8 starting the pump, 9 operation, 10 stopping and shutdown – Flowserve WUC Worthington User Manual
Page 33
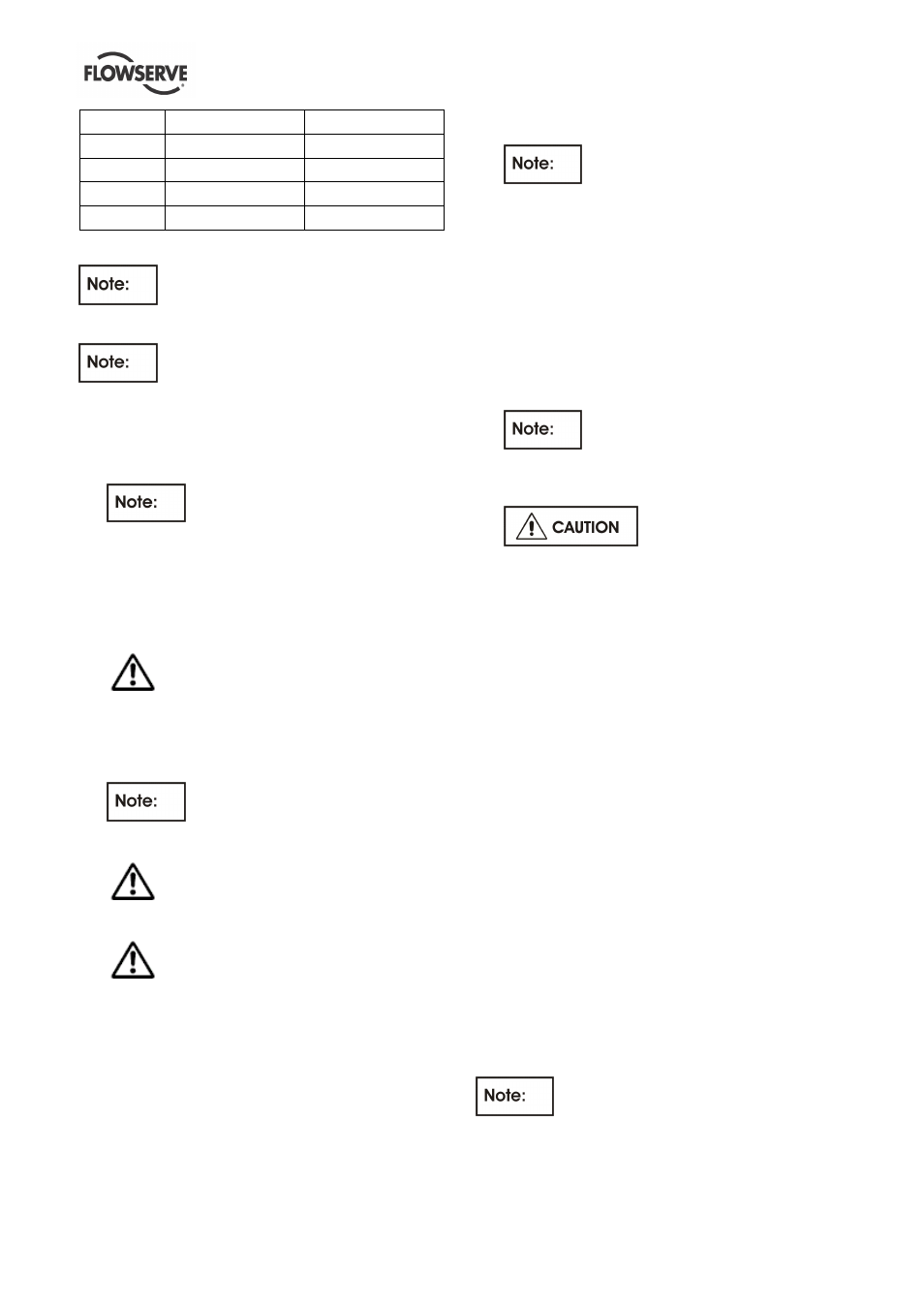
WUC USER INSTRUCTIONS ENGLISH - 07/14
Page 33 of 52
4 N
7317 BECBJ (M)
9.5 m³/h (41.8 gpm)
5 N
7318 BECBJ (M)
10 m³/h (44 gpm)
6 N
7322 BECBM
11 m³/h (48.4 gpm)
7 N
7326 BCBM
12 m³/h (52.8 gpm)
8 N
7232 / 7330 BCBM
12 m³/h (52.8 gpm)
These flow rates shall be used for the piping design.
If the pump is equipped with
hydrodynamic thrust bearing expected balance flow
rate is 12m³/h (52.8 gpm).
Design and manufacturing of the balance
line is not within the responsibility of FPD.
5.8 Starting the pump
a) Start the driver according to the specification.
(Refer to driver IOM)
Pumps are usually started against
closed discharge valve
b) Check the discharge and suction pressure gauge
to verify the pumps delivered head. Open the
discharge valve slowly, until the pump reaches the
specified operation point. The pump must operate
smoothly, and the vibration must be below 5 mm/s
(0.2 in./sec) (API 610 vibration limits).
The discharge valve must be opened
within 30 sec. after start up. Longer operation
against closed discharge valve will damage the
pump. If a minimum flow valve is installed, take
pressure gauge readings to verify the correct
operation.
If the backpressure of the discharge
pipe is sufficient, pumps can be started against
open valve.
Ensure that your driver is capable deliver
the higher torque required by starting against
open valve.
To prevent the pump from reverse rotation
after shut down, the installation of a check valve
is recommended.
Although the pump is not affected by reverse
rotation because of special coupling design , it can
be an issue with the driver.
Check the discharge and suction pressure gauge
to verify the pumps delivered head.
The pump must operate smoothly, and the
vibration must be below 5 mm/s (0.2 in./sec) (API
610 vibration limits).
If a minimum flow valve is installed, take pressure
gauge readings to verify the correct operation.
c) Check the pipe system against any leakage.
d) Check the mechanical seal against any leakage.
Right after start up a minor leakage
of the mechanical seal is quite normal. Normally
this leakage disappears after few minutes of
operation.
5.9 Operation
a) Verify that the pump is operating within the
specified limits, min/max flow, pressure,
temperature, vibration, power
b) The bearing housing temperature shall not exceed
80 °C (176 °F). If higher bearing temperature are
observed, check the viscosity grade of the used
lubrication oil.
If the pump is equipped with
hydrodynamic thrust bearing refer to bearing
manufacturer´s IOM and to recommendation for
maximum bearing temperature.
The minimum viscosity is
10 cSt at the expected oil temperature.
(Oil temperature = bearing gland temperature
+ 10 °C (50 °F))
c) From time to time check the pump shaft seal.
Leakage of 5ml/hour is also with a mechanical
shaft seal unavoidable.
d) Check the correct venting of the Can and the
headstock by opening the valve in the vent line for
short time. When the condition of service is near
the boiling point, a permanent vent line with a 3
mm ( 0.12 in.) orifice (to inhibit the exit of too much
liquid) must be installed back to the suction tank.
This will ensure that any suction and NPSH
problems can be avoided during normal service.
e) Observe the power consumption of the pump to
detect excessive wear.
5.10 Stopping and Shutdown
a) Close the outlet valve, but ensure that the pump
runs in this condition for no more than a few
seconds.
b) Stop the pump.
c) Switch off flushing and/or cooling/ heating liquid
supplies at a time appropriate to the process.
d) For prolonged shutdowns and especially when
ambient temperatures are likely to drop below
freezing point, the pump and any cooling and
flushing arrangements must be drained or
otherwise protected.
For automatic start/stop operation of the
pump, ensure that all steps described in chapter 5.6,
5.7, 5.8 and 5.9 are implemented in the control logic.