TE Technology TC-720 User Manual
Technology, inc
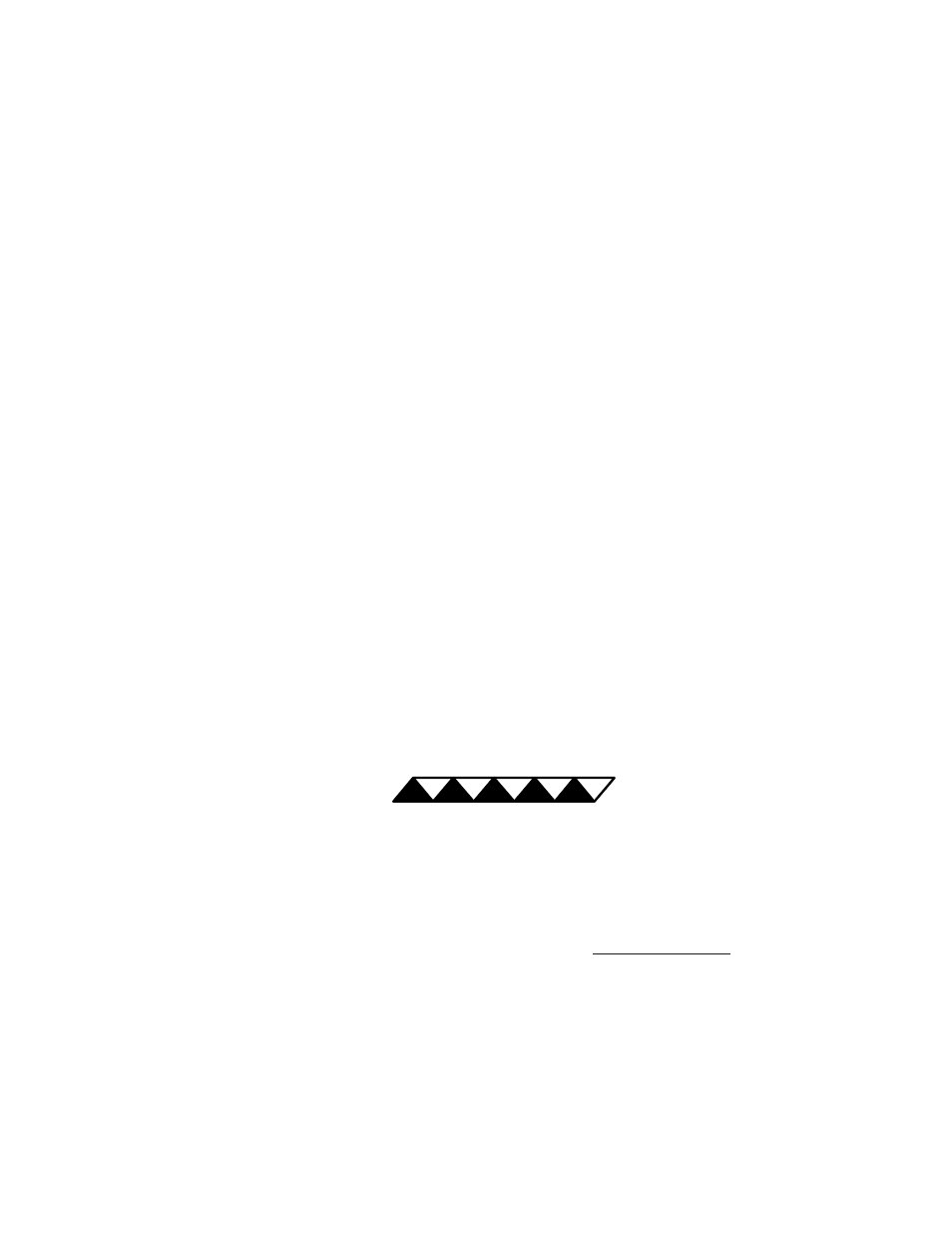
Instruction Manual
for
Model TC-720
and
Model TC-720 OEM
Thermoelectric Cooler
Temperature Controller
August 11, 2014
Drawing #5252 Rev. A
1590 Keane Drive
Phone: (231) 929-3966
Traverse City, MI 49696 USA
Fax: (231) 929-4163
www.tetech.com
e-mail:
All Materials Copyright © 2013, 2014, TE Technology, Inc.
TE
TECHNOLOGY, INC.
®
This manual is related to the following products:
Table of contents
Document Outline
- This manual must be read and followed carefully before installation and operation. All warnings in this Instruction Manual apply to both the TC-720 and TC-720 OEM versions of the controller. Where “TC-720” is referenced, it is used generically and i...
- THE LATEST REVISION OF THIS MANUAL IS AVAILABLE AT www.tetech.com. Verify that you are using the latest revision available.
- Do not use in an explosive or potentially explosive environment.
- The TC-720 is designed specifically for its intended purpose of providing temperature control of TE Technology’s thermoelectric devices only. The temperature controller is intended for light industrial, laboratory, or similar use; it is not intended...
- Do not use the TC-720 to control capacitive or inductive loads as this could damage and/or overheat the controller. Examples of capacitive or inductive loads include but are not limited to motors and solenoids.
- Do not use if the controller has been damaged.
- Only qualified technicians should install this controller.
- Do not allow the electrical connections or components on the printed circuit board, including those on the reverse side of the JP3, JP5, JP6 and JP7 connectors, to touch any electrically conductive surfaces.
- Do not operate in an environment where the controller could come in contact with condensation, water, metal shavings, dirt or other contaminants, or electrically conductive materials.
- Use ESD (Electro Static Discharge) protection when installing or handling the controller.
- Do not touch any of the electrical connections or components of the TC-720 while the controller is energized. Doing so can disrupt the function of the controller.
- The printed circuit board underneath JP7 and exposed components on the printed circuit board could exceed 70 C under normal operation. Use caution! Protect against accidental contact with hot surfaces.
- Each power input that is used must be fused separately. Alternately, a power supply with integral over current protection can be used if it is appropriately sized for protecting the controller/TE device.
- Thermoelectric devices are capable of developing potentially hazardous temperatures and/or other potentially hazardous conditions. Read and follow the instructions in TE Technology’s Thermoelectric Cooling Assembly (TCA) Instruction manual before u...
- License Agreement
- Features
- 1.0 Setup
- 1.1 Attach the temperature sensor at an appropriate temperature-control location. Locating the sensor at the cold side of the TE device provides better control stability than locating it at the object, liquid, or air that is to be cooled/heated. How...
- If you are using a secondary temperature sensor, attach it to the appropriate location as well. The secondary sensor, for example, can be used to monitor the hot side of the TE device.
- NOTE: When possible, it is recommended that at least 50 mm of the sensor’s wire be thermally connected to the surface as shown in the example below. This can be accomplished by taping the sensor wires with aluminum tape, for example. If this is not d...
- In addition, the sensor itself needs to have a good thermal connection to the temperature control location. Thermal grease, such as the TP-1 from TE Technology, or other suitable thermal interface material should be applied to the interface of the sen...
- 1.2 To connect the sensor leads to the controller (as well as other wire connections), you will first need to open up the controller. Remove the four screws from the top of the lid. Lift the lid from the controller, and set it face down next the box.
- Push the primary sensor wires through the two right-most holes in the rubber face plate located at the front side of the box. The secondary sensor wires would go through the next two holes as applicable. You may need to use a sharp tool to expand the ...
- Connect the primary sensor wire leads to JP2-1 (+) and JP2-2 (-).
- Connect the secondary sensor wire leads (if applicable) to JP2-4 (+) and JP2-3 (-).
- If you are using the MP-3193 or other thermistor, the polarity will not matter. See the controller hookup drawings below for further reference.
- If you are using a thermistor for temperature sensing, the wire leads of the thermistor can be lengthened if necessary without affecting accuracy by any significant amount. However, the use of twisted pair and/or shielded wire may be required to reduc...
- The TC-720 is pre-programmed to use the 15 kΩ thermistor curve as the default. The MP-3193 that comes standard with the controller is of this type. Other thermistor styles directly compatible with the controller besides the MP-3193 are available as op...
- If you want to use a thermistor that has a different resistance-temperature curve from the pre-programmed thermistor curves, or if you intend to use a different type of sensor altogether, the controller should be programmed accordingly. See “Programmi...
- 1.3 The TC-720 can be used with either one or two separate DC power supplies for bipolar control of one TE device. If the maximum TE device operating voltage is less than 12 V, then two power supplies must be used with the controller. If the TE device...
- The controller can also be set up to provide linear control output when used with a power supply whose output can be controlled with a 0 to 10 V signal (the maximum output voltage can be reduced as necessary). The power supply can then provide a power...
- When using one power supply for powering the controller and the TE device together, the power supply input voltage is passed directly through the controller to the TE device during the “ON” pulse. The power supply must provide a voltage that is ≥12 ...
- When using two power supplies, the input power supply for the controller itself must be ≥12 V but ≤36 V and be capable of providing at least 150 mA of current. The power supply input voltage for the TE device can be >0 V but ≤36 V and be capable of...
- The total maximum allowable current through the controller is 20 A (combined load and alarm current). The maximum allowable current draw for the TE device must therefore be less than 20 A depending on if and how much current is used by devices conne...
- The controller does not have an internal fuse to limit current. Therefore, an external fuse, appropriately sized for protecting the controller/TE device, should be connected between the power supply and the controller to prevent damage to the contro...
- When making a cooling system from a single TE module, the maximum operating voltage for that system is usually no more than 75% of the rated Vmax of the TE module. The 75% rule is based on the TE module being thermally connected to a “good” heat sin...
- Power supply and TE Device wire leads should be kept to a length of one meter or less and of sufficient wire size to reduce electrical losses in the wire and the likelihood of generating unwanted electromagnetic interference. However, see also warni...
- Use protection devices to prevent hazardous conditions and/or damage to the TE device and other related equipment. Protection devices must operate independently of the temperature controller circuitry. Protection devices should be placed at all po...
- Make sure the power supply is NOT energized while making electrical connections to the controller.
- The output voltage of the TE Power Supply should not exceed the maximum desired input voltage of the thermoelectric device, or the rated input voltage of the cooling assembly.
- Connect the DC voltage power supply (output voltage: ≥12 V but ≤36 V) to the controller as follows:
- a) Connect wire between Positive (+) terminal of the power supply and JP7-4.
- b) Connect wire between Negative (-) terminal of the power supply and JP7-3.
- c) See Section 1.4 for further information on connecting the TE device.
- Connections, One Power Supply Operation
- Make sure the power supplies are NOT energized while making electrical connections to the controller.
- The output voltage of the TE Device Power Supply should not exceed the maximum desired input voltage of the thermoelectric device, or the rated input voltage of the cooling assembly.
- a) Connect the DC voltage power supply (for powering the controller electronics) to the controller (≥12 V and ≤36 V, 150 mA minimum):
- i) Connect wire between Positive (+) terminal of the power supply and JP2-9.
- ii) Connect wire between Negative (-) terminal of the power supply and JP2-7.
- b) Connect the DC voltage power supply (for powering the TE device) to the controller (>0 V but ≤36 V):
- i) Connect wire between Positive (+) terminal of the power supply and JP7-4.
- ii) Connect wire between Negative (-) terminal of the power supply and JP7-3.
- c) See Section 1.4 for further information on connecting the TE device.
- Connections, Two Power Supply Operation
- Make sure the power supplies are NOT energized while making electrical connections to the controller.
- The maximum output voltage of the TE Device Programmable Power Supply should not exceed the maximum desired input voltage of the thermoelectric device, or the rated input voltage of the cooling assembly.
- a) Connect a constant-voltage DC power supply for powering the controller electronics to the controller (≥12 V and ≤36 V, 150 mA minimum):
- i) Connect wire between Positive (+) terminal of the power supply and JP2-9.
- ii) Connect wire between Negative (-) terminal of the power supply and JP2-7.
- b) Connect the remote control voltage points of the programmable power supply to the analog output signal of the controller; consult the manufacturer’s power supply manual for remote control setup:
- i) Connect wire between Positive (+) remote control terminal and JP2-5.
- ii) Connect wire between Negative (-) remote control terminal and JP2-7.
- iii) NOTE: This is a buffered output, however, depending on the power supply remote control input requirements an additional external voltage buffer might be required between the controller and the power supply.
- c) Connect the output terminals of the programmable power supply for powering the TE device to the controller:
- i) Connect wire between Positive (+) terminal of the power supply and JP7-4.
- ii) Connect wire between Negative (-) terminal of the power supply and JP7-3.
- d) See Section 1.4 for further information on connecting the TE device, and see SET MODE/ANALOG OUT for a description of how this control mode operates.
- NOTE: The controller does not have the internal circuitry to generate a high current analog output voltage from a fixed-voltage supply.
- Connections, Linear Control Operation (Analog Out Control Mode)
- 1.4 Connect the controller to the TE device as follows (see connection diagrams above for reference):
- a) Connect wire between Positive (+) terminal of the TE device and JP7-1. Connect wire between Negative (-) terminal of the TE device and JP7-2.
- b) If a TE Technology cooler is being used, remove jumpers from the terminal block as described below.
- TE Technology’s standard thermoelectric cooling assemblies (TCA) usually have at least one fan on the heat sink. The standard configuration has the thermoelectric modules and fan(s) wired to a terminal block with jumpers across the terminals so that...
- 1.5 Connect other applicable devices to the controller:
- a) Connect optional external alarm LED indicators to JP2-10 (ALARM2) and/or JP2-8 (ALARM1), assuming ALARM1 will not be configured for PWM fan control.
- b) Connect optional enable/disable switch between JP2-6 and JP2-7 (or other circuit ground location). The controller will need to be software programmed to enable this feature (described in Section 4). Once programmed, when the switch is closed (elect...
- Connections, Other Applicable Devices
- c) If you intend to use the controller to speed-control a fan rated for PWM control, connect the PWM speed-control wire as shown below through the rubber face plate, and connect to JP2-8. Be sure to consult the fan manufacturer for further details on ...
- The default configuration for JP2-8 is to serve as ALARM1 output. The controller will need to be software programmed (described in Section 4) for fan speed control rather than serving as ALARM1. ALARM2 may be configured to sense the temperature from t...
- Connections, Fan Speed Control
- (connections and components may vary depending on the fan being used)
- d) ALARM1 or ALARM2 outputs could also be configured to power on or off devices such pumps or fans. Each alarm can manage up to 2 A of current. However, the total current comprised of the current passing through the alarm outputs plus the current pass...
- 1.6 Turn on power supply to the controller and power supply to the TE device if applicable and set controller and tuning parameters as necessary, described in Section 2 and Section 3 or in Section 4 using the software. The factory default is set to h...
- NOTE: When not using a thermistor on the secondary sensor input, the ALARM 2 TEMPS must be set to OFF and/or ALARM 2 FUNCTION must be set to KEEP OUTPUT ON. The default setting for the controller is to assume that a secondary sensor is attached. If on...
- The keypad could reach a normal operating temperature of 70 C particularly if operating in a warm ambient temperature.
- Do not mount the controller to a surface which is exposed to a source of heat, such as from electronics, machinery, or solar radiation.
- Do not cover the controller with any object or otherwise restrict natural convection airflow around the controller. Doing so could cause the controller to overheat.
- Do not mount the controller to an insulating surface. Doing so could cause the controller to overheat.
- Do not operate the controller in such a manner as to cause the surface temperature of the case or internal temperature to exceed 70 C. Otherwise the controller might be damaged and there might be a risk of fire as a result.
- Do not allow the controller to be exposed to water (such as from dripping or leaking water lines or in which the controller is operating at or below the dew point temperature)
- Do not allow metallic dust/shavings to enter into the controller box.
- 2.0 DISPLAY AND MENU OPTIONS
- 2.1 Initialization screen
- 2.2 Primary screen
- In addition, if an alarm condition has caused the power output to be turned off, the words ALARM and OUT=0% will flash in alternating sequence in the place of the normal OUT=###% indicator.
- When not using a thermistor on the secondary sensor input, the ALARM 2 TEMPS must be turned OFF and/or ALARM 2 FUNCTION must be set to KEEP OUTPUT ON.
- 2.3 LED Indicators
- The lower left of the TC-720 contains an ALARM LED underneath the symbol. The LED will be green if there is no alarm condition or orange if there is an alarm condition.
- The USB LED underneath the symbol will be white if there is communication between the controller and a computer if connected by USB.
- 2.4 Parameters Menu
- When at the Primary Screen (shown below), depressing the MENU key allows the user to scroll through and adjust the various controller parameters.
- • Press the “MENU” button momentarily to select the parameter to be changed.
- • Press the Up/Down arrow keys to adjust the parameter value.
- • If there is more than one value for any given parameter the MENU key will scroll from the first value to the next value and then on to the next parameter.
- • Holding the Up/Down arrow keys will cause the value to increment faster.
- • The display will return to the primary screen after approximately eight seconds if no keys are depressed.
- 2.4.1 OUTPUT ENABLE
- Values: ON, OFF
- 2.4.2 RUN PROGRAM
- Values: NO, YES
- Description: Leads to the Ramp/Soak program control, see sub flowchart #1.
- Program Execution (Ramp Soak) Screen
- 2.4.3 SET TEMPERATURE
- Values: -40.00 C to +199.00 C, or as defined by the limits set by CONTROL RANGE
- Default value = 25.00 C
- 2.4.4 PROPORTIONAL BW
- Values: 0.05 C to 100.00 C
- Default value = 5.00 C
- Description: The proportional bandwidth is the temperature span over which the power is proportioned from -100% to +100% power, centered about the temperature set point. That is, the controller output is -100% at the end of the bandwidth range above ...
- For example, suppose the controller has a set point of 10.00 C, the bandwidth is set to 5 C, and the TE device needs to cool in order to reach this temperature. The controller will provide -100% power (cooling mode) until the sensor temperature reac...
- In practice, the temperature would usually begin to oscillate at some offset from the set point because some amount of power would always be required to achieve some amount of cooling. The offset is corrected by applying INTEGRAL GAIN.
- If the bandwidth is set too narrow, the temperature will oscillate around the set point. If the bandwidth is too wide, the controller will be slow to respond or may never reach set point despite INTEGRAL GAIN and/or DERIVATIVE GAIN settings.
- NOTE: The controller uses a bandwidth adjustment in the control algorithm, which is inversely related to the gain. A smaller bandwidth means a higher gain, and a larger bandwidth means a lower gain.
- 2.4.5 INTEGRAL GAIN
- Values: 0.00 to 10.00 (repeats per minute)
- Default value = 1.00
- A value 0.00 turns this factor off in the PID algorithm
- Description: With just proportional control, the controller’s output would be 0% when the actual temperature reaches the set temperature. However, some non-zero output power is almost always required to reach the set point, so using only proportional ...
- The integral function applies an additional amount of output power up at a rate determined by multiplying the error, the proportional bandwidth, and the integral gain.
- For example, suppose the set temperature is 10.0 C, the bandwidth is set to 5 C, and the controller oscillates at around 11.2 C, corresponding to 48% power with only the PROPORTIONAL BW set. The error is 1.2 C, based on the difference between the...
- ,40%- .×1.2 ×,1-.=,48%-.
- In this example, after one minute of operation the controller calculated that the difference between the desired set temperature and the actual temperature was +1.2 C. The INTEGRAL GAIN added an additional 48% output per minute. This additional 48%...
- If the integral control is set too high, the temperature will oscillate. If integral control is set too low, it will take a long time for the temperature to settle to steady state.
- 2.4.6 DERIVATIVE GAIN
- Values: 0.00 to 10.00 (cycles per minute)
- Default value = 0.00
- A value 0.00 turns this factor off in the PID algorithm
- Description: This senses the rate of change of the temperature and allows the controller to anticipate the power needed to compensate for rapid changes in the system loading. The derivate gain is generally used on very sluggish systems or where very q...
- For many thermoelectric systems such as the standard cooling assemblies sold by TE Technology acceptable control can be achieved by turning this function off (0.00).
- 2.4.7 ALARM 1 TEMPS
- Values: -40 to 199 or OFF for HIGH setting; -40 to 199 or OFF for LOW setting
- Default value for HIGH = 60
- Default value for LOW = -20
- Description: This sets the high and low temperatures for signaling an alarm based on the control sensor temperature. Adjustments are in 1 C increments, and the high setting must be higher than the low setting. If the HIGH setting is increased past 1...
- Note: If the controller senses an open circuit or a short circuit on the control sensor, the controller will automatically turn off output power, regardless of the ALARM 1 FUNCTION setting.
- 2.4.8 ALARM 1 FUNCTION
- Values: KEEP OUTPUT ON or TURN OFF OUTPUT
- Default value = TURN OFF OUTPUT
- Description: This setting determines what action will be taken when there is an alarm condition on the control sensor. When KEEP OUTPUT ON is selected, output power to the TE device stays on during the alarm condition, and the alarm 1 signal on JP2-8 ...
- The ALARM 1 and ALARM 2 outputs on JP2-8 AND JP2-10 will momentarily pulse on and off several times in the first second after the controller is turned on. This happens as the microprocessor in the controller configures itself, regardless of any ala...
- 2.4.9 ALARM 2 TEMPS
- Values: -40 to 199 or OFF for HIGH setting; -40 to 199 or OFF for LOW setting
- Default value for HIGH = 60
- Default value for LOW = -20
- Description: This sets the high and low temperatures for signaling an alarm based on the optional, secondary sensor temperature. Adjustments are in 1 C increments, and the high setting must be higher than the low setting. If the HIGH setting is incr...
- Note: If the controller senses an open circuit or a short circuit with respect to the thermistor, the controller will signal an alarm condition (presuming it is not set to OFF). In addition, if the controller senses an open thermistor circuit, T2 will...
- Using the GUI the user can configure ALARM 2 to operate from either the input 1 (control) sensor or the input 2 sensor. This selection is not available from the keypad. The factory default is for ALARM 2 to operate from the input 2 sensor.
- 2.4.10 ALARM 2 FUNCTION
- Values: KEEP OUTPUT ON or TURN OUTPUT OFF
- Default value = TURN OUTPUT OFF
- Description: This setting determines what action will be taken when there is an alarm condition on the secondary sensor. When KEEP OUTPUT ON is selected, output power to the TE device stays on during the alarm condition, and the alarm 2 signal on JP2-...
- 2.4.11 ALARM LATCHES
- Values: NO LATCHES, ALARMS 1&2 LATCH, ALARM2 LATCH, ALARM1 LATCH
- Default value = NO LATCHES
- Descriptions:
- NO LATCHES: If an alarm condition occurs but then clears itself, the alarm signal will automatically turn off and power to the TE device will be restored (assuming ALARM 1 FUNCTION and ALARM 2 FUNCTION are set to TURN OUTPUT OFF).
- If the alarm condition is recurring and the ALARM 1 FUNCTION and/or ALARM 2 FUNCTION is set to TURN OUTPUT OFF, the TE device can be damaged by thermal fatigue stress imposed by repeated long-term power cycling.
- NOTE: The default deadband for the latch reset is 0 C. However, the deadband can be reprogrammed using the computer interface to allow for the latch to reset at a specified temperature difference above/below the alarm set point. You can use the softw...
- ALARMS 1&2 LATCH: if an alarm condition occurs from either the control or secondary sensor or both, the controller will continue to signal an alarm until reset, even if the alarm condition is cleared. Power to the controller must be turned off and the...
- ALARM2 LATCH: if an alarm condition occurs from the secondary sensor, the controller will continue to signal the alarm until reset, even if the alarm condition is cleared. Power to the controller must be turned off and then on again to turn off the al...
- ALARM1 LATCH: if an alarm condition occurs from the control sensor, the controller will continue to signal the alarm until reset, even if the alarm condition is cleared. Power to the controller must be turned off and then on again to turn off the alar...
- Multi-Speed Fan Control: Alarm 1 can be used for regulating a speed-controlled fan. It can be used to control a separate speed-control input wire/terminal, or to control the input power directly if the peak current draw is 2 A or less. To adapt bet...
- The fan control is useful for controlling the hot-side fan of a TE cooler. One example is having the fan off when the cooler is off or in heating mode, or run at a low speed when the output is at a low level. The speed can be programmed to increase ...
- The fan speed control incorporates an initial period of operation at 100% duty cycle when the output is first turned on, before decreasing to the fan output level as determined by settings. This fan delay is user variable, and helps ensure the fan ha...
- Speed control should only be used on fans designed to have a controllable speed. Standard two-wire fans not designed for speed control may fail if operated with speed control, creating a hazardous condition. Fans supplied on TE Technology, Inc. pro...
- 2.4.12 TEMP 1 OFFSET
- Values: -10.0 C to +10.0 C
- Default value = 0.0 C
- Description: Offsets the control sensor value for both the display and control algorithm.
- 2.4.13 TEMP 2 OFFSET
- Values: -10.0 C to +10.0 C
- Default value = 0.0 C
- Description: Offsets the secondary sensor value for both the display and control algorithm.
- 2.4.14 CONTROL RANGE
- Values: -40 to +199, applies to both HIGH and LOW settings
- Default value for HIGH = 070
- Default value for LOW = -20
- Description: Sets the maximum and minimum temperatures available in the SET TEMPERATURE menu. This is a safety feature that helps to limit the set point to the safe operating temperature of the system being controlled. Adjustments are in 1 C increm...
- Note: If the CONTROL RANGE is adjusted such that it is no longer inclusive of the SET TEMPERATURE, the controller will continue to control to that SET TEMPERATURE. However, once you scroll to the SET TEMPERATURE menu, the SET TEMPERATURE will automa...
- 2.4.15 SENSOR 1, SENSOR 2 TYPE
- Values: 15K-1, 10K-2, 10K-1, 5K-1, User Defined, 230K-1, or 50K-1
- Default value = 15K-1
- Description:
- 15K-1 should be selected when using the supplied MP-3193 thermistor or other thermistors with equivalent temperature-resistance curves. See Appendix for further details.
- The other thermistors curves should be selected when using thermistors having curves as shown in the Appendix.
- A User Defined sensor can be used when the controller is to be used with an IC-type sensor or a non-programmed thermistor, for example. This requires a table of values to be programmed into the controller via computer though. Additional details are av...
- Depending on the sensor type being used, the CONTROL RANGE may need to be adjusted as well.
- 2.4.16 LOAD DEFAULTS
- Description: Reprograms all settings in the controller to the factory defaults.
- Pressing the down key and allowing the menu timer to time out on the YES selection will cause the controller to display another message instructing the user to hold the “menu key” and “up key” for 3 seconds to load the default values. See flow chart ...
- 3.0 Controller Tuning
- This tuning method follows the Ziegler-Nichols closed-loop tuning principals. Briefly, the controller will first be set to a high proportional bandwidth setting with no integral or derivative function (integral gain and derivative gain = 0). Then, th...
- Remember, the controller uses a bandwidth adjustment in the control algorithm. This is the inverse of gain. A smaller bandwidth means a higher gain, and a larger bandwidth means a lower gain. This should be kept in mind if reviewing online tutorial...
- 3.1 Set the desired control temperature in the SET TEMPERATURE menu.
- 3.2 Set the PROPORTIONAL BW to 20. This is just a starting value; the goal is to determine the proportional bandwidth at which the temperature of the TE device will first begin to oscillate. You might be able to start with a smaller bandwidth, dependi...
- 3.3 Set the INTEGRAL GAIN and DERIVATIVE GAIN to zero.
- 3.4 Decrease the PROPORTIONAL BW incrementally, allowing the TE device to reach steady state at each increment, until the temperature of the TE device begins to steadily oscillate. The system temperature will usually begin to oscillate before it actua...
- Measure the time period of the oscillation in minutes. This will be used to determine the INTEGRAL GAIN setting below.
- 3.5 Multiply the current PROPORTIONAL BW setting by 2.2 and enter this as the new bandwidth. The system should now maintain a steady state temperature near the set point.
- 3.6 The integral gain is calculated as follows: I = 0.54/T where I is the integral gain and T is the time period, in minutes, determined in section 3.4 above. Enter this value in the INTEGRAL GAIN setting.
- 3.7 The derivative gain is often times difficult to use and might cause more trouble than it is worth. If you are not experienced with process control, you might be better off leaving the DERIVATIVE GAIN set to zero.
- If you decide to use derivative gain, the other control parameters should be adjusted first.
- a) Instead of multiplying the initial proportional bandwidth setting by 2.2, multiply it by 1.7, and enter this as the new PROPORTIONAL BW setting.
- b) Calculate the integral gain as follows: I = 1.2/T, and enter this into the INTEGRAL GAIN setting.
- c) Calculate the derivative gain as follows: D =0.075 x T, and enter this into the DERIVATIVE GAIN setting.
- 3.8 The control parameters are approximate settings. Further adjustments might be needed.
- 4.0 Controller Software and USB Communication
- Controller Schematic
- Troubleshooting Controller
- TC-720 Electrical Connections
- TC-720 Mechanical Package Drawing
- TC-720 OEM Mechanical Package Drawing
- APPENDIX A-Thermistors Available for TC-720
- Appendix B - USB Communications
- Appendix C – Programming Custom Sensor Curves
- Appendix D – Programming Ramp/Soak Routines
- Appendix E – Additional Notes on Fan Control