Magnum Venus Plastech Flex Molding Process IVX3 INJECTION VALVE 8010 User Manual
Page 32
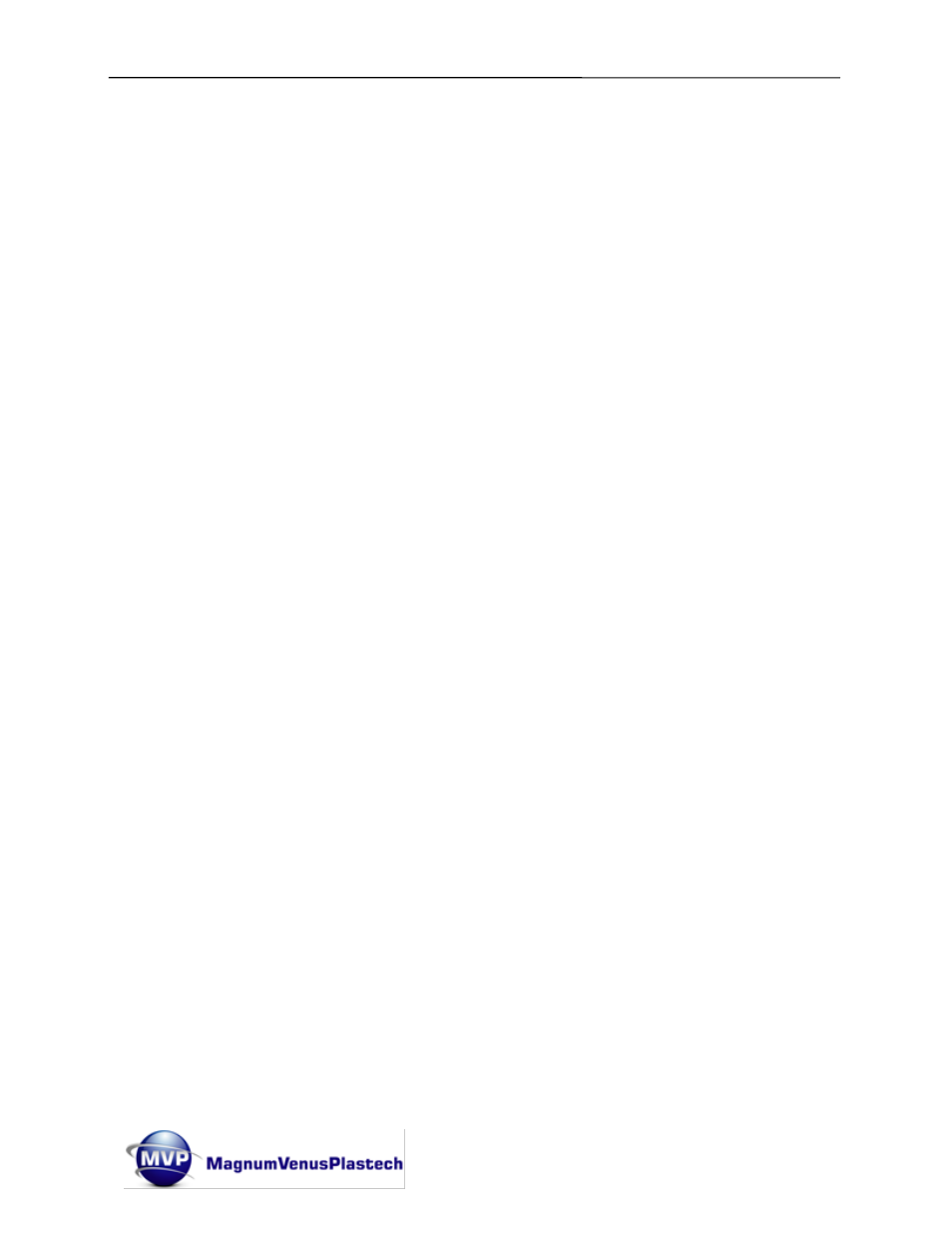
IVx3 Injection Valve Manual
Rev. 03/2012
Page | 32
7. Once a suitable vacuum level is reached, close the isolation valve on the Service
Module to isolate the vacuum source from the IVX3’s injection port. Ideally the
level on the vacuum gauge should remain stationary and the vacuum should be
maintained.
8. Actuate the IVX3 to the Purge position; the vacuum level should decrease slightly
as the seal moves. In this position the vacuum level should again be maintained.
NOTE: It is important that the valve does not leak in the purge position as in
production; air could be drawn into the part during the curing cycle.
9. Operate the valve a number of times between the Closed and Purge positions and
ensure the vacuum level is maintained.
10. Operate the valve to the Inject position; the vacuum should be exhausted and the
gauge should fall to zero.
NOTE: Once a suitable vacuum level has been achieved, the vacuum generator
(source) can be turned off. If the valve is not leaking, this level will be maintained.
Fluid Section Testing
– Pressure:
WARNING: During pressure testing, ensure the IVX3’s resin injection port is
directed away from yourself and others. Some of the tests will vent air through this
port.
1. Place the IVX3 on a bench; ensure the injection port is not connected (for example
into the universal insert on the top of the IVX3 Service Module).
2. Connect the Inject output on the top of the Service Module to the Inject signal port
on the IVX3.
3. Connect the Purge output on the top of the Service Module to the Purge signal port
on the IVX3.
4. Ensure the IVX3 is in the closed position.
5. Connect the IVX3 Purge Outlet to the indicator on the Service Module or a
pressure gauge.
6. Connect the IVX3 Resin Inlet to the pressure output on the Service Module (6
–7
bar / 87-100 PSI) and check the indicator/gauge. If pressure is seen here, the
valve is leaking between the resin Inlet and Purge outlet.