Supplementary information 8.1 application example, 2 uss status codes – Siemens G85139 User Manual
Page 37
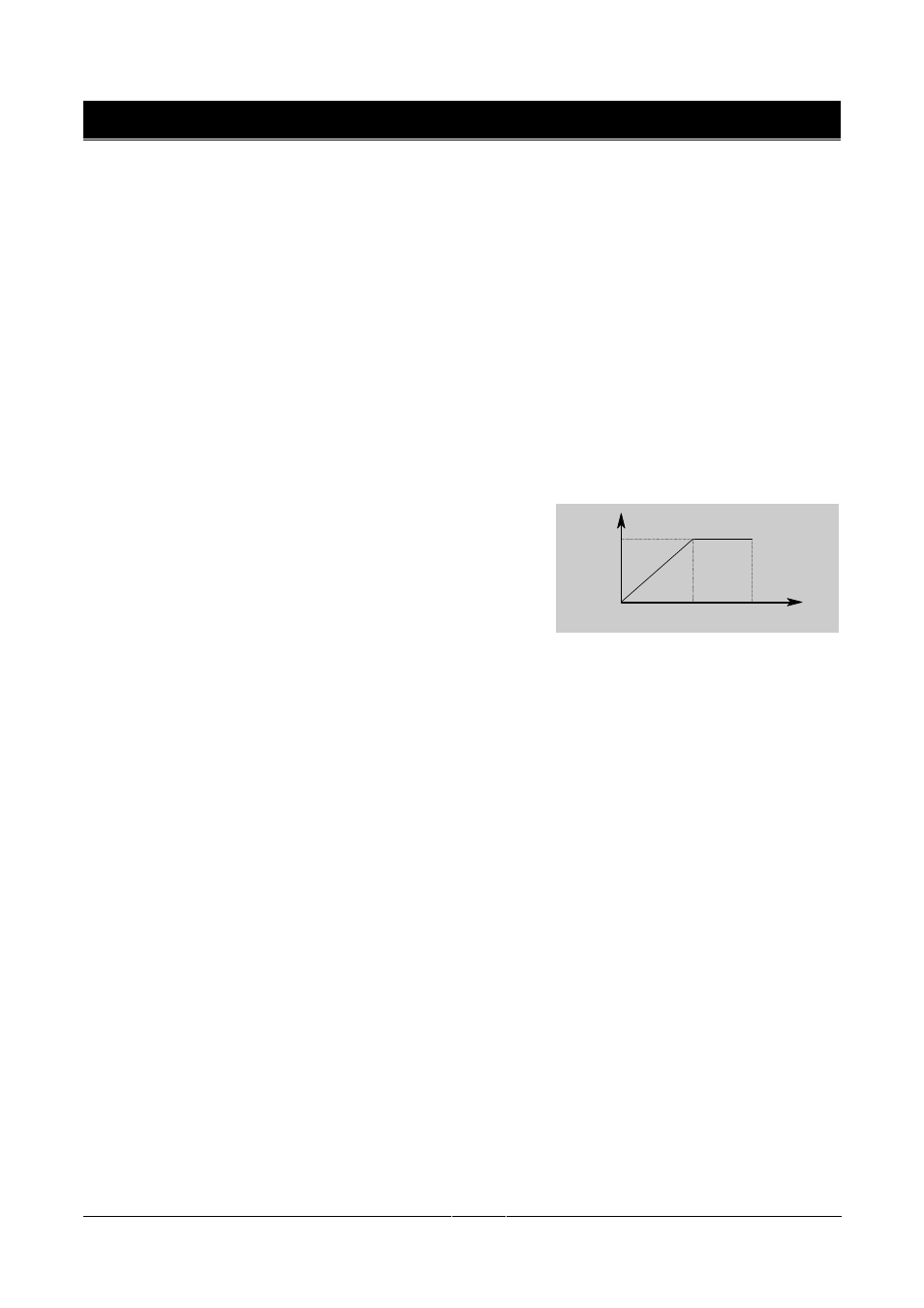
8.
SUPPLEMENTARY INFORMATION
English
© Siemens plc 1997
G85139-H1750-U049-B
37
26/09/97
8. SUPPLEMENTARY INFORMATION
8.1 Application Example
Setup procedure for a simple application
Motor:
220 V
1.5 kW output power
Application requirements:
Setpoint adjustable via potentiometer 0 - 50 Hz
Ramp up from 0 to 50 Hz in 15 seconds
Ramp down from 50 to 0 Hz in 20 seconds
Inverter used:
MM150 (6SE9216-8BB40)
Settings:
P009 = 2 (all parameters can be altered)
P081 - P085 = values given on motor rating plate
P006 = 1 (analogue input)
P002 = 15 (ramp up time)
P003 = 20 (ramp down time)
This application is now to be modified as follows:
Operation of motor up to 75 Hz
(voltage/frequency curve is linear up to 50 Hz).
Motor potentiometer setpoint in addition to
analogue setpoint .
Use of analogue setpoint at maximum 10 Hz.
Ramp times to remain the same.
Parameter adjustments:
P009 = 2 (all parameters can be altered)
P013 = 75 (maximum motor frequency in Hz)
P006 = 2 (setpoint via motor potentiometer or fixed setpoint)
P024 = 1 (analogue setpoint is added)
P022 = 10 (maximum analogue setpoint at 10 V = 10 Hz)
8.2 USS Status Codes
The following list gives the meaning of status codes displayed on the front panel of the inverter when the
serial link is in use and parameter P001 is set to 006:
001
Message OK
002
Slave address received
100
Invalid start character
101
Timeout
102
Checksum error
103
Incorrect message length
104
Parity fail
Notes
(1)
The display flashes whenever a byte is received, thus giving a basic indication that a serial link
connection is established.
(2)
If ‘100’ flashes on the display continuously, this usually indicates a bus termination fault.
i.e.
V
f (Hz)
220
50
75