Warner Electric SFP-400 User Manual
Page 3
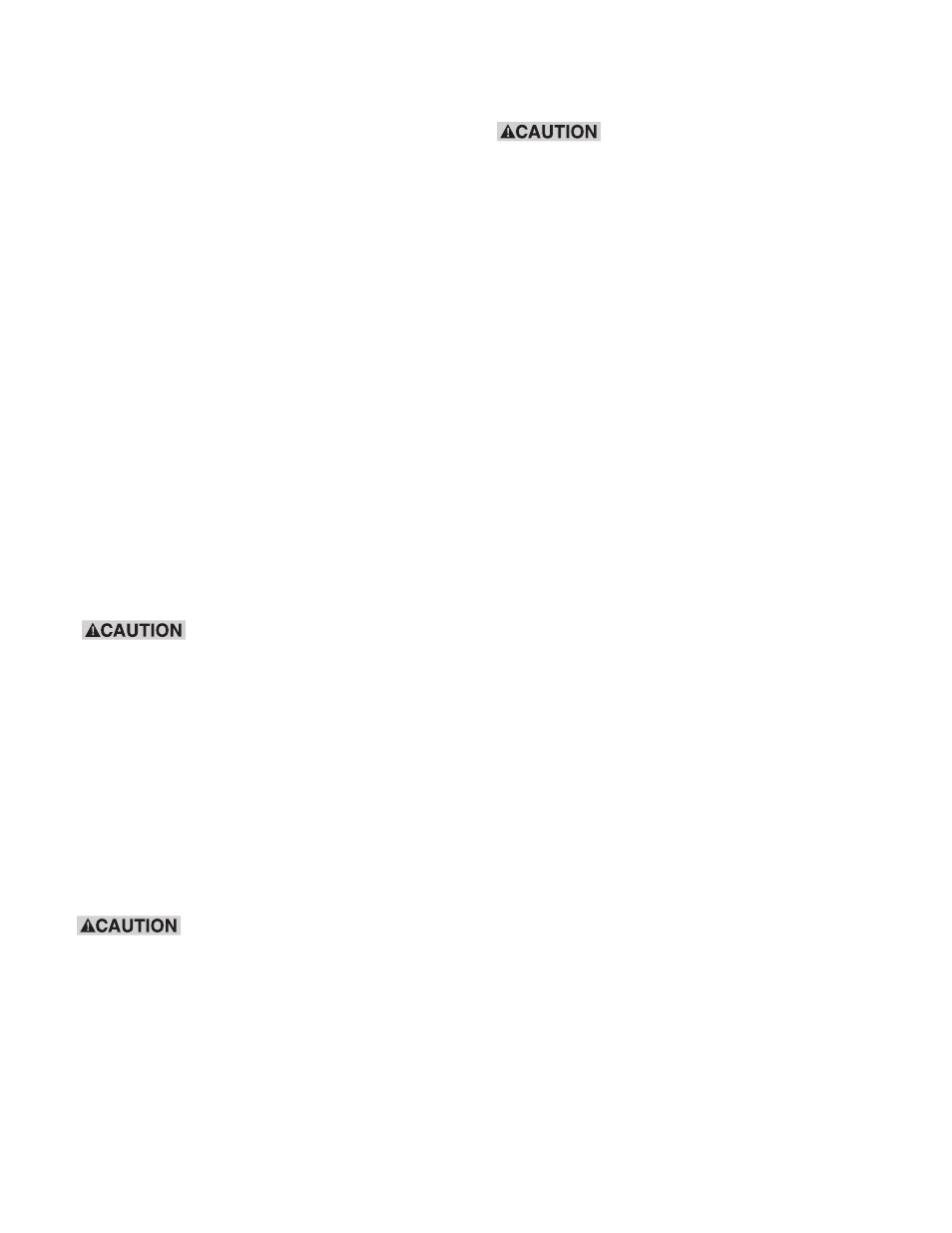
3
Warner Electric • 800-825-9050
P-231 • 819-0382
Installation
1. Check that the unit has arrived in good
condition. Each clutch comes with a terminal
accessory kit, part number 5103-101-002,
containing two screws, two terminal rings,
and two rubber terminal caps.
2. Fasten the user supplied pulley or sheave to
the clutch armature using the three threaded
mounting holes provided. Make sure that the
fasteners are short enough so they do not
bottom out on the armature. Refer to the
Dimensions section for bolt circle and thread
information. Use Loctite
®
242 or equivalent to
help assure thread retention.
3. For the SFP-400 only: To install the optional
conduit box, Warner Electric part number
5200-101-010, follow the separate installation
instructions provided with the conduit box to
assemble it to the clutch.
4. Slide the clutch onto the shaft.
Be sure the keyway is
positioned over the user supplied shaft key.
Alternately tighten the two setscrews to
secure the clutch to the shaft. (Depending on
the width of the pulley, it may have been
necessary to tighten the setscrews before
fastening the pulley.)
5. Attach a user supplied flexible strap or band
to the tab on the back of the field to secure it
to a stationary surface to prevent field
rotation.
The anti-rotation tab on the field
should not be rigidly fixed as this could
preload the bearing and reduce its life.
6. Make electrical connections from the DC
power source to the clutch. Either wire can
be attached to the + or - terminal. If a Warner
Electric control is used as the power source,
follow the connection diagram supplied with
the control.
Maintenance
SFP-250 and SFP-400 are dry
friction devices. DO NOT apply oil or
lubrication.
If correctly sized and installed, the SFP-250 or
SFP-400 should run virtually maintenance free.
As with all shaft mounted clutches, the ability to
dissipate heat will improve life. Care should be
taken to ensure adequate ventilation. For
demanding applications where the clutch is
being cycled on and off rapidly, high
temperatures can lead to accelerated wear.
After the friction surfaces undergo a significant
amount of wear, the armature may not pull in or
the unit will show a reduction in torque carrying
capability. Then the clutch will need to be
replaced.
The clutch’s operating environment can also
affect its life. If units are used on machinery
where fine, abrasive dust, chips, or grit are
dispelled into the atmosphere, shielding the
clutch may be necessary for maximum life.
Where the clutch is used near gear boxes or
transmissions requiring frequent lubrication,
means should be provided to protect the friction
surfaces from oil and grease to prevent torque
loss.