NORD Drivesystems BU0710 User Manual
Page 12
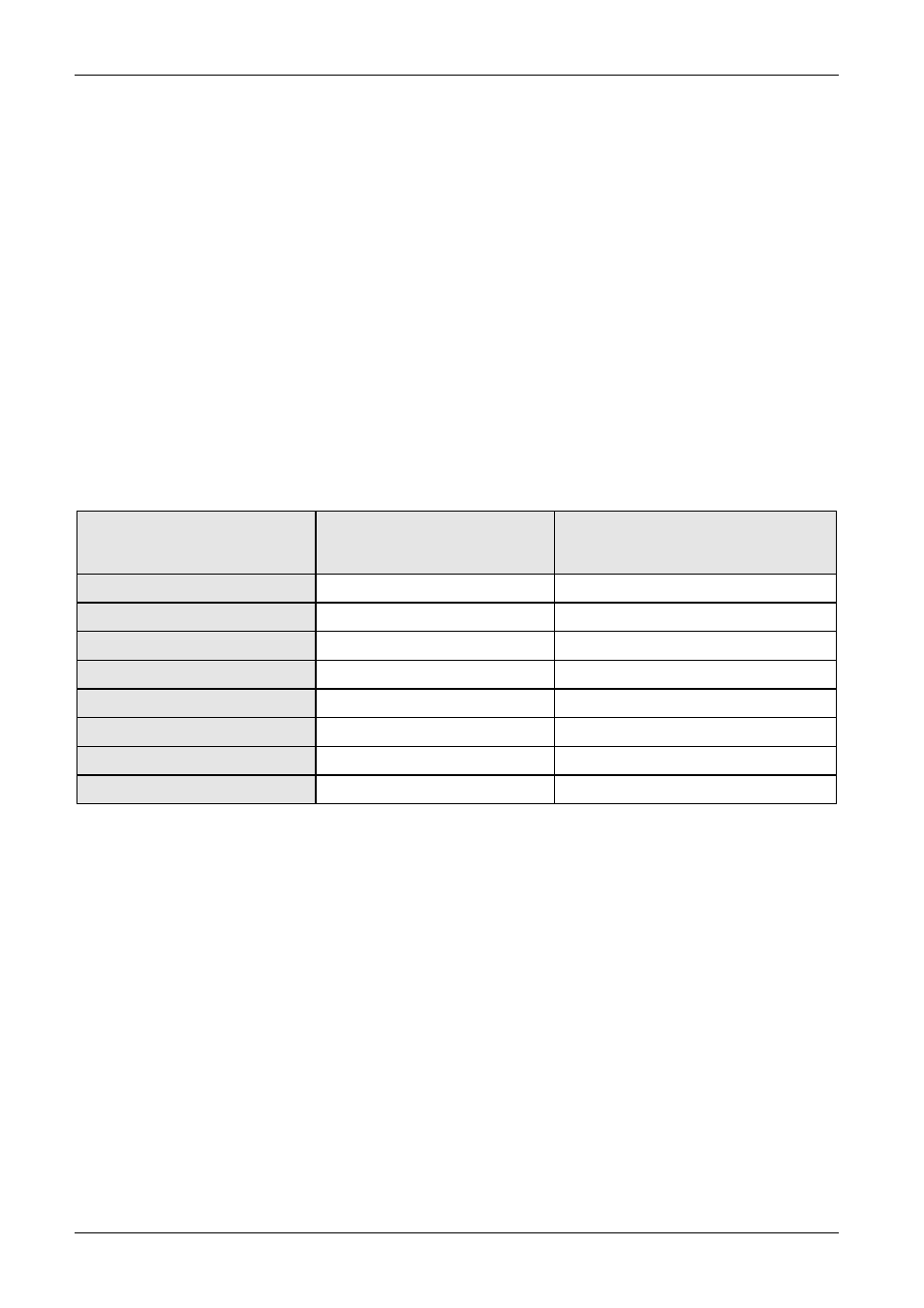
NORDAC SK 700E manual Posicon special extension
12
BU 0710 GB
2.3 Incremental encoder connection
Input for an incremental encoder with two tracks and a zero track, with TTL-compatible signals for drivers
according to EIA RS 422. Maximum current input to the incremental encoder must not exceed 250mA. Supply
voltage for the encoder is 5V.
The number of graduation marks per revolution may amount to between 500 and 5000 increments. It is set in
the "positioning" menu group which is accessed through parameter 606. If very long cables are used, or if the
motor speed exceeds 1500 1/min, the encoder should not have more than 2048 graduation lines per revolu-
tion.
With more than average cable lengths the cross sectional area must be large enough to ensure that voltage
won’t drop too much from one end of the cable to the other. This is especially important with regard to the
supply cables where the cross section can be enlarged for instance by connecting several wires in parallel.
Alternatively incremental encoders with a higher supply voltage requirement could be used. If the power
required to operate the incremental encoder does not exceed a range of 10 to 30 volts, the internal 15V
source will be sufficient (X10.2 terminal 42).
The screen of the encoder cable is connected to the screen angle using the PE clamps which are enclosed
with the basic unit.
Function
Colour
(with incremental encoder ERN 420)
Input terminals Posicon
special extension
SK XU1-POS
5 V supply
+5V
brown / green
X10.4.41 VO +5V
0 V supply
DGND
white / green
X10.3.40 GND /0V
Track A
A+
brown
X10.4.51 ENC1 A+
Track A inverse
A-
green
X10.4.52 ENC1 A-
Track B
B+
grey
X10.4.53 ENC1 B+
Track B inverse
B-
pink
X10.4.54 ENC1 B-
Track 0
ZERO+
red
X10.4.55 ENC1 N+
Track 0 inverse
ZERO-
black
X10.4.56 ENC1 N-
2.4 Absolute encoder connection
Input for an absolute encoder with ‘Gray Code’ and SSI interface. Signals are TTL-compatible in accordance
with EIA RS 422. The inverter will provide the encoder with a supply voltage of 15V. The resolution per
revolution, the maximum number of revolutions or alternatively the length of the transmitted word (8 – 24 bits)
can be set in parameter P605.
The absolute encoder should be installed on the shaft so that the scale zero of the encoder is in the correct
position. The mark treated as zero point by the inverter can be set by defining an offset value.
Multiplication and reduction parameters allow for a transmission ratio to be ensured between motor and
absolute encoder.
The sense of rotation of motor and absolute encoder need not necessarily be the same. If the sense of
rotation is different, a negative transmission ratio must be set.
With the 100kHz clock frequency used, cable lengths of up to 80m are allowed. The cables should be twisted-
pair and screened.
Absolute encoders may include break-of-wire checking provided that an extra voltage monitoring bit has been
assigned for that purpose.