Ii71e page 2 of 2 – C.E. Niehoff & Co. C701etc/C703etc Alternator OEM Installation User Manual
Page 2
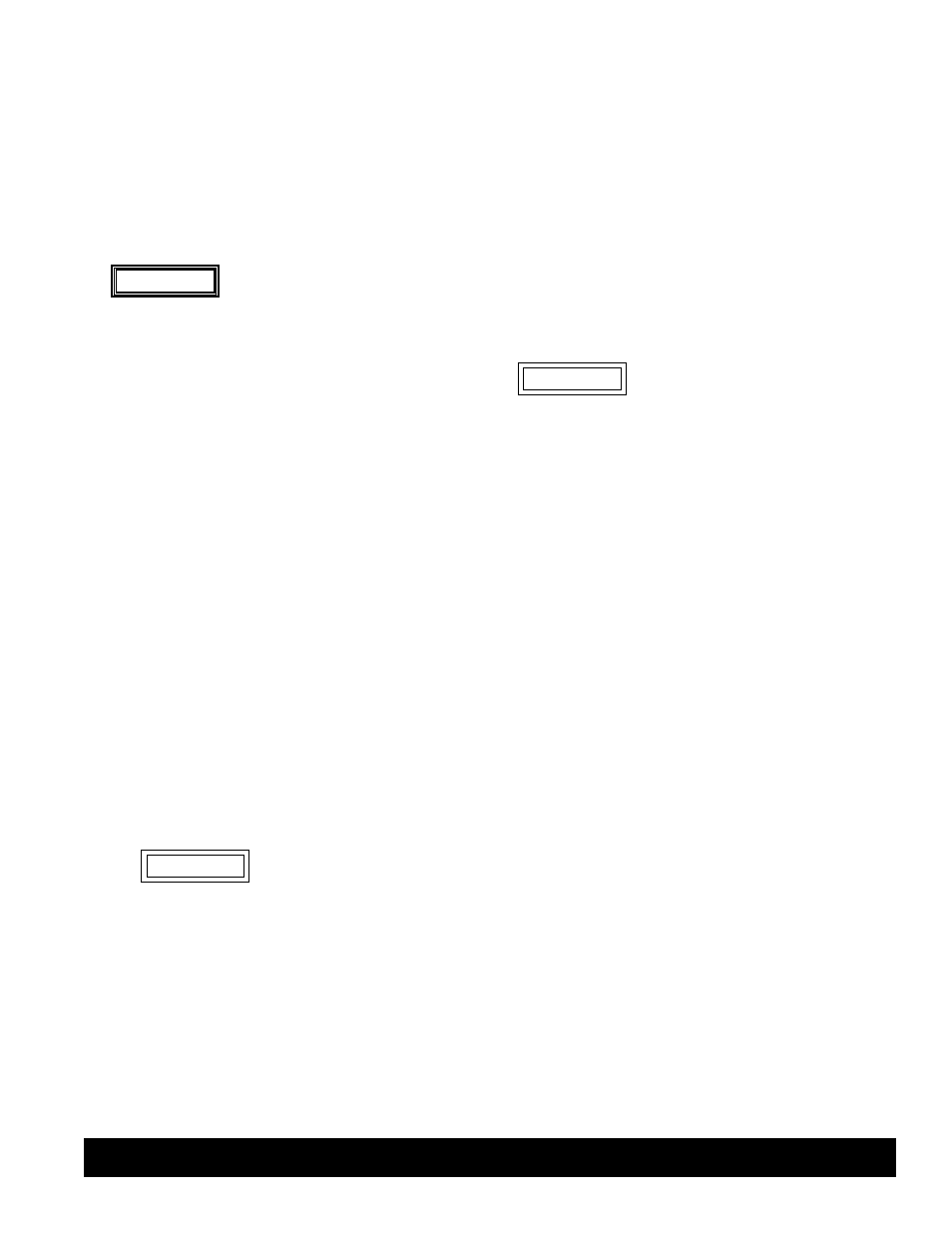
II71E
Page 2 of 2
C. E. Niehoff & Co. • 2021 Lee Street • Evanston, IL 60202 Tech Services Hotline 800-643-4633
4. Belt tension guidelines shown below are a starting
point for manual and automatic belt tensioners.
• K-section pulley: 8 grooves minimum,
10 grooves preferred.
• Belt wrap: 180 degree nominal. Less wrap
requires a pulley with more grooves and
more belt tension.
• Belt tension: 80 lbs to 120 lbs nominal. More
pulley grooves permit lower belt tension.
For further questions, please contact drive belt
manufacturer.
Either too low and too high belt tension
causes premature bearing failure. Too
low belt tension causes belt slip, pulley
heating, bearing heating, and ultimately
bearing failure. Too high belt tension
increases bearing fatigue, resulting in
bearing failure.
5. Regulator electrical connections:
a. Make sure alternator-to-regulator harness plug
is secure in regulator receptacle.
b. Connect IGN terminal on regulator to ignition
source through oil pressure switch, using
proper ring terminal. Torque #10-24 terminal
nut to 3.4 Nm/30 lb. in. Torque M5 terminal nut
to 4.5 Nm/40 lb. in.
c. Connect P terminal to tachometer or relay.
P terminal taps AC voltage, typically half the
charge voltage. Use proper ring terminal.
Torque 1/4-20 terminal nut to 3.4 Nm/30 lb. in.
Torque M6 terminal nut to 4.5 Nm/40 lb. in.
d. D+ terminal provides 28 VDC sense voltage to
multiplex controller. When connecting D+
terminal to controller through a relay, the relay
coil must be diode protected and rated for
proper voltage. Use proper ring terminal.
Torque 1/4-20 terminal nut to 3.4 Nm/30 lb. in.
Torque M6 terminal nut to 4.5 Nm/40 lb. in.
6. Alternator electrical connections:
a. Connect battery positive cable from vehicle to
alternator B+ terminal. Torque B+ terminal on
alternator to 30 Nm/22 lb. ft. Torque cable
clamp hardware to 10 Nm/90 lb. in.
B+ cable must be supported by
cable clamp within 12 in. of B+
output terminal to avoid prema-
ture failure of B+ output terminal.
CEN recommends using cable
clamp attached to alternator anti-
drive end housing for support.
b. Connect ground cable from vehicle to alternator
B– terminal. Torque B– terminal on alternator
to 15 Nm/11 lb. ft.
7. Alternator output test (conduct test with fully
charged batteries):
a. Turn on 28-volt battery system and start
engine.
b. Turn on all vehicle loads, including interior/
exterior lights and air conditioning.
c. Measure voltage at alternator. Voltage reading
should be 27.6 – 28.0 V on low setting of
regulator and 28.5 – 29.0 V on high setting.
See CEN Troubleshooting Guides for further
information.
d. Check battery cable voltage drop. There should
be no more than 0.4 V drop on each leg from
alternator to battery.
e. Road test vehicle for about 20 minutes.
f. Following road test, repeat output test.
Regulators used with these alternators
feature overvoltage cutout (OVCO), which
disables alternator output in an overvoltage
condition. Restarting engine resets OVCO
circuit. When an overvoltage condition is no
longer present, alternator and regulator
should operate normally. If a no-output con-
dition should occur, follow above reset pro-
cedure to determine if OVCO trip is cause.
CAUTION
CAUTION
WARNING