Installation, 10 lpg conversion - all models – Glow-worm Ultracom hxi User Manual
Page 26
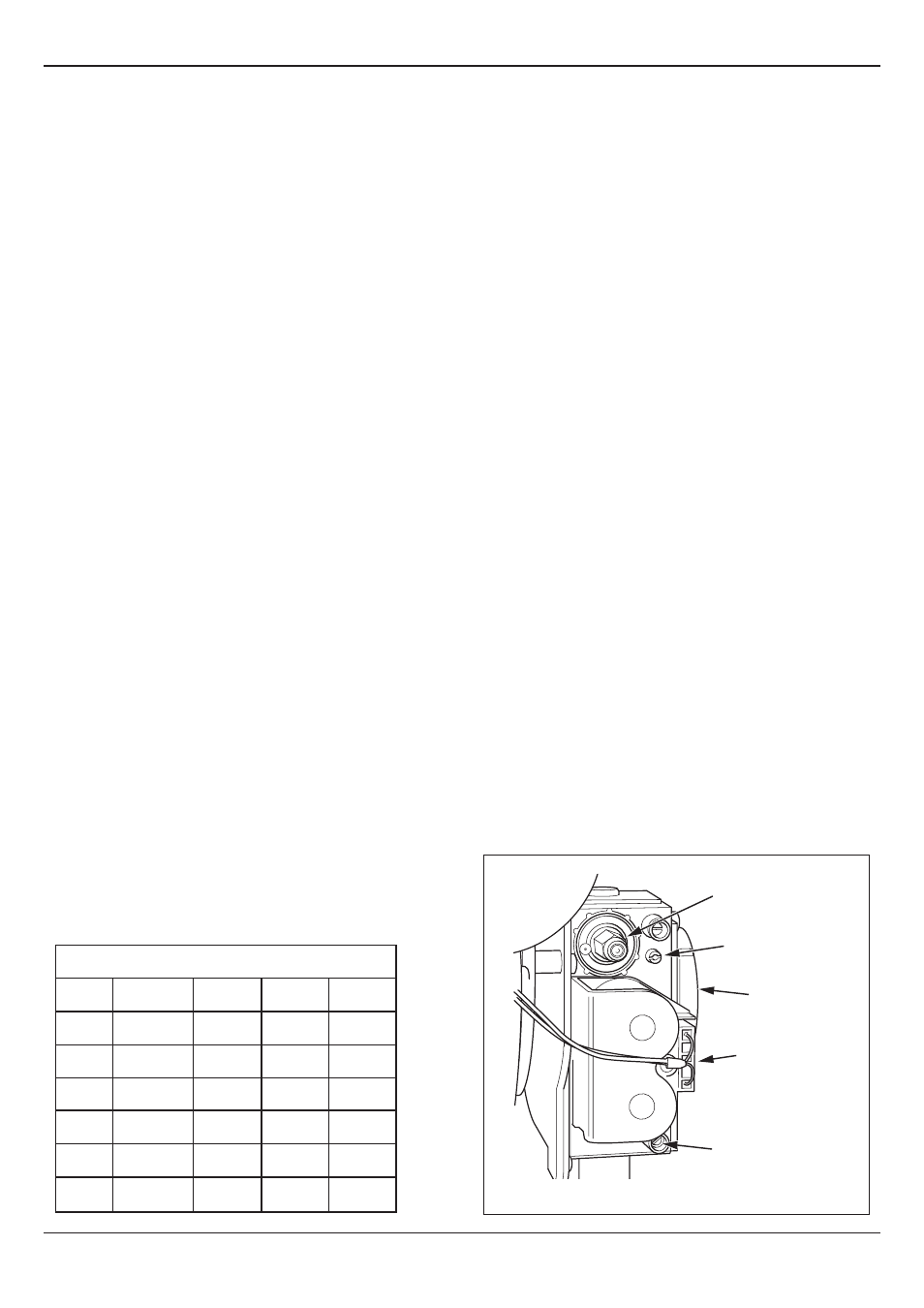
0020107233_00 - 06/11 - Glow-worm
INSTALLATION
- 26 -
G31 BURNER % CO
2
CHECK
(case on)
SETTING
(case off)
10.1
10.1
10.1
10.1
10.5
9.8
+ 0.0
- 0.8
+ 0.5
- 0.5
+ 0.0
- 1.0
+ 0.3
- 0.8
+ 0.3
- 0.8
+ 0.2
- 0.8
Throttle
TURNS
5
5¼
5
5¼
5½
8
CO/CO2
0.004
0.004
0.004
0.004
0.004
0.004
9.2 to 10.2
9.8 to 10.8
9.2 to 10.2
9.2 to 10.2
10.0 to 11.0
9.2 to 10.2
MODEL
12hxi
15hxi
18hxi
24hxi
30hxi
38hxi
GAS VALVE
OFFSET
ADJUSTMENT
THROTTLE
ELECTRICAL
PLUG
PRESSURE
TEST POINT
13513
10.10 lPG ConVeRSIon - all models
As an option, a chargeable boiler performance and function
service can be provided by Glow-worm Service by calling
telephone No. 01773 828100.
noTe: Steps 10.1 and 10.3 will need to be completed before
the appliance can be converted.
This conversion should only be carried out by a
competent
person approved at the time by the Health and Safety
Executive.
During the conversion to Propane use of a suitable flue gas
analyser is necessary.
● The person carrying out a combustion measurement should
have been assessed as competent in the use of a flue gas
analyser and the interpretation of the results.
● The flue gas analyser used should be one meeting the re-
quirements of BS7927 or BS-EN50379-3 and be calibrated in
accordance with the analyser manufacturers’ requirements.
● Competence can be demonstrated by satisfactory
completion of the CPA1 ACS assessment, which covers
the use of electronic portable combustion gas analysers in
accordance with BS 7967, parts 1 to 4.
As an option a chargeable boiler only commissioning service
can be provided by Glow-worm Service by calling telephone
No. 01773 828100.
Tools required to make the conversion are a 2mm Allen key
and an electricians screwdriver.
Ensure that the appliance supply pressure = 37mbar.
(1) Access the gas valve.
(2) Refer to diagram 10.5 and turn the gas valve throttle fully
clockwise.
(3) Turn the throttle anti-clockwise by the number of turns
shown in the table.
(4) Ensure that the gas analyser is set to the correct fuel
setting - Propane.
(5) Attach combustion analyser to the combustion test point,
refer diagram 11.1.
IMPoRTanT: Remember to replace the cap on
completion of the test.
(6) Make sure that the external controls are calling for heat,
then turn the mains electrical supply and gas service
isolation valve on.
(7) Switch the boiler on. The boiler should fire automatically.
noTe: If the appliance does not light & goes to lockout
(F1) turn the throttle anti-clockwise a further turn and
press the reset button. The appliance will (after a short
delay) again attempt to fire. Repeat this procedure (up
to a total of 2 extra turns on the throttle screw) until
the appliance lights. Several ignition attempts may be
needed, to purge gas through the appliance, before a
successful ignition is achieved.
Diagram 10.5
(8) Check and adjust the burner %CO
2
at maximum rate.
Press the “reset” button on the controls fascia, release
and immediately press and hold in the “+” button. After
approximately 5 seconds “Hi” will be displayed. Pressing
the mode button when “Hi” is selected will force the boiler
to maximum rate, the display will flash between “Hi” and
the “default display” this will indicate the boiler has been
forced to maximum.
(9) If necessary, adjust the burner % CO
2
to the value shown
in the “SETTING” column of the table, by turning the
throttle screw (anti-clockwise to increase), see diagram
10.5 no more than 1/8 of a turn, waiting a minute to allow
for the appliance to stabilise before checking or making
further adjustments.
(10) Exit the check sequences press the “mode” and “+”
buttons simultaneously, this will reset the boiler to the
default display.
(11) Check the burner % CO
2
, at minimum rate, to the value
shown in the “SETTING” column of the table.
(12) If adjustment is required, press the “reset” button on the
controls fascia, release and immediately press and hold
in the “+” button. After approximately 5 seconds “Hi” will
be displayed. Pressing the “+” or “-” buttons will cycle
between “Hi” and “Lo”. Pressing the mode button when
“Lo” is selected will force the boiler to minimum rate, the
display will flash between “Lo” and the “default display”
this will indicate the boiler has been forced to minimum.
(13) Adjustment of the %CO
2
is very coarse so carefully
adjust the %CO
2
to the value shown in the “SETTING”
column of the table with the offset adjustment, see
diagram 10.5 and %CO
2
Table (Rotate clockwise to
increase).
(14) To exit the function press the “mode” and “+” buttons
simultaneously, this will reset the boiler to the default
display.
(15) Repeat (8) and check CO
2
at maximum rate - adjust if
necessary. Check that the CO/CO2 ratio is less than the
value in the table below.
(16) Remove analyser probe from the test point and replace
the cap. Refit the control panel.
(17)
IMPoRTanT: fit the lPG conversion label supplied
in the documentation pack to the inner front panel
alongside the data label. Refit the inner door and
outer door.
(18) Continue commissioning from 10.5.
13868