Measurement accuracy – Atec Anritsu-ML2400 Series User Manual
Page 9
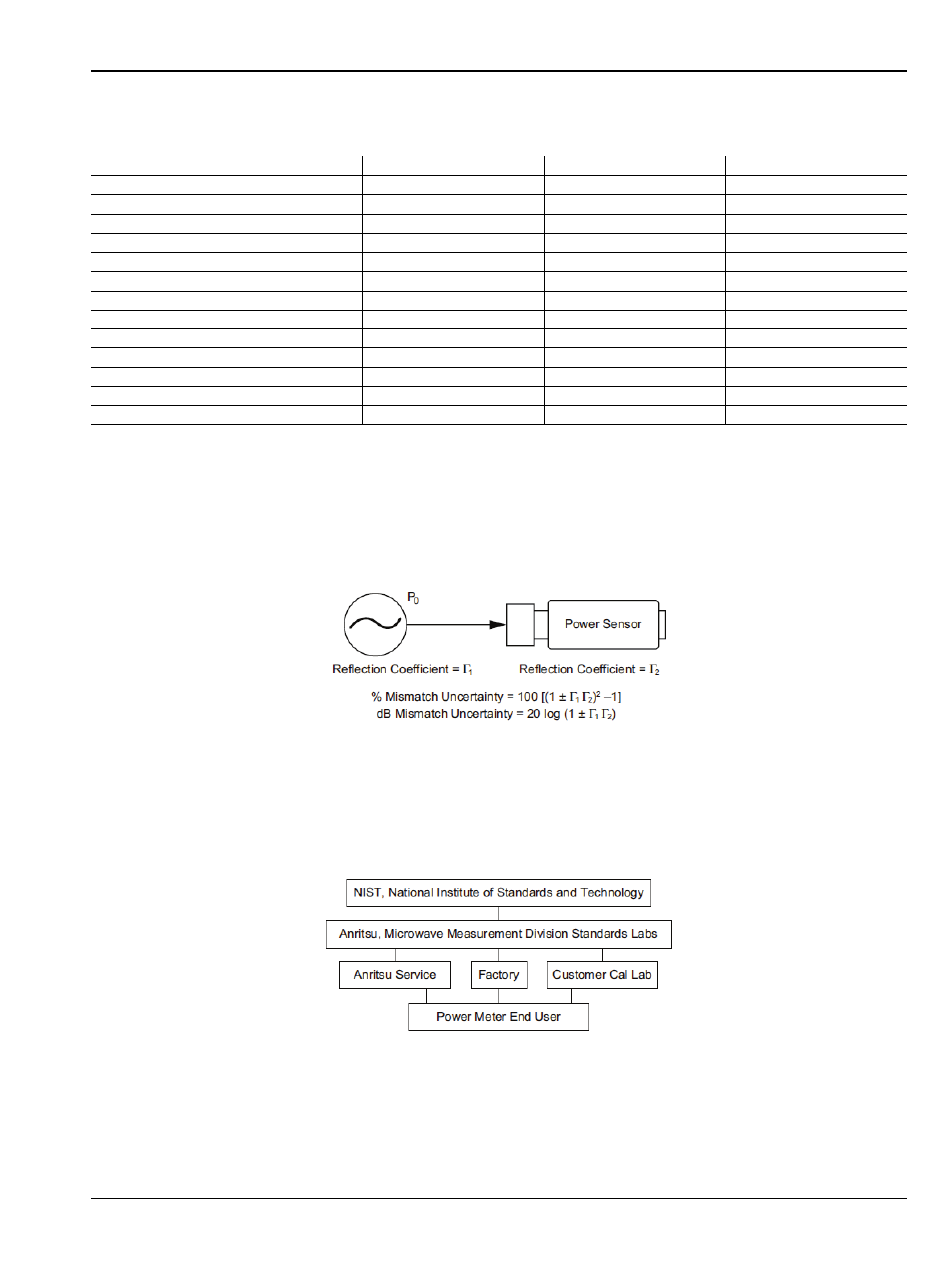
ML2430A, ML2480B, ML2490A
Power Sensor Specifications
ML2430A, ML2480B, ML2490A TDS
PN: 11410-00423 Rev. H
9
Measurement Accuracy
Power measurement accuracy can be split into several parts. The table below shows how the measurement uncertainty is composed for several
power sensors. The source is presumed to be a 16 GHz, 12.0 dBm signal with a source SWR of 1.5:1.
The uncertainties can be calculated as an RSS term as each parameter is independent. Alternatively they can be added together for a worst-case
analysis.
The Instrumentation accuracy of 0.5 % is a very small component of the overall uncertainty budget and describes the linear voltage
measurement accuracy of the power meter.
Sensor linearity describes the relative response over the dynamic range of the sensor, and is included when the sensor is measuring power
levels relative to the 0 dBm calibrator reference level. Temperature linearity is included when operating the sensor at other than room
temperature.
Noise, Zero Set and Drift are all measured on the lowest power range of the power sensor. Different types of power sensors have different
noise characteristics. Noise can be reduced by averaging.
Mismatch uncertainty is typically the largest component of the uncertainty budget – caused by the different impedances of the device under
test and the sensor. To help resolve this issue, the sensor has been designed to have a good return loss over a wide frequency range, typically
achieving significantly better results than the specification. In many cases the major contributing factor is the match of the source under test.
The source match of the device under test can be improved by the use of precision attenuators with good return loss or by the use of external
levelling with a high directivity coupler or splitter.
Connector damage has significant accuracy and repeat- ability effects, and is also the most common cause of sensor damage – although it is
frequently undetected. Every MA2400A/D Series includes a hex nut connection for application of a calibrated torque wrench. Torque wrenches
assure compliance with the quality requirement and result in more consistent measurements.
Sensor calibration factor uncertainty identifies the accuracy of the sensor’s calibration relative to a recognized standard for absolute power
level. Sensor calibration factor uncertainty is included in accuracy calculations for any absolute power measurement (in dBm or Watts) and for
relative power measurements if the signals are different frequencies.
Reference power uncertainty specifies the maximum possible output drift of the power meter’s 50 MHz, 0.0 dBm power reference between
calibration intervals. Reference power uncertainty and reference to sensor mismatch uncertainty do not generally impact relative power
measurements. See the Anritsu website
) for more information and tool to calculate measurement uncertainties.
MA2440D
MA2491A
MA2470D
Instrumentation Accuracy
0.50 %
0.50 %
0.50 %
Sensor Linearity
1.80 %
3.50 %
1.80 %
Noise, 512 Avg.
0.00 %
0.00 %
0.00 %
Zero Set and Drift
0.00 %
0.00 %
0.00 %
Mismatch Uncertainty
3.84 %
4.49 %
4.49 %
Sensor Cal Factor Uncertainty
0.79 %
1.59 %
0.84 %
Reference Power Uncertainty
1.20 %
1.20 %
1.20 %
Reference to Sensor Mismatch Uncertainty
0.23 %
0.31 %
0.23 %
Temperature Linearity
1.00 %
1.00 %
1.00 %
RSS, Room Temp
4.51 %
6.06 %
5.09 %
Sum of Uncertainties, Room Temp
8.36 %
11.59 %
9.06 %
RSS
4.62 %
6.14 %
5.18 %
Sum of Uncertainties
9.36 %
12.59 %
10.06 %
Mismatch is easily calculated in either dB or percentage terms from the source’s and sensor’s respective reflection coefficients.
ML2400A Series is NIST traceable for more accurate, dependable measurements.