Warner Electric Blade Brake Clutch Application Guide User Manual
Page 4
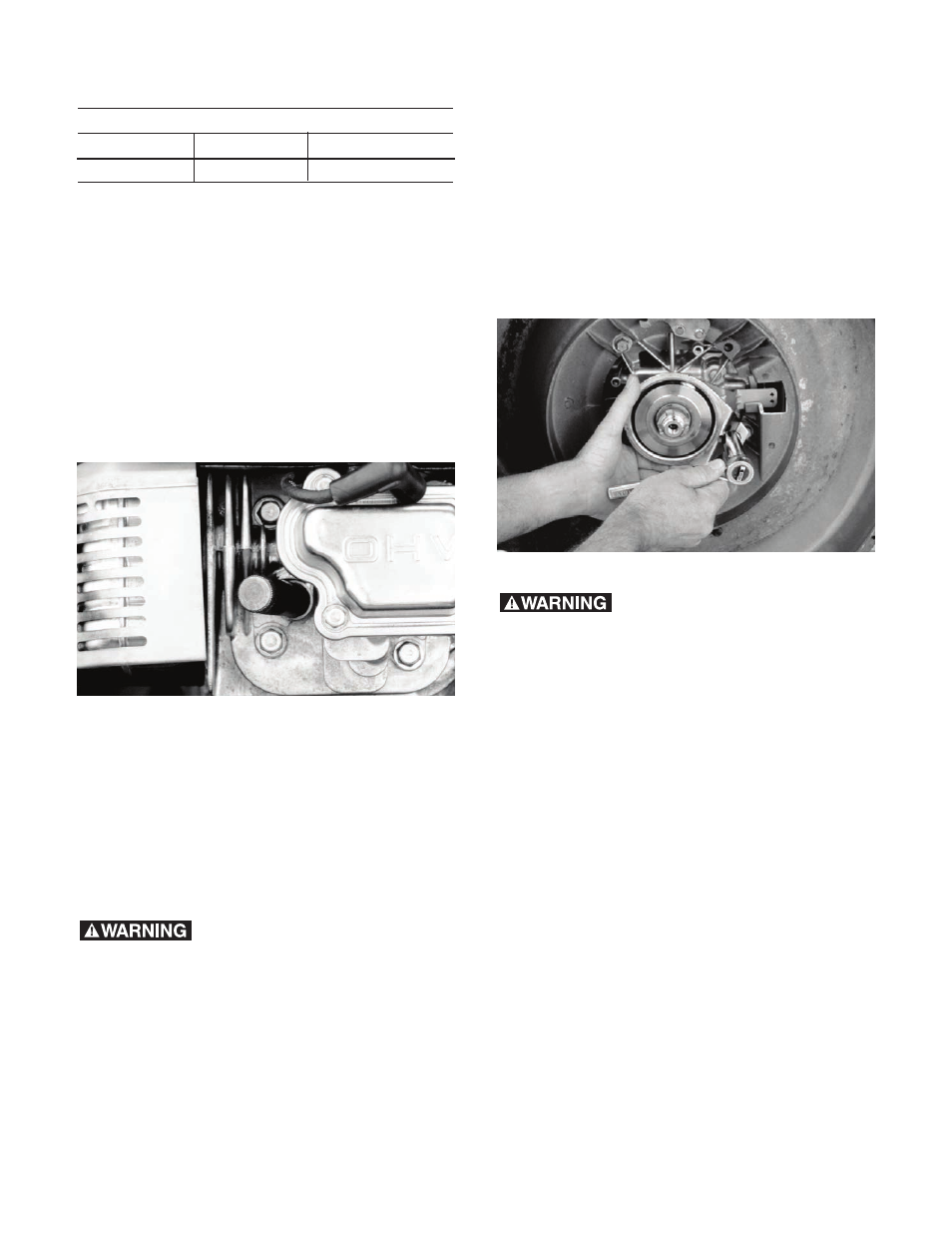
4
Warner Electric • 800-825-9050
P-1319-WE • 819-0465
Recommended Bolt Torque
Thread Type
48 ± 3 lbs.ft.
65 ± 5NM
3/8-24 UNF
48 ± 3 lbs.ft.
65 ± 5NM
M10X1.25-6g
Bolt to be grade #8 US, Grade #10 Europe.
Note: Please contact Warner Electric for assistance with other thread
sizes.
To obtain proper bolt torque (See Table 1), the
engine shaft must be held from rotating. Check
with the engine manufacturer for acceptable
methods of preventing shaft rotation. See figure 3
for piston stop used to prevent engine rotation.
If customer supplied bolt and washer is used
washer to be 3MM (0.118") thick and bolt to be
grade 10 Europe (grade # 8 US bolt). Do not use
lock washer.
The use of Loctite or other thread-locking
adhesive is not recommended and is not a
substitute for proper mounting bolt torque.
Proper mounting bolt torque is
essential for BBC operation and to prevent
premature failure of the BBC.
C. Anti-Rotation
BBC installations require an anti-rotation device
to prevent the brake plate from rotating. The
anti-rotation device should be rigidly mounted to
the mower deck or engine block. The anti-
rotation device must be designed to allow the
brake plate to move axially. Warner Electric
recommends that the anti-rotation device be
fabricated from a .469 inch (11.9mm) nominal
hardened steel pin.
Constraining the axial
movement of the brake plate may cause
the BBC to function improperly, leading to
increased blade stop times and premature
failure of the BBC.
D. Brake Actuation Spring
The actuating force for the braking function is
generated by a spring connected between the
brake spring attachment point (or one of the
clutch actuation cable attachment holes) and a
rigid location on the mower such as the deck or
engine block. Return spring is not provided with
the BBC.
The total rotation of the actuation arm from the
positive stop in the clutched position to the
positive stop in the braked position is 17°
nominal. A minimum of 150 in.lbs (16.95nm) of
torque is required to move the actuation arm
from the fully clutched to the fully braked
position. The spring force required to achieve
this torque is dependent on several factors such
as the location of the attachment points, the
angle of the spring compared to the plane, and
the tangent of rotation.
Figure 3
Figure 4
Table 1