Motor installation and calibration – Warren Controls AmurAct Actuator Linkage and Motor User Manual
Page 11
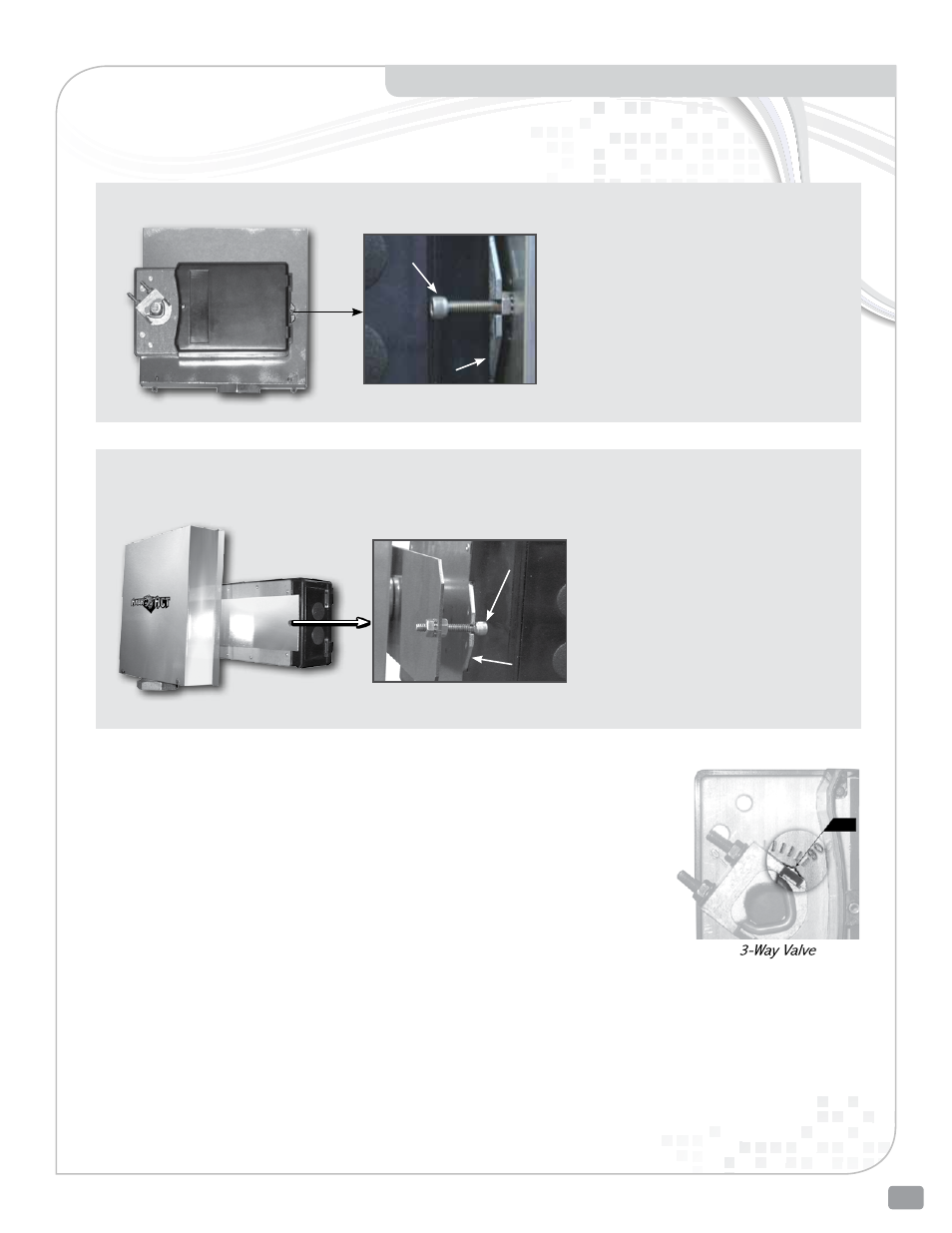
11
AmurAct
IOM_AA_RevH_0413
MOTOR INSTALLATION AND CALIBRATION
2.
To calibrate the motor output, remove the black cover, declutch the gear train and
manually rotate the output clamp as follows:
On a two-way valve, rotate the clamp fully clockwise until the pointer stops
at the 90-degree position. Release the clutch pushbutton to engage the
clamp at that position.
On a three-way valve, note that the 90-degree rotation scale is divided into
ten percent graduations. Rotate the clamp clockwise until the pointer is
midway between the 90-degree and adjacent graduation marks. Release the
clutch to engage the clamp at that position.
3.
Apply moderate pressure to minimize the gap between the motor and safety shield, and tighten the two 10 mm hex
nut to 150 lb. in. torque. Use of a 6 pt deep well socket wrench is recommended. Apply force gradually, as sudden, or
impact force may damage the u-bolt.
4.
Remove the c-clamp installed during the motor removal procedure.
5.
Connect field wiring and re-start the control valve as instructed in pages 6 through 9. Remember to press the reset/
auto-stroke push-button before applying a control signal.
Anti-rotAtion pin
Motor tAB
Anti-rotAtion
pin
Motor
tAB
stAndArd (Ls) LinKAGe
high TeMperATUre (le) linKAge
1.
Slide the motor output clamp over the linkage shaft; then install the anti-rotation screw, securing it with its locking
nut.
The Anti-Rotation Screw to the Motor Tab should have some play. See Below.
An anti-rotation pin engages a slot-
ted tab at the foot of the motor to al-
low alignment of the motor as its’ shaft
clamp rotates. The pin (screw) threads
into a boss on the linkage base and is
retained by a locking nut. Note that the
slotted motor tab rests and moves freely
on the threads.
An anti-rotation pin engages a slot-
ted tab at the foot of the motor to
allow alignment of the motor as its’
shaft clamp rotates. The pin (screw)
passes through the “Hi-Temp Mo-
tor Mounting Bracket, and is re-
tained by “kEP” nuts on either
side of the sheet metal. Note the
positions of the parts and that the
slotted motor tab rests and moves
freely on the threads.