ROTHENBERGER ROWELD ROFUSE Plus V2.0 User Manual
Page 18
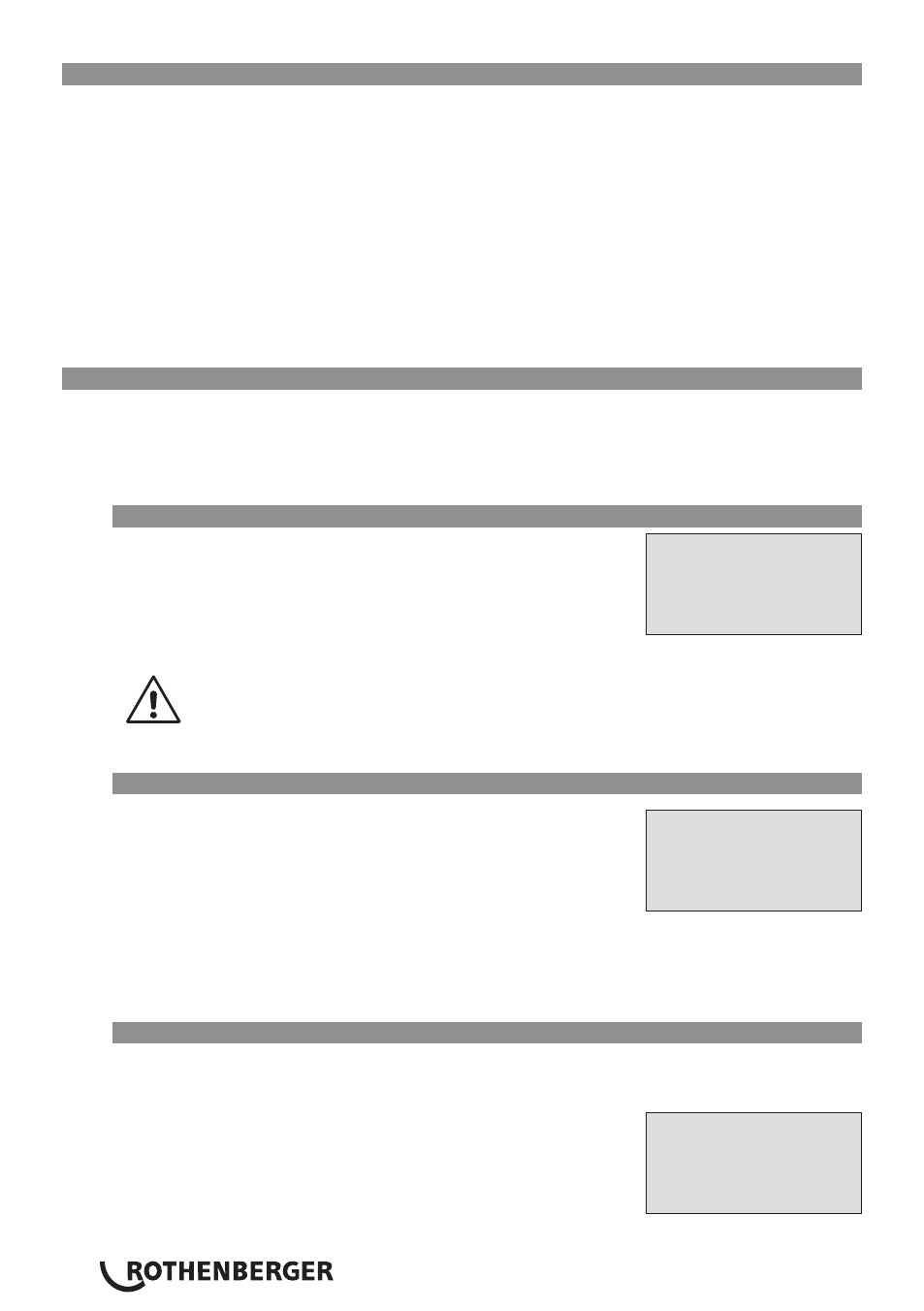
ENGLISH
16
4
Principles of Operation
The ROWELD ROFUSE V2 and the ROWELD ROFUSE+ V2 allow welding electrofusion fittings
that feature a bar code. Every fitting is provided with a tag with one or two bar codes on it. The
structure of this code is internationally standardized. The first code, encoding the data on proper
welding, complies with ISO 13950 and can be processed with the welding unit.
The model version ROWELD ROFUSE+ V2 allows additionally the manual input of the welding
parameters. The microprocessor-controlled welding unit
• controls and monitors the welding process in a fully automated fashion,
• determines welding duration depending on ambient temperature,
The latter is done by the temperature sensor located on the welding cable, which checks the
ambient temperature at regular intervals.
The unit monitors the characteristics of its power supply continuously. If one of these is out of
tolerance, welding is aborted or cannot be started.
5
Check-out and Operation
To operate the welding unit, be sure that it is set on a proper, level surface.
Be sure that power supply/generator protection is 16 A (slow blow).
Plug the power supply cord into the mains power supply or the generator.
Read and comply with the User’s Manual of the generator, if applicable.
5.1
Turning the Welding Unit On
After connecting the power supply cable to mains power or a
generator, turn the welding unit on using the On/Off switch. This
causes Display 1 to show
Display 1
Roweld
Welder
ROFUSE +
Version 2.0
.
Then the screen changes to Display 2.
CAUTION in case of System Errors! If during the auto-test that the unit performs
at start-up, an error is detected, a “System Error” message shows on the display.
When this happens, the welding unit has to be disconnected immediately from
the power suppy and the fitting, and it has to be shipped to the manufacturer
for repair.
5.2
Connecting the Fitting
Connect the connection terminals to the fitting and check for
proper
Display 2
Enter Fitting Code
14:32:11 21.10.12
Inp.Volt. 230V 50Hz
No Contact
contact. Use terminal adapters if needed. The contact
surfaces of the cable connection terminals or adapters and the
fitting have to be clean. Dirty terminals may lead to improper
welding and also to overheated and fused connection terminals.
Protect the cable connectors against getting dirty at all times.
Terminals and push-on adapters should be considered consumables
and, therefore, have to be checked before every welding operation
and replaced if damaged or dirty.
When the fitting is connected, the “No Contact” message (see Display 2) disappears.
5.3
Reading the Fitting Code with a Handheld Scanner
Only the bar code on the tag sticking on the fitting to be welded may be used. It is not acceptable
to read the fitting code tag of a fitting of a different kind if the intended one is damaged or
unreadable.
Read the fitting code by holding the scanner in front of the bar
code
Display 3
Start ?
Temp.: 20°C
HST 315mm 58s
SAT 40.00V 0.80Ω
at a distance of 5 to 10 cm (2 to 4 inches), where the red line
indicates the reading area. Then push the reading button. If the
data are correctly read, the welding unit confirms this by an audible
signal and displays the decoded data on the screen (see Display 3).