Eddy current inspection, Eddy current technology, Benefits of eddy currents – Atec Panametrics-Olympus-Omniscan-MX User Manual
Page 8: Eddy current probes
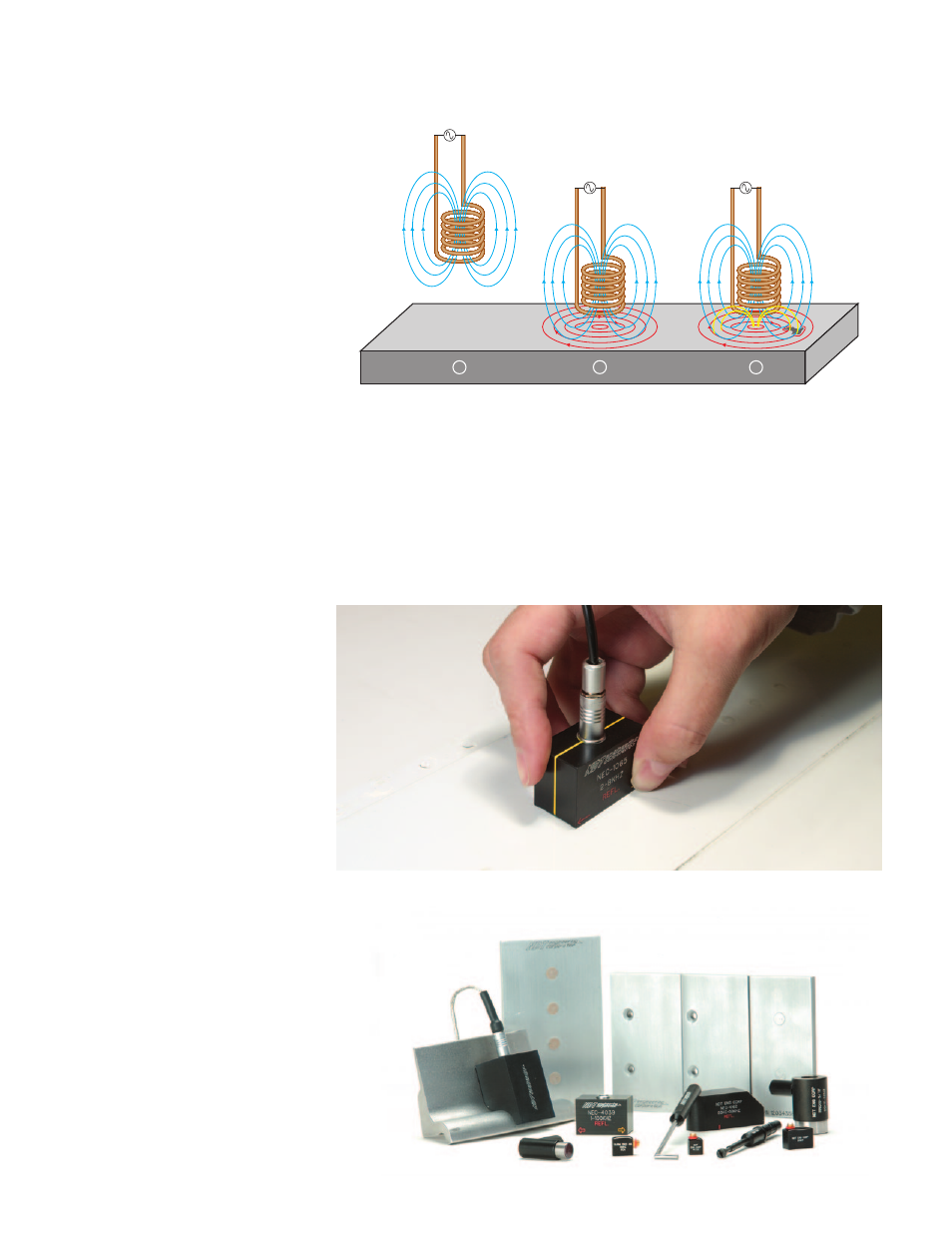
www.olympus-ims.com
8
Eddy Current Inspection
Eddy Current Technology
Eddy current testing (ECT) is a method for
the inspection of metallic parts. The probe,
excited with an alternating current, induces
an eddy current in the part being inspected.
Any discontinuities or material property
variations that change the eddy current flow
in the part are detected by the probe as a
potential defect.
Over the years, probe technology and data
processing have continuously progressed
so that the eddy current technique is now
recognized to be fast, simple, and accurate.
This is why the technique is widely used in
the aerospace, automotive, petrochemical,
and power generation industries in the de-
tection of surface or near-surface defects in
materials such as aluminum, stainless steel,
copper, titanium, brass, Inconel, and even
carbon steel (surface defect only).
Benefits of Eddy Currents
Eddy currents offers the following benefits:
•
A quick, simple, and reliable inspection
technique to detect surface and near-
surface defects in conductive materials
•
Can be used to measure the electrical
conductivity of materials.
•
Measurement of nonconductive
coatings
•
Hole inspection with the use of a high-
speed rotating scanner and surface
probe
Eddy Current Probes
Olympus NDT standard eddy current
probes are available in different configura-
tions:
•
Bolt hole probes
•
Surface probes, in various shapes and
configurations
•
Low-frequency Spot and Ring probes
•
Sliding probes
•
Wheel probes
•
Conductivity probes
•
Speciality probes made for specific
applications
Reference standards with EDM notches can
be manufactured according to the applica-
tion specifications.
a
b
c
Probes used to perform eddy current inspections are made with a copper wire wound to form a coil. The coil shape can vary to
better suit specific applications.
1.
The alternating current flowing through the coil at a chosen frequency generates a
magnetic field around the coil.
2.
When the coil is placed close to an electrically conductive material, an eddy current is
induced in the material.
3.
If a flaw in the conductive material disturbs the eddy current circulation, the magnetic
coupling with the probe is changed and a defect signal can be read by measuring the
coil impedance variation.
Surface preparation is minimal. Unlike liquid penetrant or magnetic particle inspection, it is unnecessary to remove the paint from
the surface to inspect the parts.