Gas valves, Checking the input – John Wood Commercial Atmospheric Vent - AJWSM User Manual
Page 27
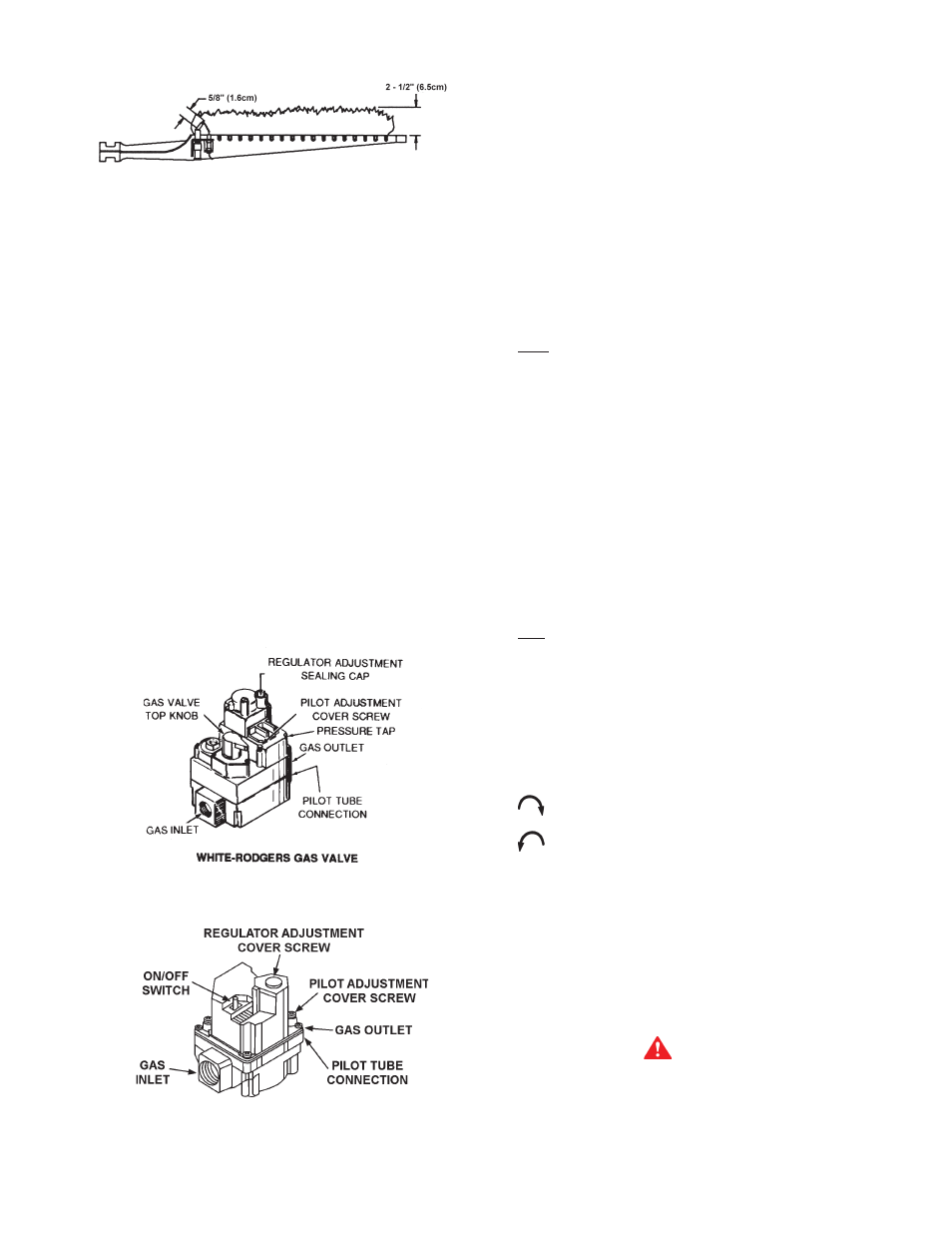
27
TYPICAL PILOT AND MAIN BURNER FLAMES
FIGURE 16
If the preceding burner characteristics are not evident, check
for accumulation of lint or other foreign material that restricts or
other foreign material that restricts or blocks the air openings to
the burner or heater.
NOTE: Cleaning of main burners.
1. Remove main burners from unit.
2. Check that burner venturi and ports are free of foreign
matter.
3. Clean burners with bristle brush and/or vacuum cleaner — DO
NOT distort burner ports or pilot location.
4. Reinstall burners in unit. Make sure front and rear of burners
are installed correctly in burner support brackets.
Also check for good flow of combustion and ventilating air to the
unit. Maintain a clear area around the heater at all times.
GAS VALVES
Figure 17 shows the two types of combination gas control valves
used on these heaters.
LP VALVE
NATURAL VALVE
FIGURE 17
If the gas valve becomes defective, repairs should not be
attempted. A new valve should be installed in place of the
defective one.
CHECKING THE INPUT
For appliance installation locations with elevations above 2000
feet (610 m), refer to HIGH ALTITUDE INSTALLATIONS section
of this manual for input reduction procedure.
1. Attach a pressure gauge or a manometer to the gauge port and
refer to Table 5, for correct manifold pressure.
2. Use this formula to “clock” the meter. Be sure that other gas
consuming appliances are not operating during this interval.
3600 X H = Btuh
T
T = Time in seconds to burn one cubic foot of gas.
H = Btu’s per cubic foot of gas.
Btuh = Actual heater input.
Example: (Using BTRC-199 heater)
T = 15.8 seconds
H = 1050 Btu
Btuh = ?
19.0 X 1050 = 199,000 Btuh (70.3 Kwh) (Compare with
15.9 heater model and rating)
Should it be necessary to adjust the gas pressure to the burners
to obtain the full input rate, the steps below should be followed:
3. Remove the regulator adjustment sealing cap, fig. 17, and
adjust the pressure by turning the adjusting screw with a
screwdriver.
Clockwise to increase gas pressure and input rate.
Counterclockwise to decrease gas pressure and input
rate.
4. “Clock” the meter as in step 2 above.
5. Repeat steps 3 and 4 until the specified input rate is achieved.
6. Turn the gas control knob to PILOT. Remove the pressure
gauge and replace the sealing cap and the allen wrench set
screw in the pressure tap opening.
WARNING
UNDER NO CIRCUMSTANCES SHOULD THE GAS INPUT
EXCEED THE INPUT SHOWN ON THE HEATER MODEL AND
RATING PLATE. OVERFIRING COULD RESULT IN DAMAGE
OR SOOTING OF THE HEATER.
When the heater is operating at full capacity, or full gas input, it
should consume 1 cu. ft. of gas in time indicated on Table 6.
CREATED BY NEEVIA DOCUSTAMP TRIAL VERSION (WWW.NEEVIA.COM)
CREATED BY NEEVIA DOCUSTAMP TRIAL VERSION (WWW.NEEVIA.COM)