MK Products CobraMig 260 PS/Feeder User Manual
Page 16
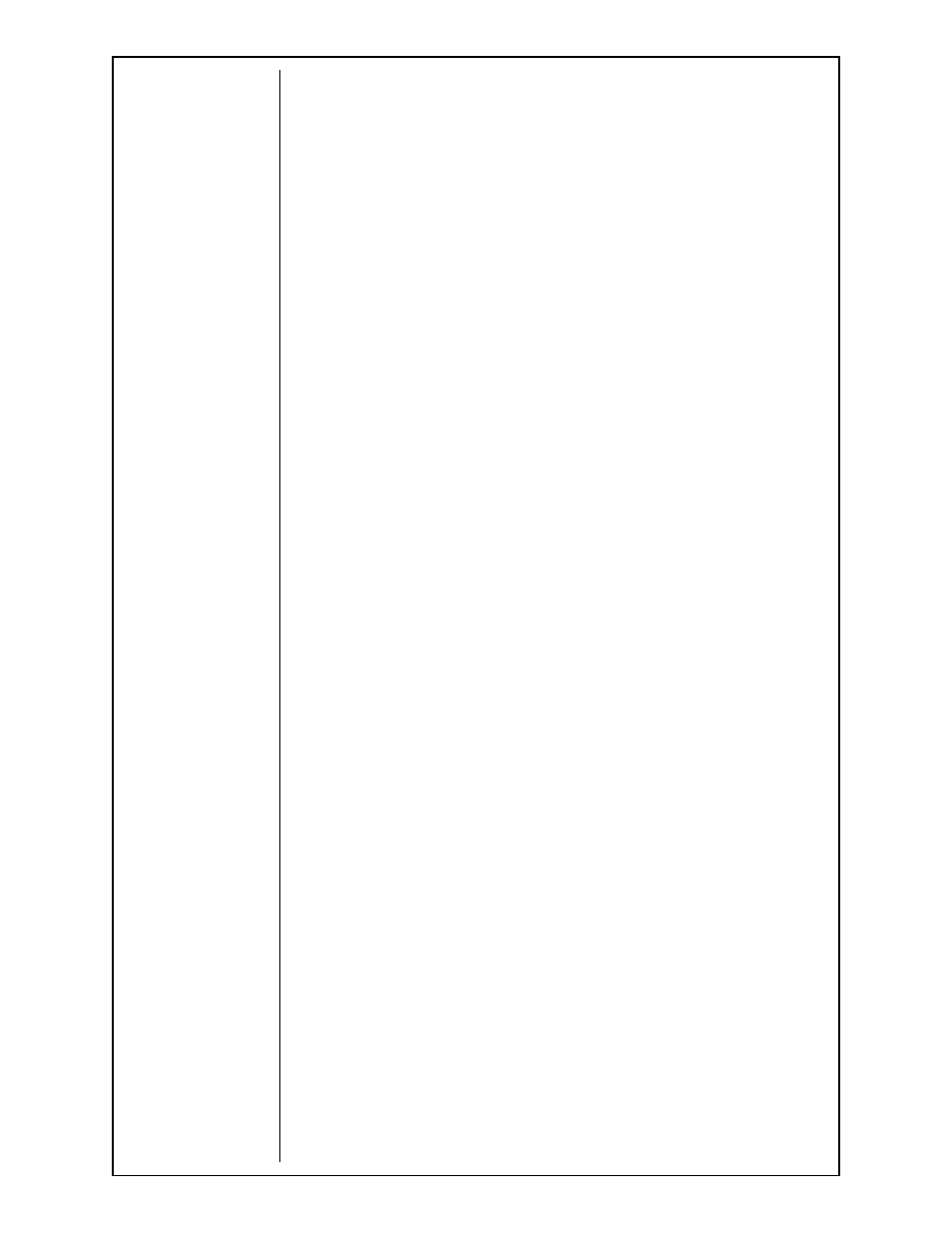
CobraMig 260 Owner's Manual - Page 10
Sample Setup - Aluminum
The procedure described below is designed to help you familiarize yourself
with this equipment and also provide you with a known procedure so that you
may perform a successful weld. Although these conditions may not be the
exact ones needed for your specifi c application, it will provide an example of
the proper use and operation of this equipment.
MATERIALS NEEDED:
1 ea
CobraMig 260 system with torch of your choice
1 ea
#6 Gas Cup (3/8")
10 ea Contact Tips .044 (621-0001 spray arc)
1 ea
Spool of clean .035 4043 Wire
1 ea
Cylinder of Argon gas w/Regulator-Flowmeter and Hose
1 ea
Stainless Steel Wire Brush
20 ea Weld coupons (2 X 6 X 1/8") 6061T-6 Aluminum
PROCEDURE:
Machine Set-up
Hook-up the CobraMig 260 according to installation instructions in owners
manual.
Install wire onto spindle and thread wire through torch according to wire
threading procedure.
Make sure "Wire Type" switch is in the "030-035 ALUM" position.
Press gun trigger and set gas fl ow to 25cfh.
Set the “VOLTAGE” control on front panel to 8.4 and the “RANGE” switch
to Lo.
Turn the “POSA START” to the off position.
Place the “POLARITY JUMPER” in the positive (+) connector and the ground
clamp in the negative connector.
Press the gun trigger for six (6) seconds. Adjust the wire feed speed until 32
inches of wire is measured in 6 seconds; this equals 320 ipm.
Using the S/S brush, brush two weld coupons until the oxide is removed.
Position Material and Tack Weld
Position the coupons on the work table to form a ‘T’ fi llet.
Place the gas cup near the work piece and tack weld one end. Remember to
provide pre-purge before each weld by cracking the torch trigger and holding
it for a few seconds before fully pressing the trigger. This will reduce built-up
pressure and aid in arc starting.
Tack weld the other end.
Deposit Weld
Securely clamp the workpiece to the table so that you have a clear view of the
arc, weld puddle, and unwelded portion of the joint at all times.
Welding is done from right to left for a right handed operator and from left
to right for a left handed operator (known as Push or Forehand). The torch