Hot water sanitization recommendations – GE P&W Spiral Wound Membranes - Duratherm EXL Series User Manual
Page 2
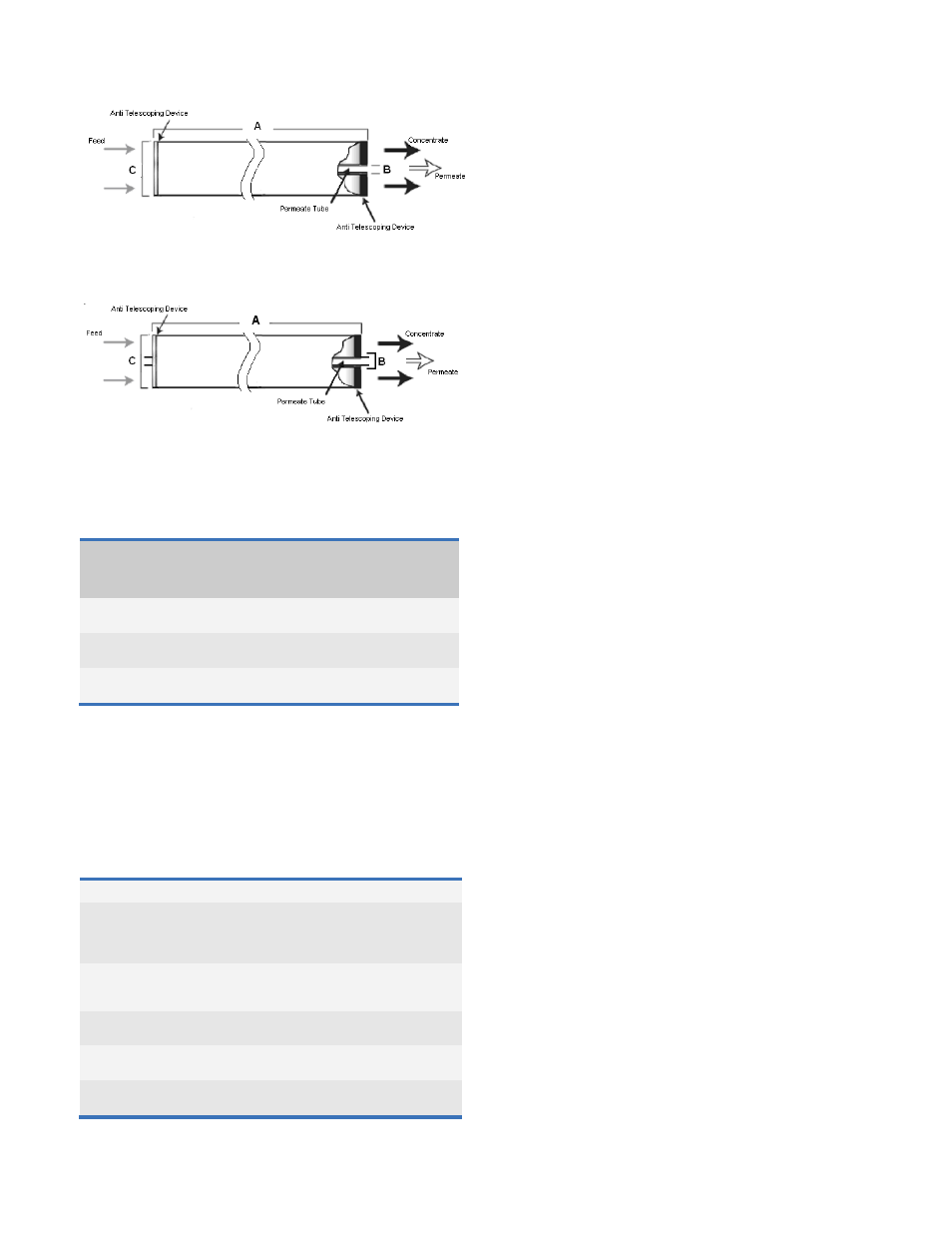
Figure 1A: Element Dimensions Diagram – Female
Figure 1B: Element Dimensions Diagram – Male
Table 3: Dimensions and Weight
Model²
Dimensions, inches (cm)
Boxed
A
B
1
C
3
Weight
lbs (kg)
XX 2540
40.0
(101.6)
0.75
(1.91)
2.43
(6.17)
4
(1.8)
XX 4040
40.0
(101.6)
0.625
(1.59)
3.9
(9.9)
9
(4.1)
XX 8040
40.0
(101.6)
1.125
(2.86)
7.9
(20.1)
29
(13.2)
1
Internal diameter.
² These elements are dried then bagged before shipping.
3
The element diameter (dimension C) is designed for optimum performance in GE
pressure vessels. Others pressure vessel dimension and tolerance may result in
excessive bypass and loss of capacity.
Table 4: Operating and CIP parameters
Do not exceed 20 GFD (33 LMH) or 2,000 Wagner units
under any circumstance.
Typical Operating Pressure
Figures 9 & 10
Maximum Operating Pressure 1,200 psi (8,273 kPa)
600 psi (4,137 kPa)
400 psi (2,758 kPa)
Hot Water Sanitizing
32 – 77°F (0 – 25°C)
78 – 122°F (26 – 50°C)
123 – 158°F (51 – 70°C)
158 – 194°F (70 – 90°C)
Maximum Temperature
Continuous Operation: 177°F (70°C)
Clean-In-Place (CIP): 104°F (40°C)
Hot Water Sanitizing: 194°F (90°C)
pH range
Continuous Operation: 3 – 9
clean-In- Place (CIP): 2 – 10.5
Chlorine Tolerance
500 ppm hours
dechlorination recommended
Feedwater
NTU < 1
SDI < 5
Hot Water Sanitization
Recommendations
For optimal performance, Duratherm EXL elements
should always be cleaned using approved CIP pro-
cedures and flushed with fouling free water before
the sanitization process. Feed pressure during sani-
tization should not exceed 40psi (275kPa) and the
crossflow should not incur a pressure drop greater
than 2psi (14kPa) per element. Heating rate to sani-
tizing temperature and cool down should not be
faster than 5°C (9ºF)/minute. Maximum sanitization
temperature is 90°C (194ºF).
Loss of permeate flow after repeated
90ºC (194ºF) sanitization cycles
It is almost impossible to exactly predict the per-
centage of permeate flow rate lost from the high
temperature sanitations, which among other fac-
tors depends on:
• The rate of temperature increase and decrease.
• The presence of other species like organics, ion-
ic and metallic compounds that could locally
decrease or increase the temperature at the
surface of the membrane.
• The feed flow rate and specifically the heat
transfer rate to the membrane surface.
• The thickness and geometry of the feed spacer
used.
At optimum conditions measured in controlled envi-
ronment with deionized water, between 30% and
50% of the original permeate flow rate was lost be-
fore the element performance had stabilized after
repeated heat treatments (over 90% of this flow
reduction occurred during the first heat treatment).
With the loss of permeate flow rate, the salt rejec-
tion increases. The rate of cooling and heating was
not more than 5°C (9ºF) per minute, and the differ-
ential pressure drop per element did not exceed 2
psi.
Pilot testing based on the criteria noted above will
give the best operating parameters for any specific
application.
Page 2
Fact Sheet