Teledyne 3010TAC - Split architecture trace oxygen analyzer (EU - CENELEC) User Manual
Page 19
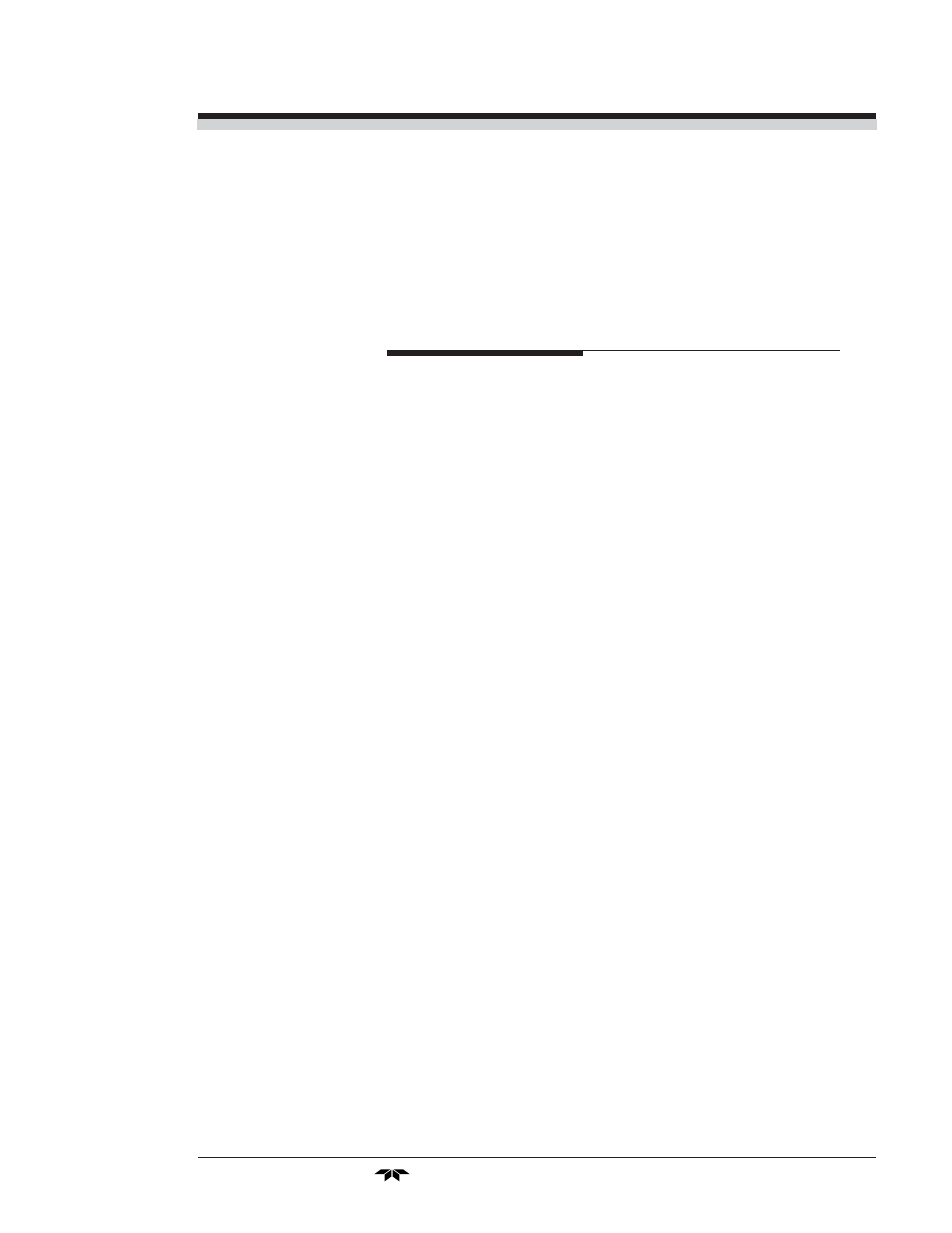
Part I: 2-1
Oxygen Analyzer
Part I: Control Unit
Teledyne Analytical Instruments
Operational Theory
2.1
Introduction
The Model 3010TAC Oxygen Analyzer Control Unit uses an 8031
microcontroller with 32 kB of RAM and 128 kB of ROM to control all
signal processing, input/output, and display functions for the Model
3010TAC analyzer. (The sample system and Micro-Fuel Cell sensor are
covered in Part III, Remote Probe, in this manual.) System power is sup-
plied from a universal power supply module designed to be compatible
with any international power source.
2.2
Electronics and Signal Processing
All of the Analyzer electronics are located on Printed Circuit Board
(PCB) assemblies inside the Control Unit chassis. The PCB locations are
illustrated in section 5, Maintenance.
Refer to Figure 2-1, Block Diagram of the 3010TAC Electronics:
In the presence of oxygen, the sensor (in the Analysis Unit) generates
a current. A current to voltage amplifier (in the Control Unit) converts this
current to a voltage.
The second stage amplifier amplifies the voltage. It also uses a signal
from the thermistor (which is physically located in the Analysis Unit cell
block) to provide temperature compensation for the sensor signal. The
thermistor is a temperature dependent resistance that changes the gain of
the amplifier in proportion to the temperature changes in the block. This
thermistor signal compensates for the change in the cell output due to the
temperature changes. The result is a signal that is temperature independent.
The output from the second stage amplifier is sent to an 18-bit analog to
digital converter controlled by the microprocessor.