Installation and service manual – Lochinvar 399 User Manual
Page 47
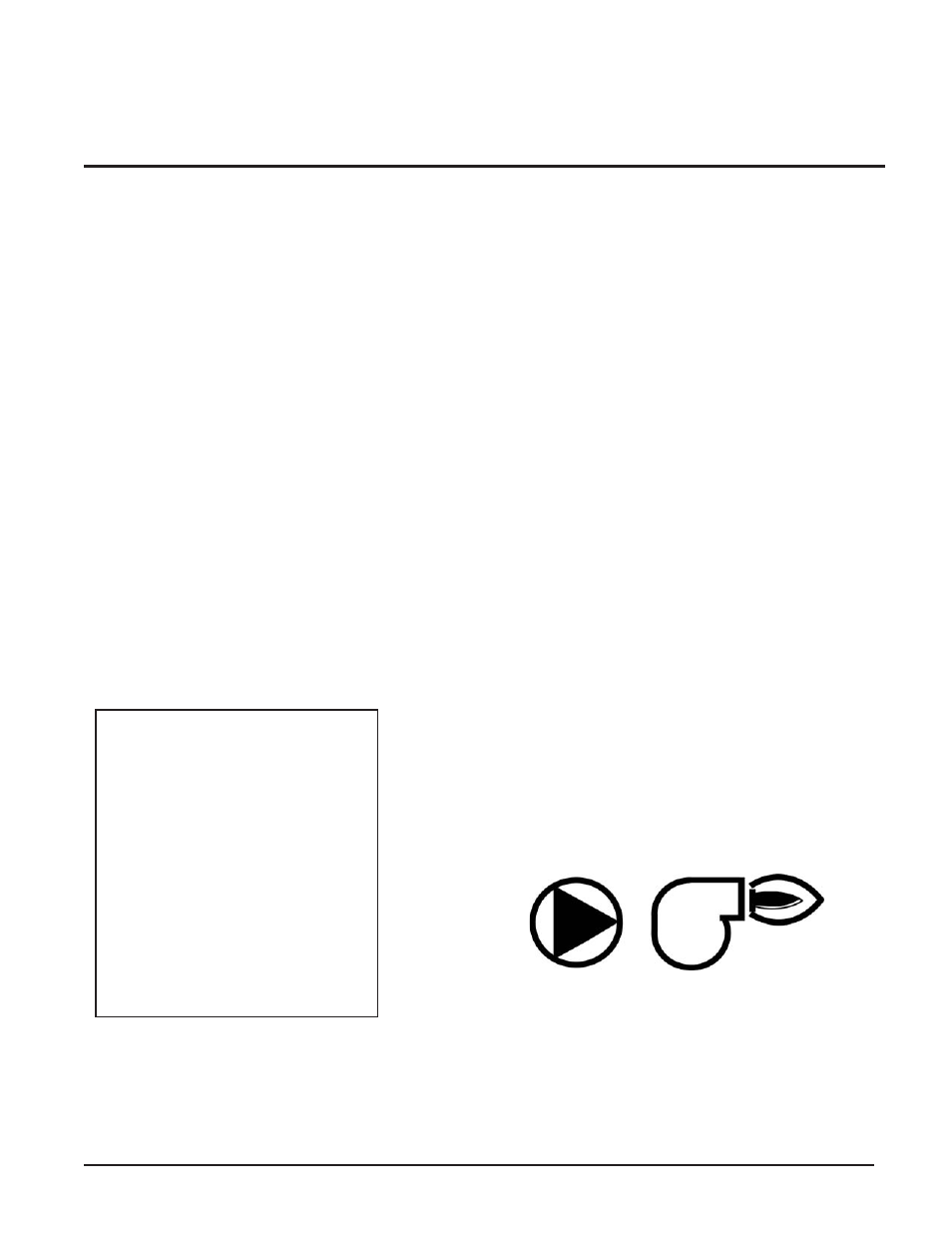
Installation and
Service Manual
47
System Sensor: This is used for boiler applications. This sensor
will control the water temperature within the building loop.
Staging Logic
There are two different types of staging logic used in the
temperature control; Proportional (step) Staging Logic and
PID Staging Logic. The staging logic used depends upon what
mode the control is running under.
Proportional (Step) Staging Logic
The proportional method of staging is based on manually
adjusted settings which determine when the next stage is required
to fire. This method is used on Mode 1 for set point operation
(with no outdoor sensor) and Mode 2 for water heating. The
adjustable settings are:
Set Point TARGET 1, 2, 3, or 4: Staging set point target for each
stage. Typically, users set the four different stages a few degrees
apart to allow segments of the heater to come on as the
temperature drops.
DIFF 1, 2, 3, or 4: Staging differential for each stage.
STG DLY: Interstage delay to turn on between stage 1 and 2 and
between stage 3 and 4.
How It Works
A stage will turn on once the temperature drops to its Set point
TARGET minus DIFF. The stage will turn off once the
temperature rises to its Set point TARGET.
There is a time delay (STG DLY) that applies in the staging on
sequence between stage 1 and 2 and between stage 3 and 4. For
example, in order for stage 2 to turn on, the temperature must
drop to Set point TARGET 2 minus DIFF 2, and the STG DLY
must elapse. The STG DLY begins once stage 1 turns on. This
operation applies between stage 3 and 4 as well.
Stage 1 and 2 are independent of stage 3 and 4. Stage 2 cannot
fire before stage 1 and stage 4 cannot fire before stage 3.
PID Staging Logic
(Outdoor Air Mode 1 Only)
This method is used on Mode 1 for outdoor reset with reset
override operation (using the outside air temperature sensor).
The PID method of staging allows the control to decide the
most effective way to operate the stages to maintain an
accurate temperature and minimize short cycling.
The control continuously monitors the actual supply
temperature and compares it to the target temperature. The
amount of error (proportional), the time the error has been
present (integral), and the rate of change (derivative),
determine if an additional stage is required to turn on or off.
The control automatically calculates the inter-stage differential
as well as the delays between stages turning on or off.
OUTDR START, OUTDR DSGN, BOIL START and BOIL
DSGN need to be field set based on installation design criteria to
establish the reset curve. Verify that the WWSD is set to the
desired value. Adjust BOIL MAX and BOIL MIN to appropriate
values for the application.
Note: BOIL MIN should not be less than a setting which will
ensure the return water temperature to the unit being 140°F
minimum.
BOIL MASS should only need adjustment if changes in the
interstage delay are necessary.
Graphic Symbols
The screen will display two graphic symbols. One is a circle
with a triangle inside and the other is a graphic representation
of a blower (see FIG. 50). The circle with a triangle inside
represents the pump. When this symbol is present, the pump is
operating. When the blower symbol is present, the controller is
calling for heat.
FIG. 50 Graphic Symbols
Programming For Mode 1, Boiler
Operation
Mode 1 is for boiler operation. Under Mode 1, there are two
sublevels of operation.
1. Operate off of set point.
2. Operate off of outdoor air reset curve.
EXAMPLE:
Using stage one of the control as an
example, the corresponding load would
be energized and de-energized at the
following temperatures based on the
programmed settings.
Settings
Set Point: 160°F (71°C)
Differential: 8°F (5°C)
Output Energized
Stage One: Energized at 152°F (67°C)
Output De-energized
Stage One: De-energized at 160°F (71°C)