For 2-way only, Dipswitches, Feedback signal – Warren Controls AmurAct Actuator Linkage and Motor User Manual
Page 8: Control signal - voltage, Configuration of dipswitches
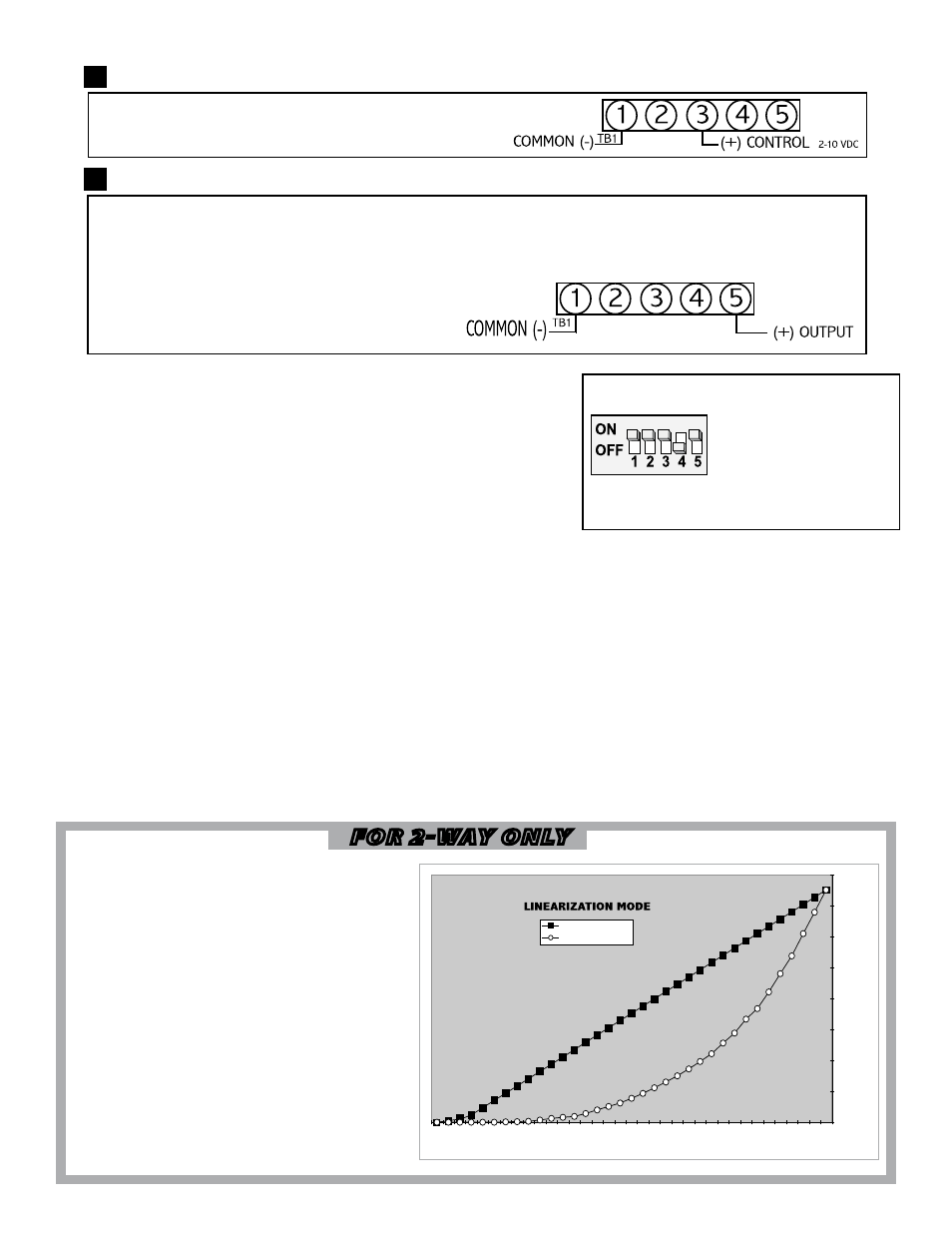
FEEDBACK SIGNAL
This signal is an output signal and not required for operation. The sole function is to provide a verified feedback signal that is proportional to rotation.
The actuator can be set to provide a 4-20 mA feedback signal (factory default) or a 2-10 vdc feedback signal. For 4-20 mA feedback dipswitch #4 must be
in the OFF position. For 2-10 vdc feedback, dipswitch #4 must be in the ON position. Connect the feedback wires to TB1 as shown below. If the actuator
is set for CCW rotation on increasing signal (factory default) and the actuator is at 90º rotation (facing the motor) the feedback will be 4 mA or 2 vdc, at
45 degrees rotation the feedback will be 12 mA or 6 vdc and at 0º
rotation (facing the motor) the feedback will be 20 mA or 10 vdc. If
the actuator is set for CW rotation on increasing signal the direction
of the feedback signal will be reversed.
CONTROL SIGNAL - Voltage
If the control signal is 2 - 10 vdc, connect the control wires to
TB1 as shown. Dipswitch #3
MUST be in the OFF position.
CONFIGURATION OF DIPSwITCHES:
Factory default configuration of the five dipswitches is shown below.
Switch #1
Factory default - ON
An increasing control signal causes the valve
stem to drive up, opening a two-way valve, or opening the L (lower) port and
closing the U (upper) port of a three-way valve. The valve stem will drive down
upon loss of signal. When Switch 1 is in the OFFposition an increasing control
signal causes the valve stem to drive down, closing a two-way valve, or closing
the L (lower) port and opening the U (upper) port of a three way valve. The valve
stem will drive up upon loss of signal.
Switch #2
Factory default - ON
Upon loss of power the Enerdrive® circuit will drive the valve stem down, closing a two-way valve, or closing
the L (lower) port and opening the U (upper) port of a three-way valve. When Switch #2 is in the OFF position, upon loss of power the
Enerdrive® circuit will drive the valve stem up, opening a two-way valve or opening the L (Lower) port and closing the U (upper) port of a
three-way valve.
Switch #3
Factory default - ON
The motor will accept a 4-20 mAdc control signal connected to terminals 1(-) and 3(+) on terminal block 1.
When Switch #3 is in the OFF position the motor will accept a 2-10 vdc signal.
Switch #4
Factory default - OFF
The motor will provide a 4-20 mAdc feedback output at terminals 1(-) and 5(+) on terminal block 1. When
Switch #4 is in the ON position the motor will provide a 2-10 vdc output.
Switch #5
(2-way) Factory default - ON This establishes a linear relationship between the control signal and valve stem lift. When Switch #5 is in the
OFF position a “non-linear” relationship is established between the control signal and valve stem lift. This is uniquely applicaple only on 2-way
valve linkages.
(3-way) Factory default - OFF
The 3-way linkage has a different signal to lift relationship and should not use the linearization feature.
For 3-way valves, switch #5 should always be
off.
Placing dipswitch #5 in its ON (Linearizing) position accomplishes
several objectives that may be helpful in specific control valve
installations. One result is that the entire input signal range is
applied to modulating the valve opening. Only at the very end
of the signal range does the AmurAct linkage drive into lockup.
Another result is that the inherent characteristic of the control
valve is preserved. “Linearizing” operation can provide linear flow
control when using a valve having linear trim.
Placing dipswitch #5 on its OFF (Non-Linear) position causes the
valve stem to rise very slowly in the beginning of its stroke, and
to rise increasingly rapidly as the valve opens. This mode uses the
first 25% of the control signal to move the linkage into and out
of lockup. “Non-Linear” operation may be useful when additional
control is needed at low flow rates, and additional response is
required for changes in higher flow rates.
Selection of the linearization mode (dipswitch #5) can be made
during operation, and dipswitch #5 should be left in the position
that produces the better system control result.
dipswitches
switch #1: Action &
Signal Loss
switch #2: Power Fail
switch #3: Signal
switch #4: Feedback
switch #5: Linearization
mA Signal Rotation
Linearized
Stem Lift
Non
Linearized
Stem Lift
0.023438
4
90
0.000000
0.00000
4.15
90
0.000000
0.00000
4.2
72
0.000000
0.00000
4.5
65.5
0.0234375
0.00000
5
59
0.046875
0.00000
5.5
54.75
0.070313
0.00000
6
50.5
0.093750
0.00100
6.5
46.25
0.117188
0.002000
7
42
0.140625
0.003000
7.5
39
0.164063
0.007000
8
36
0.187500
0.012000
8.5
33.5
0.210938
0.016000
9
31
0.234375
0.019000
9.5
29
0.257813
0.028000
10
27
0.281250
0.040000
10.5
25
0.304688
0.051000
11
23
0.328125
0.062000
11.5
21.5
0.351563
0.077000
12
20
0.375000
0.093000
12.5
18.5
0.398438
0.111000
13
17
0.421875
0.130000
13.5
15.75
0.445313
0.150000
14
14.5
0.468750
0.172000
14.5
13.25
0.492188
0.196000
15
12
0.515625
0.221000
15.5
10.75
0.539063
0.256000
16
9.5
0.562500
0.288000
16.5
8.5
0.585938
0.333000
17
7.5
0.609375
0.367000
17.5
6.5
0.632813
0.421000
18
5.5
0.656250
0.480000
18.5
4.25
0.679688
0.537000
19
3
0.703125
0.609000
19.5
1.5
0.726563
0.678000
20
0
0.750000
0.750000
4
4.15 4.2 4.5
5 5.5 6 6.5 7 7.5 8 8.5 9 9.5 10
10.5 1
1
11.5 12 12.5 13 13.5 14 14.5 15 15.5 16 16.5 17 17.5 18 18.5 19 19.5 20
0.00000
0.10000
0.20000
0.30000
0.40000
0.50000
0.60000
0.70000
0.80000
Linearized Stem Lift
Non Linearized Stem Lift
mA signal
s
te
m
L
if
t
FOR 2-wAY ONLY