Brooks, Model sla5840 – Brooks Instrument SLA5840 User Manual
Page 20
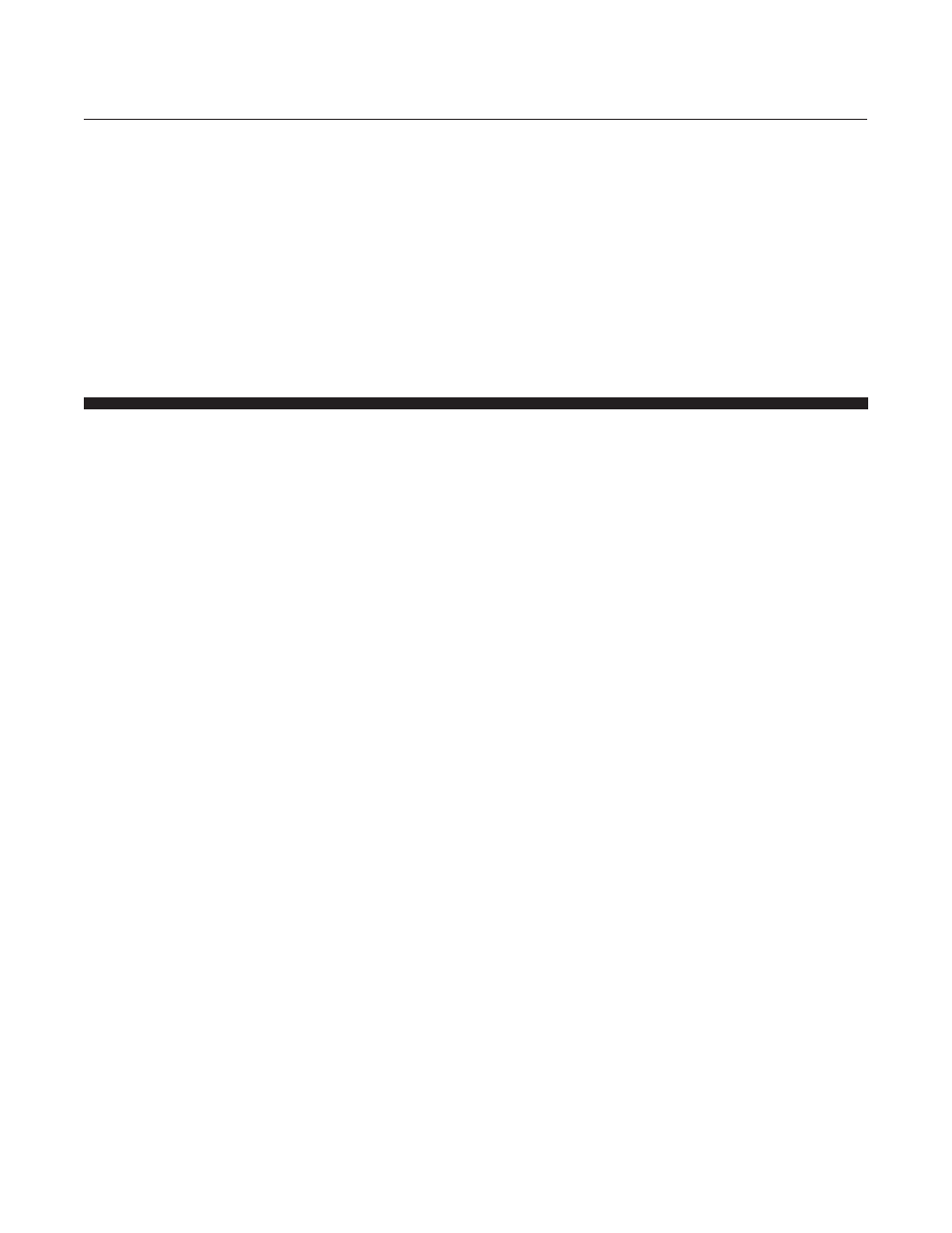
3-2
Brooks
®
Model SLA5840
Section 3 Operation
Installation and Operation Manual
X-PR-SLA5800-RT-eng
Part Number: 541B120AAG
August, 2009
The DeviceNet Instruction Manual describes further details on specific
communication features.
Calibrations will appear in the calibration table in the same order as they
appeared on the customer order, unless otherwise specified. The first listed
gas will appear as calibration #1 the second as calibration #2 and so on.
Note that unless specified otherwise on the customer order any unit containing
a single calibration will have that calibration stored in calibration position 1.
3-4 Analog I/O Mode of Operation
The following paragraphs describe the basic features of the Brooks Digital
Series RT's. NOTE: Read Section 3-3, Features, before reading this
section. See DeviceNet Supplemental Instruction Manual for specific
details on communication features.
A. Functional Description
The analog interface is consistent with other Brooks analog RT. This
includes a 0-5 volt setpoint input, 0-5 volt flow signal output, Valve Override
input, and Mode Select input pin. All analog signals available are on the 15
pin D-connector. (See Fig. 2-1 for connections). Note that one formerly
unused connector pin, pin 13, now allows selection of up to ten separate
calibrations. The contents of the ten calibrations are determined from the
customer order. Only those calibrations ordered will be available in the
instrument. Unless otherwise specified, a Delta Class RT ordered with only
one calibration will have that calibration stored in calibration #1. Before
operating the RT, apply power and warm-up the instrument for
approximately 45 minutes. After warm-up, apply gas pressure then
proceed by following the instructions in the following sections.
B. Analog I/O Setpoint
This input allows the user to establish the RT setpoint. The usable range of
this input is from 0 to 5.5 Vdc which corresponds to 0 to 110% of the RT full
scale flow rate. Setpoints below 45 mV will be treated as 0 volt setpoints.
For setpoints below 0 Vdc the RT behaves as if a 0 Vdc setpoint is present.
Setpoints above 5.5 Vdc will cause a setpoint of at least 110% FS.
C. Analog I/O Flow Signal
This output is used to indicate the flow signal. The range of this signal is
from -0.6 to 6.0 Vdc, with the range of 0 to 6.0 Vdc corresponding to a
calibrated flow signal of 1 to 120% of the full scale flow rate. A negative
flow signal indicates reverse flow through the device, but is NOT
calibrated.
D. Valve Override
This input allows the valve to be forced to its most closed state or its most
open state, regardless of the setpoint. If this input is not electrically connected
the RT will operate according to the current values of the other RT inputs. If
this input is held at 0 Vdc or -15Vdc the valve will be forced to its most
closed state. If this input is head at +5 Vdc or greater (max. =24 Vdc).