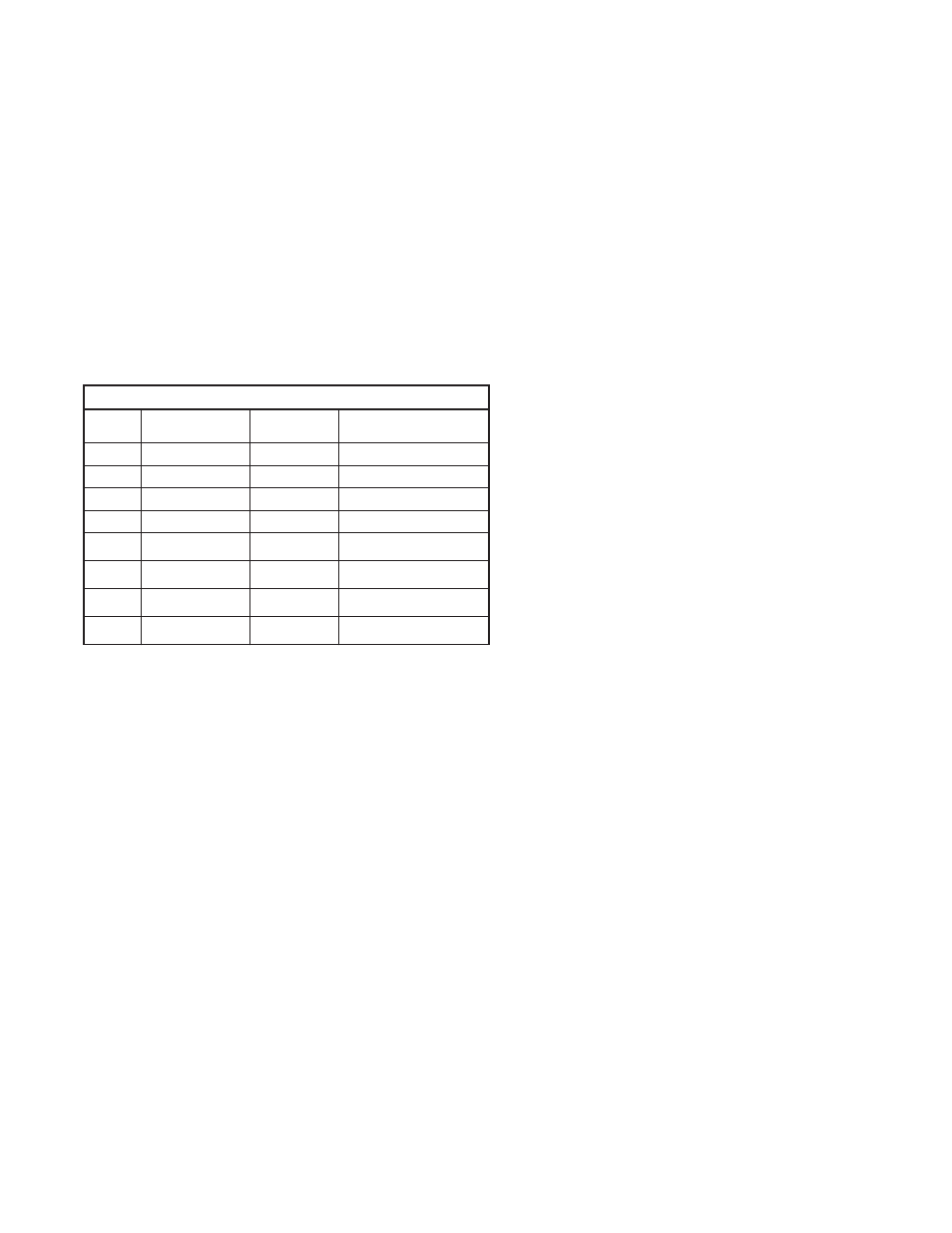
5
Lubricants
Loren Cook Company uses petroleum lubricant in a lith-
ium base conforming to NLGI grade 2 consistency. Other
grades of grease should not be used unless the bearings
and lines have been flushed clean. If another grade of
grease is used, it should be lithium-based.
A NLGI grade 2 grease is a light viscosity, low-torque,
rust-inhibiting lubricant that is water resistant. Its tempera-
ture range is from -30
F to +200F and capable of intermit-
tent highs of +250
F.
Motor Bearings
Motor bearings are pre-lubricated and sealed. Under nor-
mal conditions they will not require further maintenance for
a period of ten years. However, it is advisable to have your
maintenance department remove and disassemble the
motor, and lubricate the bearings after three years of opera-
tion in excessive heat and or in a contaminated airstream
consisting of airborne abrasives.
Fan Bearings
Fan bearings are lubricated through a grease connector
and should be lubricated by the schedule, Conditions Chart,
shown above.
For best results, lubricate the bearing while the fan is rotat-
ing. Slowly pump grease into the bearing until a slight bead
forms around the bearing seals. Excessive grease can burst
seals thus reduce bearing life.
In the event the bearing cannot be seen, use no more than
three injections with a hand-operated grease gun.
Motor Services
Should the motor prove defective within a one-year
period, contact your local Loren Cook representative or your
nearest authorized electric motor service representative.
Changing Shaft Speed
All belt driven Tube Axial fans with motors up to and
including 5HP are equipped with variable pitch pulleys. To
change the fan speed, perform the following:
a. Loosen setscrew on driver (motor) pulley and remove
key, if equipped.
b. Turn the pulley rim to open or close the groove facing. If
the pulley has multiple grooves, all must be adjusted to
the same width.
c. After adjustment, inspect for proper belt tension.
Conditions Chart
RPM
Temperature
Fan
Status
Greasing
Interval
100
Up to 120°F
Clean
6 to 12 months
500
Up to 150°F
Clean
2 to 6 months
1000
Up to 210°F
Clean
2 weeks to 2 months
1500 Over
210°F
Clean
Weekly
Any
Speed
Up to 150°F
Dirty
1 week to 1 month
Any
Speed
Over 150°F
Dirty
Daily to 2 weeks
Any
Speed
Any Temperature
Very Dirty
Daily to 2 weeks
Any
Speed
Any Temperature
Extreme
Conditions
Daily to 2 weeks
Speed Reduction
Open the pulley in order that the belt rides deeper in the
groove (smaller pitch diameter).
Speed Increase
Close the pulley in order that the belt rides higher in the
groove (larger pitch diameter). Ensure that the RPM limits
of the fan and the horsepower limits of the motor are main-
tained.
Pulley and Belt Replacement
a. Clean the motor and fan shafts.
b. Loosen the motor plate mounting bolts to relieve the
belt tension. Remove the belt.
c. Loosen the pulley setscrews and remove the pulleys
from the shaft.
If excessive force is required to remove the pul-
leys, a three-jaw puller can be used. This tool,
however, can easily warp a pulley. If the puller is
used, inspect the trueness of the pulley after it is
removed from the shaft. The pulley will need
replacement if it is more than 0.020 inch out of
true.
d. Clean the bores of the pulleys and place a light coat of
oil on the bores.
e. Remove grease, rust and burrs from the shaft.
f. Place fan pulley on the fan shaft and the motor pulley
on the motor shaft. Damage to the pulleys can occur
when excessive force is used in placing the pulleys on
their respective shafts.
g. After the pulleys have been correctly placed back onto
their shafts, tighten the pulley setscrews.
h. Install the belts on the pulleys. Align and adjust the
belts to the proper tension as described in Belt and Pul-
ley Installation, page 1.
Bearing Replacement
The fan bearings are pillow block ball bearings.
a. Loosen the motor plate mounting bolts and remove the
drive belts.
b. Gain access to the interior of the fan. Remove duct
work and/or guards as necessary.
c. Remove the propeller from the shaft.
d. Remove the bearing cover from the bearing plate.
e. Remove the four bearing hold-down bolts and then
remove the shaft, bearings, and driven sheave from
the unit as an assembly.
f. Mark the location of the bearings and sheave on the
shaft. This will aid the reassembly.
g. Remove the anti-corrosion coating from the shaft with a
suitable degreaser and then remove the pulley from the
shaft.
h. Remove the bearings from the shaft using a bearing
puller.
i. Clean the shaft and bearing bores thoroughly.
j. Place the bearings into position making sure they are
not on a worn section of the shaft. Tapping the inner
ring face with a soft driver may be required.
NOTICE! Do not hammer on the housing. This my
cause damage to the bearings.