Trouble shooting – Hellenbrand H-125 Series User Manual
Page 19
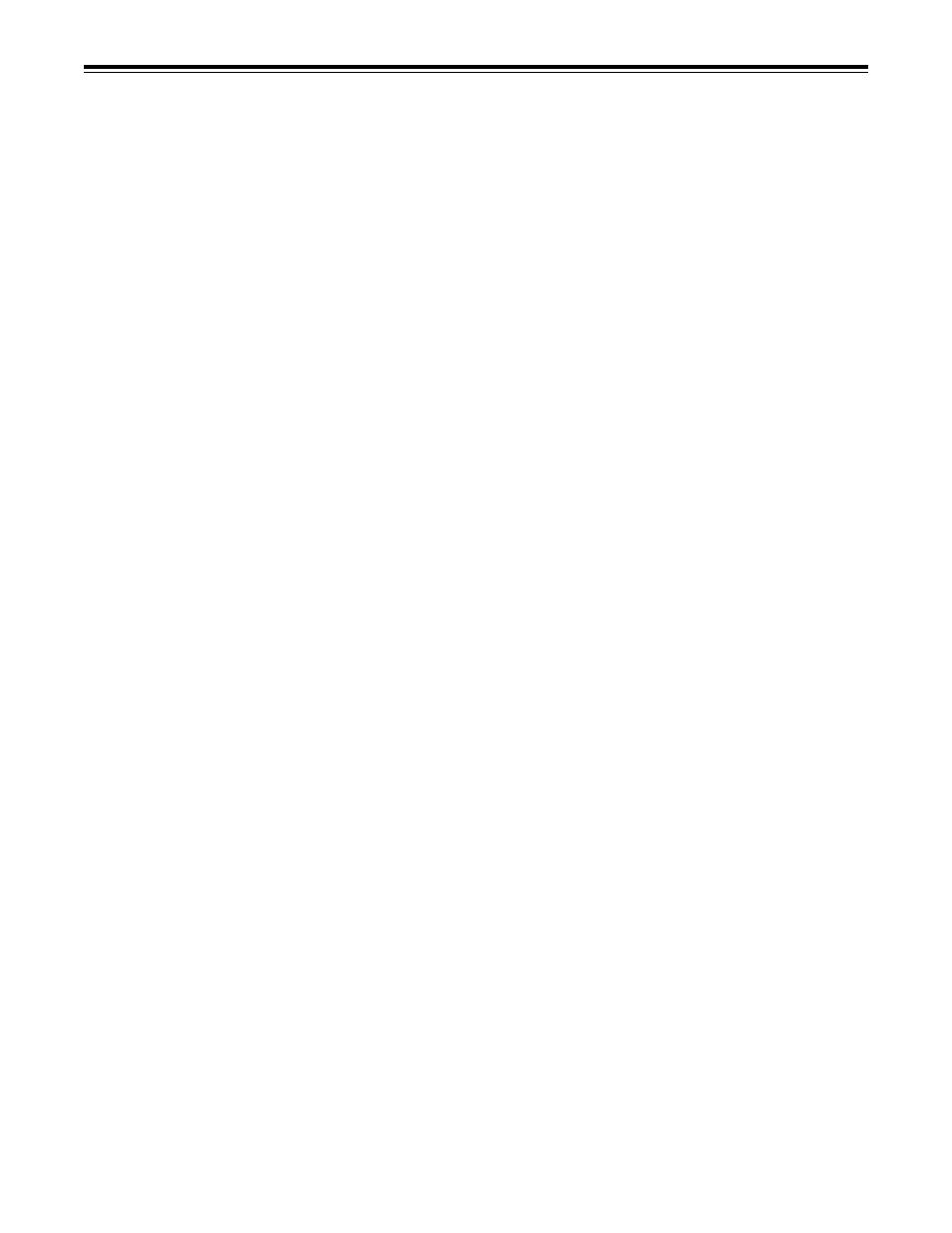
19
TrOuble shOOTinG
PROBLEM
CAUSE
CORRECTION
1. ERROR followed by code number
Error Code 101 - Unable to recognize
A1. Not reading piston position, valve has
A1. Resynchronize software with piston position, Press
start of regeneration
been recently serviced
NEXT & REGEN for 3 seconds or until display is blank
A2. Incorrect Assembly
A2. Disassemble drive bracket, verify wires are in guides
& reassemble. Verify motor is plugged into PC board
Error Code 102 - Unexpected stall
B. Mechanical Binding
B. Check piston and spacer stack assembly
for foreign matter
Error Code 103 - Motor ran too long,
C. High drive forces on piston
C. Loosen drive cap gear 1/4 turn or replace
timed out trying to reach next cycle
Address high drive forces.
position
Error Code 104 - Motor ran too long,
D1. Control valve piston not in home position
D1. Press NEXT and REGEN for 3 seconds
timed out trying to reach home position
or until display is blank.
D2. Motor not inserted fully to engage pinion,
D2. Check motor and wiring. Replace motor if
motor wires broken or disconnected,
necessary
motor failure
D3. Drive gear label dirty or damaged,
D3. Replace or clean drive gear
If other Error Codes display
missing or broken gear
contact the factory
D4. Drive bracket incorrectly aligned to
D4. Reseat drive bracket
back plate
D5. PC board is damaged or defective
D5. Replace PC board
D6. PC board incorrectly aligned to
D6. Ensure PC board is correctly snapped on to
MAV Error Codes:
drive bracket
drive bracket
Error Code 106
E. Incorrect programming. If programmed
E. Verify MAV drive cable and/or interconnect cable is
for any MAV use, MAV must be connected
connected to PC. If no auxilliary valve required,
to PC board prior to powering up.
program auxilliary control valve as off.
Error Code 107
F. MAV Stalled
F. Check MAV piston/stack for foreign matter, incorrect
assembly, motor not fully inserted or damaged gears
2. Control valve stalled in regeneration
A. Motor not operating
A. Replace Motor
B. No electric power at outlet
B. Repair outlet or use working outlet
C. Defective transformer
C. Replace transformer
D. Defective PC board
D. Replace PC board
E. Broken drive gear or drive cap assembly
E. Replace drive gear or drive cap assembly
F. Broken piston retainer
F. Replace drive cap assembly
G. Broken main or regenerant piston
G. Replace main or regenerant piston
3. Control valve does not regenerate
A. Transformer unplugged
A. Connect transformer
automatically when REGEN button
B. No electric power at outlet
B. Repair outlet or use working outlet
is depressed and held
C. Broken drive gear or drive cap assembly
C. Replace drive gear or drive cap assembly
D. Defective PC board
D. Replace PC board
4. Control valve does not regenerate
A. Bypass valve in bypass position
A. Put control valve in service position
automatically but does when
B. Meter connection disconnected
B. Connect meter to PC board
REGEN button is depressed
C. Restricted/stalled meter turbine
C. Remove meter and check for rotation
or foreign matter
D. Defective meter
D. Replace meter
E. Defective PC board
E. Replace PC board
F. Set-up error
F. Check control valve set-up procedure
5. Time of day flashes on and off
A. Battery back-up maintains time-of-day up
A. Reset time of day and replace battery on PC Board
to 2 years in event of power outage and
(Lithium coin type battery 2032)
battery is not depleted. Time of day flashes
when battery is depleted.
B. Prior to 2/2007, PC board did not have
B. Reset time of day.
battery back-up - capacitor held time of day
up to 2 hours. Power outage > 2 hours.
6. Softener delivers hard water.
A. Bypass valve is open or faulty.
A. Close bypass valve or replace.
B. No salt or low salt level in brine tank.
B. Add salt to brine tank and maintain salt level
above water level.
C. Softener fails to draw brine.
C. See problem #11.
D. Excessive water usage.
D. Check gallon capacity settings.
E. Insufficient brine level in brine tank.
E. Check brine refill setting and refill flow restrictor for
blockage.
F. Resin level inadequate.
F. See problem #8, page 21.
G. Meter faulty.
G. Test meter and clean or replace meter.
H. Raw water hardness fluctuation.
H. Test raw water hardness and adjust settings to
highest known hardness.
7. Unit uses too much salt.
A. Improper brine refill setting.
A. Check brine refill setting for proper salt dosage
B. Improper settings.
B. Check water hardness and reevaluate capacity setting
specification