Vms-25, Terminals, Product: series vm linear electric actuators – Warren Controls PICV Series User Manual
Page 18: Installation, Testing
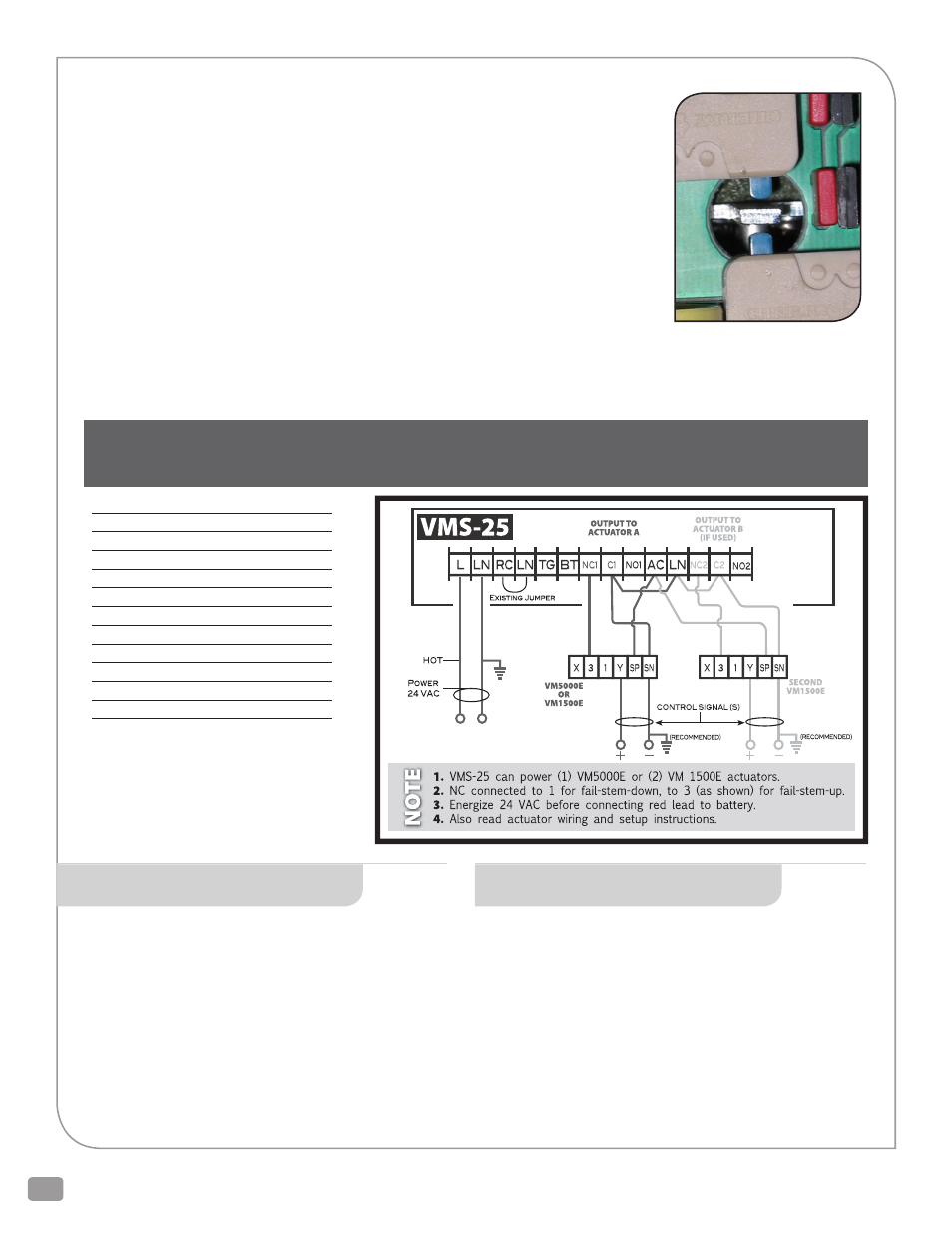
18
2600 Emrick Blvd • Bethlehem, PA 18020 • USA • 800-922-0085 • www.warrencontrols.com
PRODUCT: SERIES VM LINEAR ELECTRIC ACTUATORS
NATURE OF FAULT: Actuator motor does not de-energize at one end of travel. Actuator does not
respond to Input signal changes.
PROBABLE CAUSE: Over-travel device cannot reach limit switch activation point.
CORRECTIVE ACTION(S):
1. De-energize the actuator, both power and signal.
2. Remove the actuator cover and locate the two switches soldered onto the circuit board. Note
the small lever protruding through the board, between the switches.
3. Using a hex wrench, declutching if necessary, manually drive the actuator away from its’ end of
travel. Note that the lever moves to a “rest” position.
4. Loosen the circuit board mounting screws sufficiently to allow the board to be moved in its’
slotted mounting holes.
5. Position the board so the lever is centered between the switches and re-tighten the mounting
screws. Check position again, after tightening.
6. Re-energize the actuator, and perform “Auto-Stroke”. Observe that the actuator travels fully in
both directions, and comes to rest at the point dictated by the applied input signal.
LEVER, CORRECTLY
POSITIONED
BETWEEN
SWITCHES
INSTALLATION
1. Connect the VMS-25 to the actuators as shown. Connect NC1 or
NC2 to terminal 1 on an actuator to drive the valve stem down during
power failure or to terminal 3 to drive the valve stem up during a
power failure.
2. Connect VMS-25 to 24 volts AC power.
3. Connect the red wire to the battery positive (+) and the black wire
to the battery negative (-).
Note: Connect the 24 volt power to the VMS-25 before connecting
the battery. Connecting the battery first causes the VMS-25 to
go into the power failure mode. If there are conditions other than
power failure during which the actuator should be driven to the end
position, replace the jumper between LN & RC with a contact that
opens on demand.
TESTING
Disconnecting the jumper between LN & RC, with building
power on, will drive the actuator to the power failure position.
Testing the VMS-25 and the battery. Measure the voltage
between TG & BT. TG is negative. When the power supply is charging
correctly the voltage will be 13 - 14 volts DC. Disconnect LN or L and
then measure the voltage between TG & BT. If the battery is good
and adequately charged the voltage will be Between 10 - 12 volts
DC. VMS-25 is a standby power supply for VM1500E and VM5000E
actuators. It is intended to drive these actuators to either open or
close a valve during a power failure. The VMS-25 can power one
VM5000E or two VM1500E actuators.
For floating control, connect controller with dry contacts and
floating mid position between terminal NO1 and 1 and 3 for
Actuator A, and between terminal NO2 and 1 and 3 for Actuator B.
TERMINALS
VMS-25
Operation:
Proportional Normal: Terminal AC is connected to 24
VAC building power. Terminal LN supplies power to
SN. Actuator responds to modulating input signal.
Power Failure: Terminal AC changes to 24V square
wave from inverter. Terminal C2 connects to Terminal
NC2. Terminal NC2 supplies power to Termial 1 or 3 to
drive actuator to fail safe position.
L
System Power 24VAC
LN
System Neutral
BT
Battery Test
RC
Remote Control
TG
Test Ground
C1
Relay Common 1st Motor
C2
Relay Common 2nd Motor
NC1
Relay Normally Closed 1st Motor
NC2
Relay Normally Closed 2nd Motor
NO1
Relay Normally Open 1st Motor
NO2
Relay Normally Open 2nd Motor
AC
24 Volt Out