Technical information 19.3 – HEIDENHAIN TNC 640 (34059x-05) ISO programming User Manual
Page 629
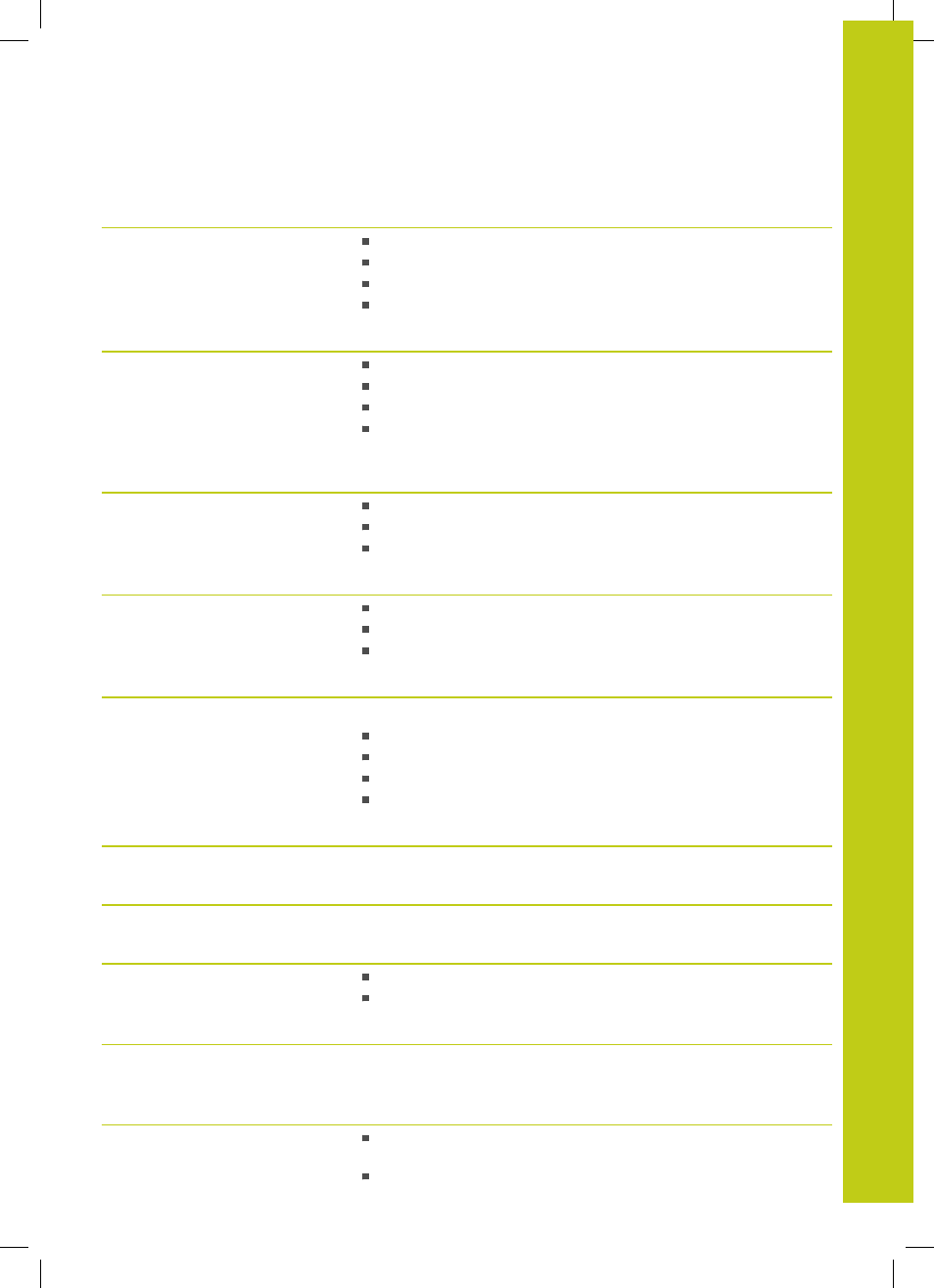
Technical Information
19.3
19
TNC 640 | User's ManualDIN/ISO Programming | 1/2015
629
Dynamic Collision Monitoring – DCM
(Option #40)
Dynamic Collision Monitoring
The machine manufacturer defines objects to be monitored
Warning in Manual operation
Program interrupt in Automatic operation
Includes monitoring of 5-axis movements
DXF Converter
(Option #42)
DXF converter
Supported DXF format: AC1009 (AutoCAD R12)
Adoption of contours and point patterns
Simple and convenient specification of reference points
Select graphical features of contour sections from conversational
programs
Adaptive Feed Control – AFC
(Option #45)
Adaptive Feed Control
Recording the actual spindle power by means of a teach-in cut
Defining the limits of automatic feed rate control
Fully automatic feed control during program run
KinematicsOpt
(Option #48)
Optimizing the machine
kinematics
Backup/restore active kinematics
Test active kinematics
Optimize active kinematics
Mill-Turning
(Option #50)
Milling and turning modes
Functions:
Switching between Milling/Turning mode of operation
Constant surface speed
Tool-tip radius compensation
Turning cycles
Extended Tool Management
(Option #93)
Extended tool management
Python-based
Spindle Synchronism
(Option #131)
Spindle synchronization
Synchronization of milling spindle and turning spindle
Remote Desktop Manager
(Option #133)
Remote operation of external
computer units
Windows on a separate computer unit
Incorporated in the TNC interface
Synchronizing Functions
(Option #135)
Synchronization functions
Real Time Coupling – RTC:
Coupling of axes
Cross Talk Compensation – CTC
(Option #141)
Compensation of axis couplings
Determination of dynamically caused position deviation through axis
acceleration
Compensation of TCP (
T
ool
C
enter
P
oint)