Fan installation, Operation, Start up – COOK Lo-Pro User Manual
Page 4: Inspection, Maintenance, Fan bearings, Motor bearings
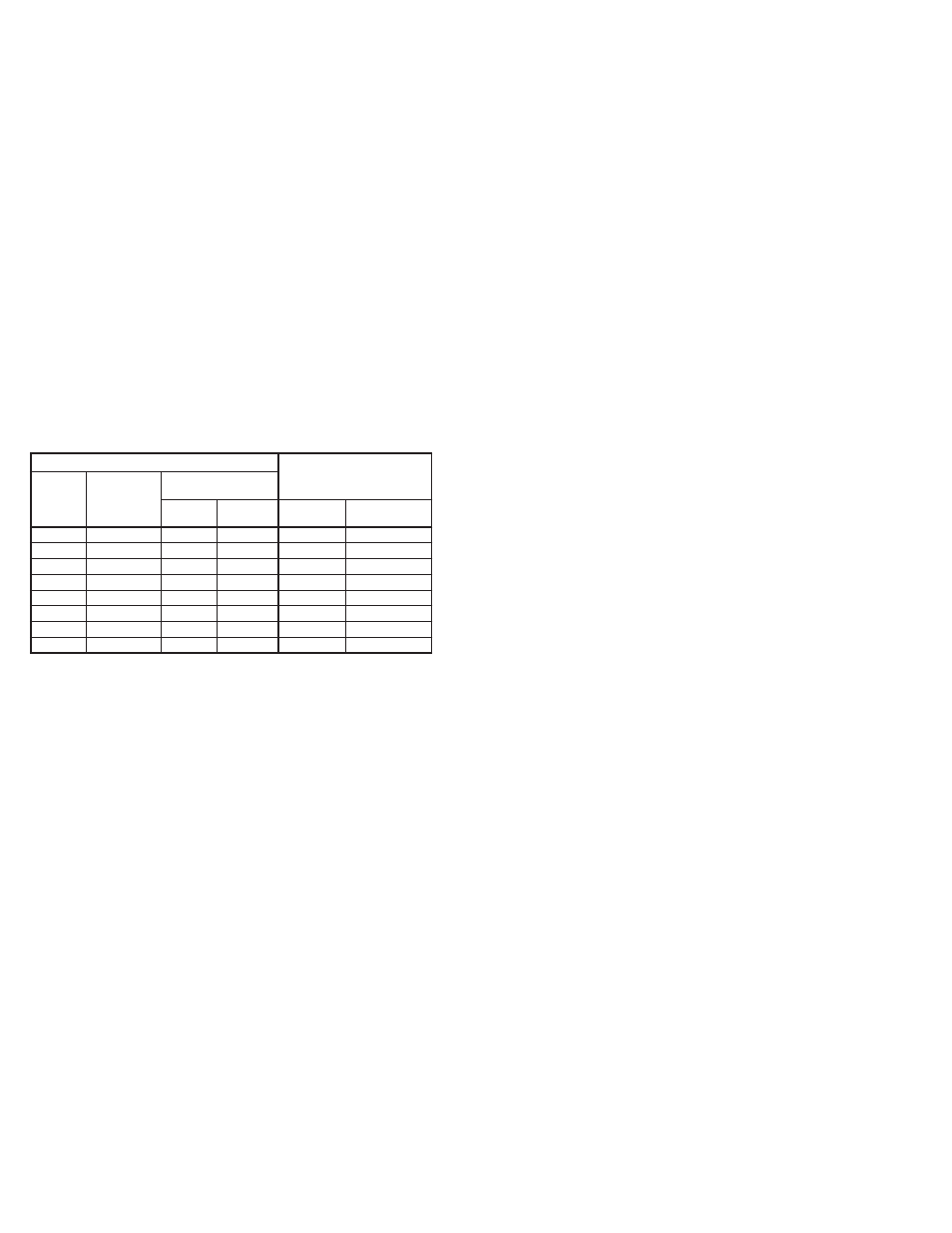
4
wrong direction, check the control switch. If is possible
to interchange two leads at this location so that the fan
is operating in the correct direction.
Fan Installation
Place fan over roof opening. Secure the fan with lag
screws, anchor bolts, or other suitable fasteners.
Operation
Pre-Start Checks
a. Lock out all the primary and secondary power sources.
b. Inspect fasteners and setscrews, particularly those
used for mounting the fan, and tighten if necessary.
c. Inspect belt tension and pulley alignment. (Remember,
if belt tension is correct, a loud squeal occurs as the
fan increases to full power.)
d. Inspect motor wiring.
e. Ensure the belt touches only the pulleys.
f. Ensure fan and ductwork are clean and free of debris.
g. Test the fan to ensure the rotation of the wheel is the
same as indicated by the rotation label.
h. Close and secure all access doors.
i. Restore power to unit.
Start Up
Turn the fan on. In variable speed units, set the fan to its
lowest speed. Inspect for the following:
• Direction of rotation
• Excessive vibration
• Unusual noise
• Bearing noise
• Improper belt alignment or tension (listen for a continu-
ous squealing noise)
• Improper motor amperage or voltage
NOTICE! If a problem is discovered, immediately shut
off the fan. Lock out all electrical power and check for
the cause of the trouble. Refer to Troubleshooting,
page 6.
Inspection
Inspection of the fan should be conducted at the first 30
minute, 8 hour and 24 hour intervals of satisfactory opera-
tion. During the inspections, stop the fan and inspect as per
the chart below.
30 Minute Interval
Inspect bolts, setscrews, and motor mounting bolts.
Adjust and tighten as necessary.
8 Hour Interval
Inspect belt alignment and tension. Adjust and tighten as
necessary.
24 Hour Interval
Inspect belt tension. Adjust and tighten as necessary.
Recommended Torque for Setscrews/Bolts (IN/LB.)
Setscrews
Hold Down Bolts
Size
Key Hex
Across
Flats
Recommended
Torque
Min.
Max.
Size
Wrench
Torque
No.10
3/32”
28
33
3/8”-16
240
1/4”
1/8”
66
80
1/2”-13
600
5/16”
5/32”
126
156
5/8”-11
1200
3/8”
3/16”
228
275
3/4”-10
2100
7/16”
7/32”
348
384
7/8”-9
2040
1/2”
1/4”
504
600
1”-8
3000
5/8”
5/16”
1104
1200
1-1/8”-7
4200
3/4”
3/8”
1440
1800
1-1/4”-7
6000
Maintenance
Establish a schedule for inspecting all parts of the
fan.The frequency of inspection depends on the operating
conditions and location of the fan.
Inspect fans exhausting corrosive or contaminated air
within the first month of operation. Fans exhausting con-
taminated air (airborne abrasives) should be inspected
every three months. Clean the wheel and air inlets if mate-
rial build-up is excessive. Excessive build-up can cause
imbalance and failure of the wheel.
Regular inspections are recommended for fans exhaust-
ing non-contaminated air.
Regular inspections of the Grease Terminator 2 are rec-
ommended. Depending on the amount of grease dis-
charged through the fan, the Terminator 2 should be
changed every 30 to 45 days to ensure proper operation.
Any buildup of grease is easily seen during a visual inspec-
tion of the clear canister. However, if the Terminator 2
becomes saturated, grease will no longer be absorbed.
It is recommended the following inspections be con-
ducted twice per year.
• Inspect bolts and setscrews for tightness. Tighten as
necessary.
• Inspect belt wear and alignment. Replace worn belts
with new belts and adjust alignment as needed. See
Belt and Pulley Installation, page 2.
• Bearings should be inspected as recommended in the
Conditions Chart, page 5.
• Inspect for cleanliness. Clean exterior surfaces only.
Removing dust and grease on motor housing assures
proper motor cooling.
Fan Bearings
The fan bearings are provided prelubricated. Any spe-
cialized lubrication instructions on fan labels supercedes
information provided herein. Bearing grease is a petroleum
lubricant in a lithium base conforming to a NLGI #2 consis-
tency. If user desires to utilize another type of lubricant,
they take responsibility for flushing bearings and lines, and
maintaining a lubricant that is compatible with the installa-
tion.
A NLGI #2 grease is a light viscosity, low-torque, rust-
inhibiting lubricant that is water resistant. Its temperature
range is from -30°F to 200°F and capable of intermittent
highs of 250°F.
Bearings should be relubricated in accordance with the
condition chart below.
For best results, lubricate the bearing while the fan is in
operation. Pump grease in slowly until a slight bead forms
around the bearing seals. Excessive grease can damage
seal and reduce life through excess contamination and/or
loss of lubricant.
In the event that the bearing cannot be seen, use no
more than three injections with a hand operated grease
gun.
Motor Bearings
Motors are provided with prelubricated bearings. Any
lubrication instructions shown on the motor nameplate
supersede instructions below.