Fluid Components International FLT Series Rack Mount User Manual
Page 13
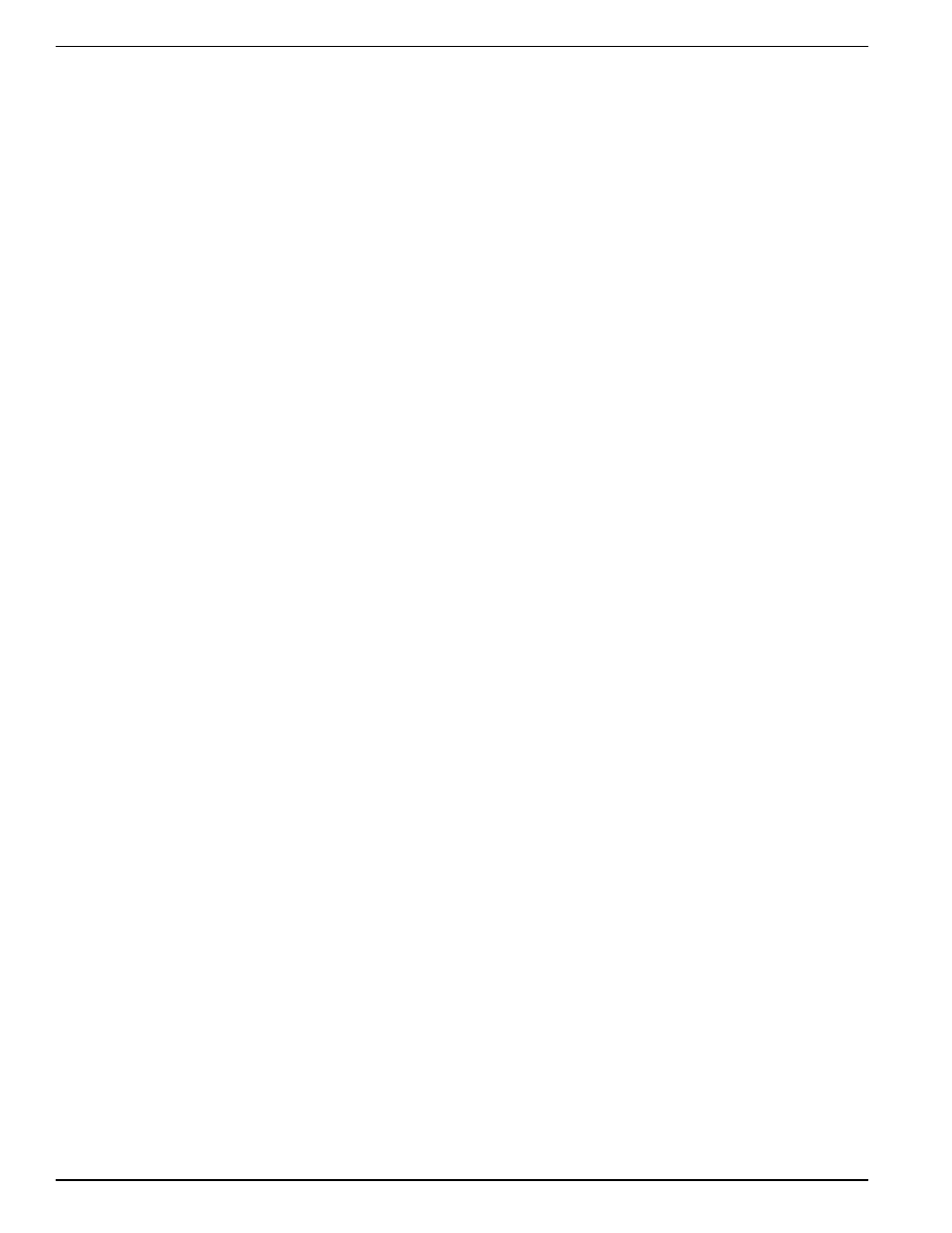
FLUID COMPONENTS INTL
APPENDIX D - TEMP COMP
FLT
Series FlexSwitch
Rack Mount
D - 2
Doc. No. 06EN003250 Rev. N/C
2.
Write down where the heater wattage control jumper is located on the control circuit. Refer to Figure 3-1.
Remove the heater wattage control jumper and install it in position J4 [J30] (heater off). Refer to Figure 3-1 for
the jumper location.
3.
Remove jumpers J1 and J2 [J27 and J28] from the control circuit and set them aside.
4.
Connect the DMM from TP1 (next to J1) [TP3 (next to J27)] to the right jumper post of J1 [J27]. Set the DMM
to ohms. See Figure D-1 for test point placement.
5.
Adjust potentiometer R9 [R50] [TP3] until the DMM reads the ohm value for R9 [R50] as shown on the Temp
Comp calibration sheet that is in the plastic page protector in the back of this manual.
6.
Remove the DMM and connect it from TP2 (next to J2) [TP4 (next to J28)], to the right jumper post of J2 [J28].
See Figure D-1 for the jumper post location.
7.
Adjust potentiometer R12 [R51] until the DMM reads the ohm value for R12 [R51] as shown on the Temp
Comp calibration sheet.
8.
Remove the DMM and reinstall the jumpers. (Leave the heater jumper installed in the off position, J4 [J30].)
9.
Connect the adapter cable to connector P2 and reinstall the control circuit on the socket. If the adapter cable is
not available refer to the P2 pin out chart in figure D-1
10. Connect the DMM to the adapter cable or P2 with the positive lead connected to P2-1 and the negative lead
connected to P2-2. Set the DMM to volts DC.
11. Turn on the instrument power and wait fifteen minutes for the instrument to stabilize. During this time make
sure that the process media is flowing or the sensing elements are submerged. Do not make the following
adjustment in still gas.
12. Adjust potentiometer R3 [R49] until the DMM reads 0 volts
±
5mV.
13. Turn off the instrument power and remove the DMM. Also remove the jumper from J4 [J30] and install it in it's
original position.
The Temp Comp adjustments are now restored. Turn on the power and make sure the instrument is functioning
properly. Make adjustments to the alarm set points if needed.
Field Temp Comp Calibration
If the application of the instrument changes the Temp Comp may need to be re-calibrated. An example of when the
Temp Comp needs to be re-calibrated is as follows: The process media is gas, the factory set Temp Comp is 40 to
140 °F. The instrument is then placed in an application that varies in temperature from 300 to 400 °F. In this case
the instrument's accuracy would be greater with a new Temp Comp calibration performed.
Another example of where the accuracy will be affected and a Temp Comp calibration would need to be done is
when the process media is changed, i.e. from water to heavy oil.
Temp Comp calibration is possible to do in the field if the test conditions are met and the data is measured correctly.
However, in many applications it is difficult to achieve these parameters and it is easier to have the switch factory
calibrated. To do the procedure the following parameters are required:
•
The maximum temperature differential does not exceed 100 °F.
•
The maximum temperature does not exceed the instruments rated maximum temperature.
•
The velocity at which the switch will alarm needs to be known.
Equipment Required
1 each
DC Power Supply, 0 to 20 Vdc minimum, at 0.5 Amps.
2 each
5-1/2 Digit DMM with 4 wire clip leads.
1 each
#1 Philips screw driver.
1 each
#1 Flat blade screw driver.
1 each
Flat screw driver, capable of adjusting control circuit potentiometers.
Insulating varnish or equivalent to reseal the potentiometers.