Chapter 11, Lathe turning – Smithy Midas 1220 LTD User Manual
Page 55
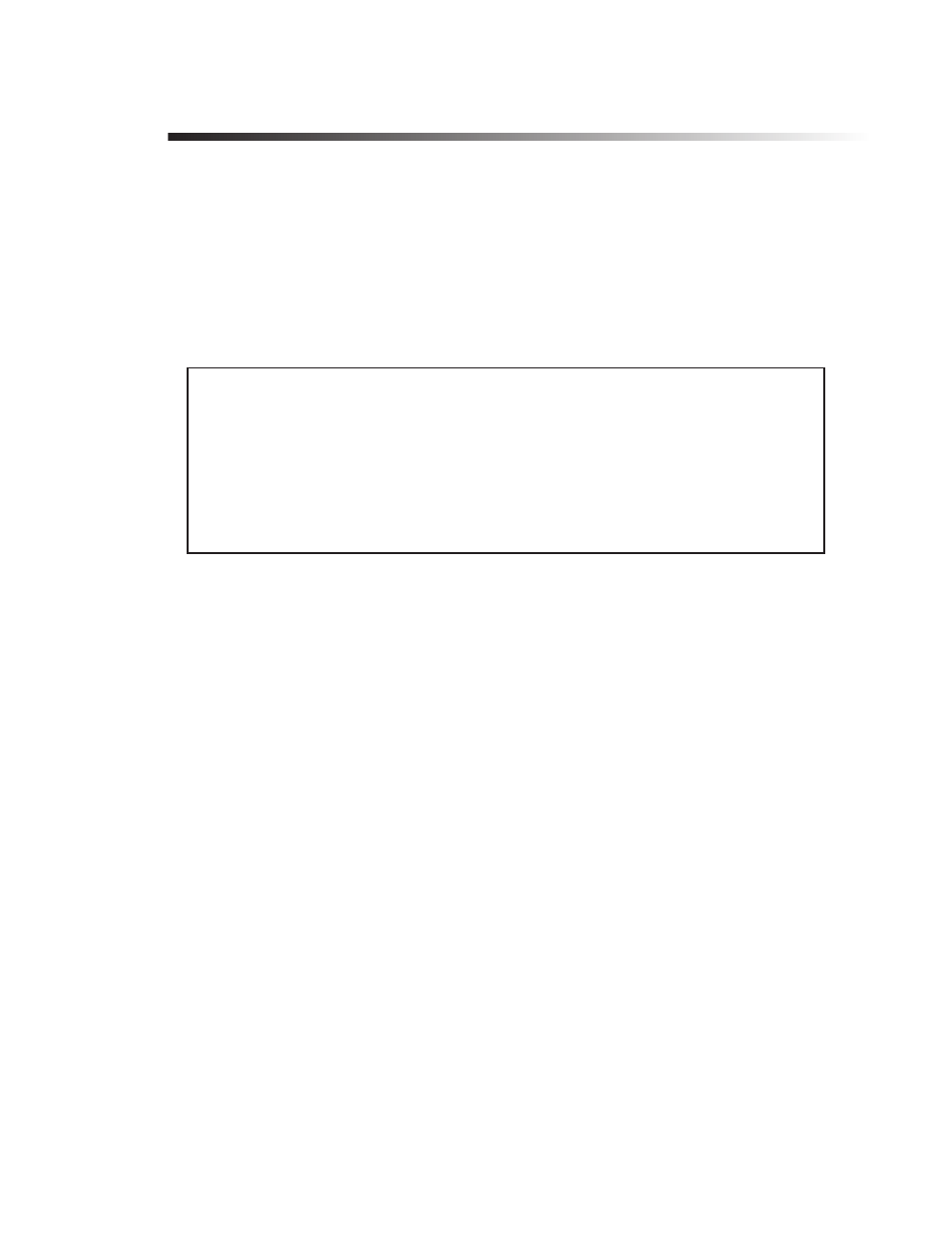
Chapter 11
Lathe Turning
Rough Turning
In turning a shaft to size and shape where you have to cut away a lot of stock, take heavy,
rough cuts to get the work done in the least time. With the MI-1220 LTD use a transverse
powerfeed for heavy cuts-from right to left toward the headstock so the thrust is against
the head-stock or the chuck. Use a right-hand turning or roundnose cutter.
Caution
Remember caution must be taken to not run the powerfeed past their limits of travel.
As part of the normal operation, procedures, run each axis through the entire
length of the proposed machining operation before engaging the powerfeed to
assure there is sufficient travel to accomplish for the desired task. Failure to so could
result in running the power feed to the end of its mechanical limit. This is what is
known as a "CRASH". A crash can cause damage to the work piece and severe
damage to the machine.
After selecting a cutter, place it into the left side of the turret . The cutter's point should
be just above or on the line of the centers. The greater the diameter of the work, the
higher the cutter can be. Adjust the height by placing shims under the cutter and raising
or lowering it (Figure 9.1).
With the tool properly positioned, tighten the Allen capscrews. Next, run the carriage to
the right end of the workpiece with the hand crank. Make sure the lathe is set to feed
toward the headstock. Now determine the depth of the cut. Move the tool to the desired
depth till it just touches the stock and zero the cross-feed dial.
Start the lathe. Run the crossfeed in by hand to take as heavy a cut as is consistent with
the power of the drive or the amount of metal to remove.
Say, for example, you need to reduce a diameter by a known number of thousandths of
an inch. If you zero the collar and watch the movement of the dial, you'll know the depth
of the feed from the zeroing point.
Note:
The dial gives a good approximation, but for exact measurements, use a
measuring instrument.
To reduce the diameter, advance the tool only half as many thousandths on the dial. This
is because the tool takes off an equal amount from both sides as it cuts a continuous strip
around the work. For example, to reduce the diameter of a shaft 0.005", you advance the
tool only 0.0025", or 1-1/4 calibrations.
Engage the tool before setting the floating dial. The tool must be moving in the direction
you want to go before you set the dial to zero to compensate for the backlash.
11-1
Or Visit www.smithy.com