Brooks, Model 5851e – Brooks Instrument 5851E User Manual
Page 29
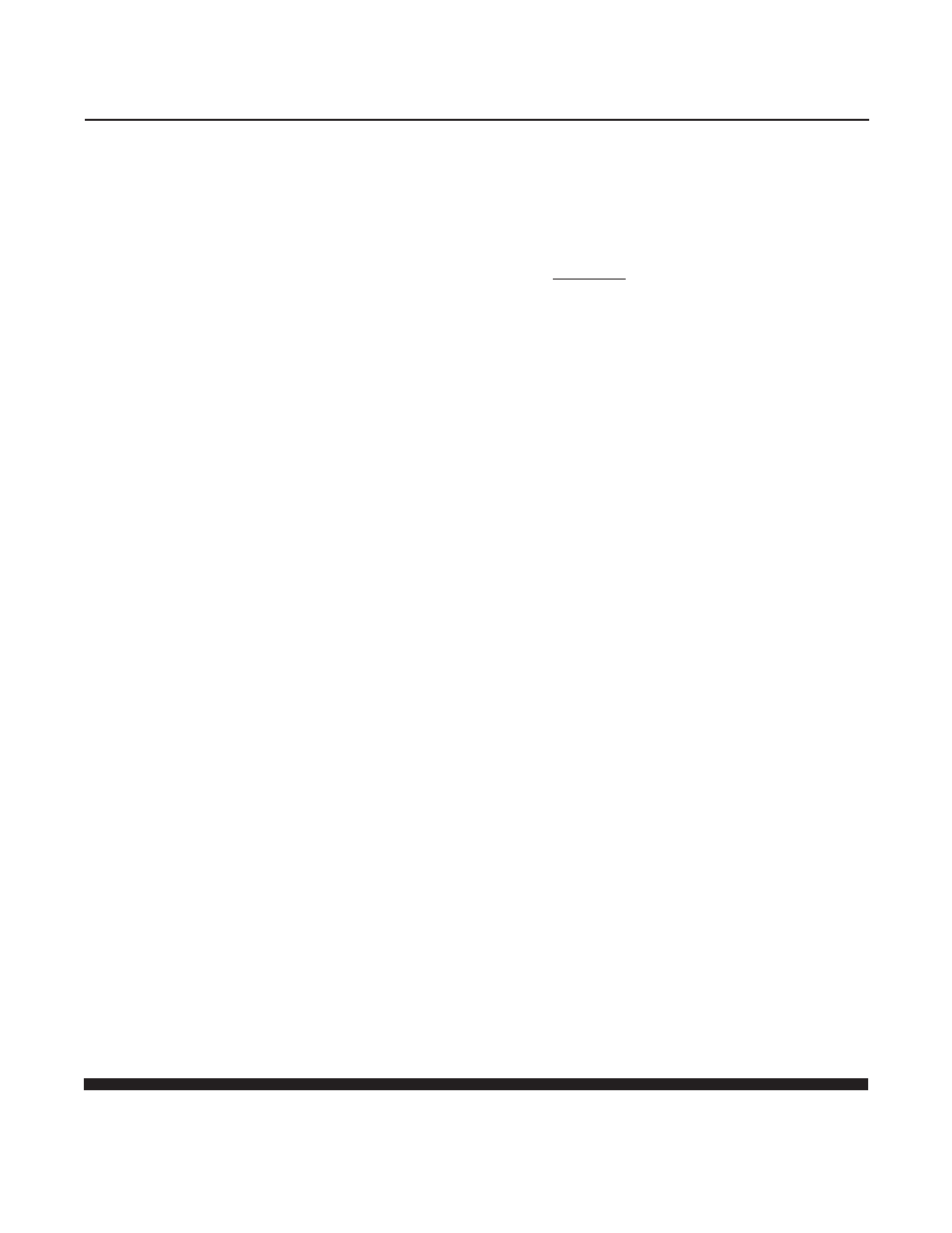
3-9
Brooks
®
Model 5851E
Section 3 Operation
Installation and Operation Manual
X-TMF-5851E-MFC-eng
Part Number: 541B104AAG
November, 2008
Example;
What is the percent of full scale error when full scale is equal to 100
slpm?
Measured flow rate = 48.5 slpm
Desired flow rate = 50.0 slpm
(48.5 - 50)
Full scale error = 100
= -1.5%
100
i. Calculate the TP2 correction voltage:
(error recorded in Step h) x 0.450 Volts
Example:
Error = -1.5%
TP2 correction voltage = -1.5 x 0.450 = -0.675 Volts
New TP2 voltage = 0 Volts + (-0.675) = -0.675 Volts
j. Set the command potentiometer for 100% flow (5.000 V). Connect the
DVM positive lead to TP2 and the negative lead to TP4.
k. Adjust the linearity potentiometer for an output equal to the new calcu-
lated TP2 voltage.
l. Repeat Steps f, g and h.
1. If the error recorded in Step h is less than 0.5%, then the calibration
procedure is complete.
2. If the error is greater than 0.5% set the command potentiometer for
100% (5.000 V). Connect the DVM positive lead to TP2 (linearity
voltage) and the negative lead to TP4 (circuit common). Calculate a
new TP2 voltage as follows:
error
measured
New TP2 voltage =
recorded in
x
0.450 V
+
TP2
Step i
voltage
Example:
Controller error = 0.7%
Measured TP2 voltage = -0.567 Volts
TP2 correction = 0.7 x 0.450 = 0.315 Volts
New TP2 correction = 0.315 + (-0.567) = 0.252 Volts
Adjust the linearity potentiometer for an output equal to the new TP2
voltage and then repeat Steps f, g and h.
Note: The voltage at TP2 can range from -10 to +3 Volts, however, it
is recommended that this voltage stay between -2.5 and +2.5 Volts
for proper operation. If the recommended voltage range is exceeded
the desired accuracy and/or signal stability may not be achieved. If
one of the limits is reached, check the restrictor sizing. Refer to
section 4-7.
3-5 Response
Fast Response Adjustment
Two methods of adjusting the step response of the Model 5851E mass
flow controllers can be used. No. 1 describes a method that will get the
step response close to optimum quickly and without any flow measuring
equipment. This method should be used when the response time of the