Maintenance, Filters, Fan bearings – COOK Duct Blower User Manual
Page 4: Motor bearings, Motor services
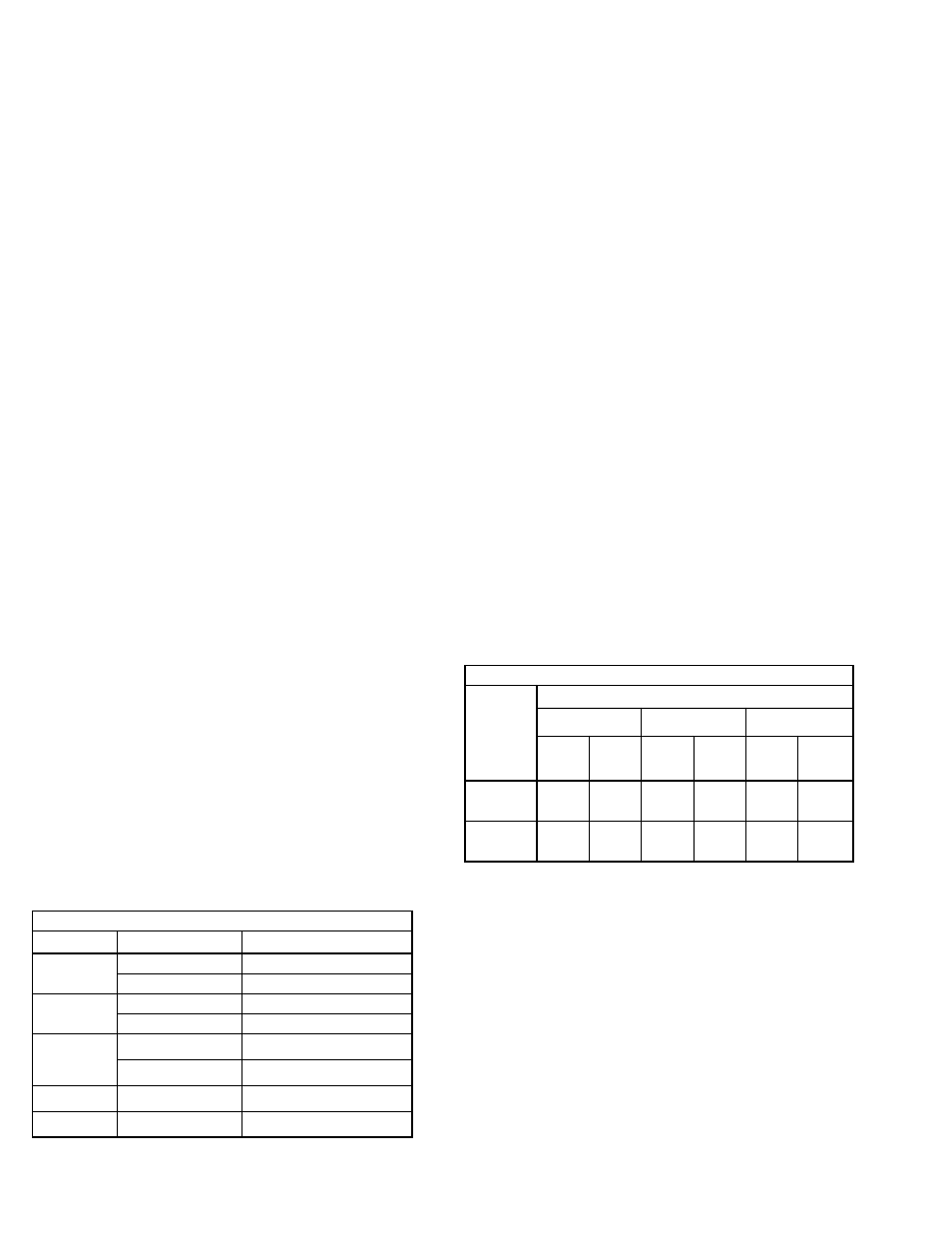
4
Filters
(if included)
Filters should be inspected within the first two weeks of
operation. If there is no excessive build-up, monthly servic-
ing should be adequate.
To clean reusable aluminum filters, back flush with soap and
water. When clean, shake off excess water and allow the fil-
ter to air-dry before reinstalling it.
Maintenance
Establish a schedule for inspecting all parts of the fan.The
frequency of inspection depends on the operating condi-
tions and location of the fan.
Inspect fans exhausting corrosive or contaminated air
within the first month of operation. Fans exhausting contam-
inated air (airborne abrasives) should be inspected every
three months.
Regular inspections are recommended for fans exhaust-
ing non-contaminated air.
It is recommended the following inspections be conducted
twice per year.
• Inspect bolts and setscrews for tightness. Tighten as
necessary.
• Inspect belt wear and alignment. Replace worn belts
with new belts and adjust alignment as needed. See Belt
and Pulley Installation, page 2.
• Bearings should be inspected as recommended in the
Conditions Chart.
• Inspect for cleanliness. Clean exterior surfaces only.
Removing dust and grease on motor housing assures
proper motor cooling.
Fan Bearings
The fan bearings are provided prelubricated. Any special-
ized lubrication instructions on fan labels supercedes infor-
mation provided herein. Bearing grease is a petroleum
lubricant in a lithium base conforming to a NLGI #2 consis-
tency. If user desires to utilize another type of lubricant, they
take responsibility for flushing bearings and lines, and main-
taining a lubricant that is compatible with the installation.
A NLGI #2 grease is a light viscosity, low-torque, rust-
inhibiting lubricant that is water resistant. Its temperature
range is from -30°F to 200°F and capable of intermittent
highs of 250°F.
Bearings should be relubricated in accordance with the
condition chart below.
For moist or otherwise contaminated installations; divide the interval by a
factor of 3. For vertical shaft installations divide the interval by a factor of 2.
Conditions Chart
RPM
Temp °F
Greasing Interval
Up to 1000
-30 to 120
6 months
120 to 200
2 months
1000 to 3000
-30 to 120
3 months
120 to 200
1 month
Over 3000
-30 to 120
1 month
120 to 200
2 weeks
Any Speed
< -30
Consult Factory
Any Speed
> 200
1 week
For best results, lubricate the bearing while the fan is in
operation. Pump grease in slowly until a slight bead forms
around the bearing seals. Excessive grease can damage
seal and reduce life through excess contamination and/or
loss of lubricant.
In the event that the bearing cannot be seen, use no
more than three injections with a hand operated grease
gun.
Motor Bearings
Motors are provided with prelubricated bearings. Any
lubrication instructions shown on the motor nameplate
supersede instructions below.
Direct Drive 1050/1075,1200,1300 &1500 rpm units use
a prelubricated sleeve bearing that has a oil saturated wick-
ing material surrounding it. The initial factory lubrication is
adequate for up to 10 years of operation under normal con-
ditions. However, it is advisable to add lubricant after 3
years. Use only LIGHT grade mineral oil or SAE 10W oil up
to 30 drops. If the unit has been stored for a year or more it
is advisable to lubricate as directed above. For VCR direct
drive units and other units in severe conditions, lubrication
intervals should be reduced to half.
Motors without sleeve bearings (as described above) will
have grease lubricated ball or roller bearings. Motor bear-
ings without provisions for relubrication will operate up to
10 years under normal conditions with no maintenance. In
severe applications, high temperatures or excessive con-
taminates, it is advisable to have the maintenance depart-
ment disassemble and lubricate the bearings after 3 years
of operation to prevent interruption of service.
For motors with provisions for relubrication, follow inter-
vals of the table below.
Motors are provided with a polyurea mineral oil NGLI #2
grease. All additions to the motor bearings are to be with a
compatable grease such as Exxon Mobil Polyrex EM and
Chevron SRI.
The above intervals should be reduced to half for vertical
shaft installations.
Motor Services
Should the motor prove defective within a one-year
period, contact your local Loren Cook representative or
your nearest authorized electric motor service representa-
tive.
Relubrication Intervals
Service
Conditions
NEMA Frame Size
Up to and
including 184T
213T-365T
404T and larger
1800 RPM
and less
Over 1800
RPM
1800 RPM
and less
Over 1800
RPM
1800 RPM
and less
Over 1800
RPM
Standard
3 yrs. 6 months 2 yrs. 6 months
1 yr.
3 months
Severe
1 yr.
3 months
1 yr.
3 months6 months 1 months