7 cool down procedure for cryogenic service – Flowserve WUC Worthington User Manual
Page 32
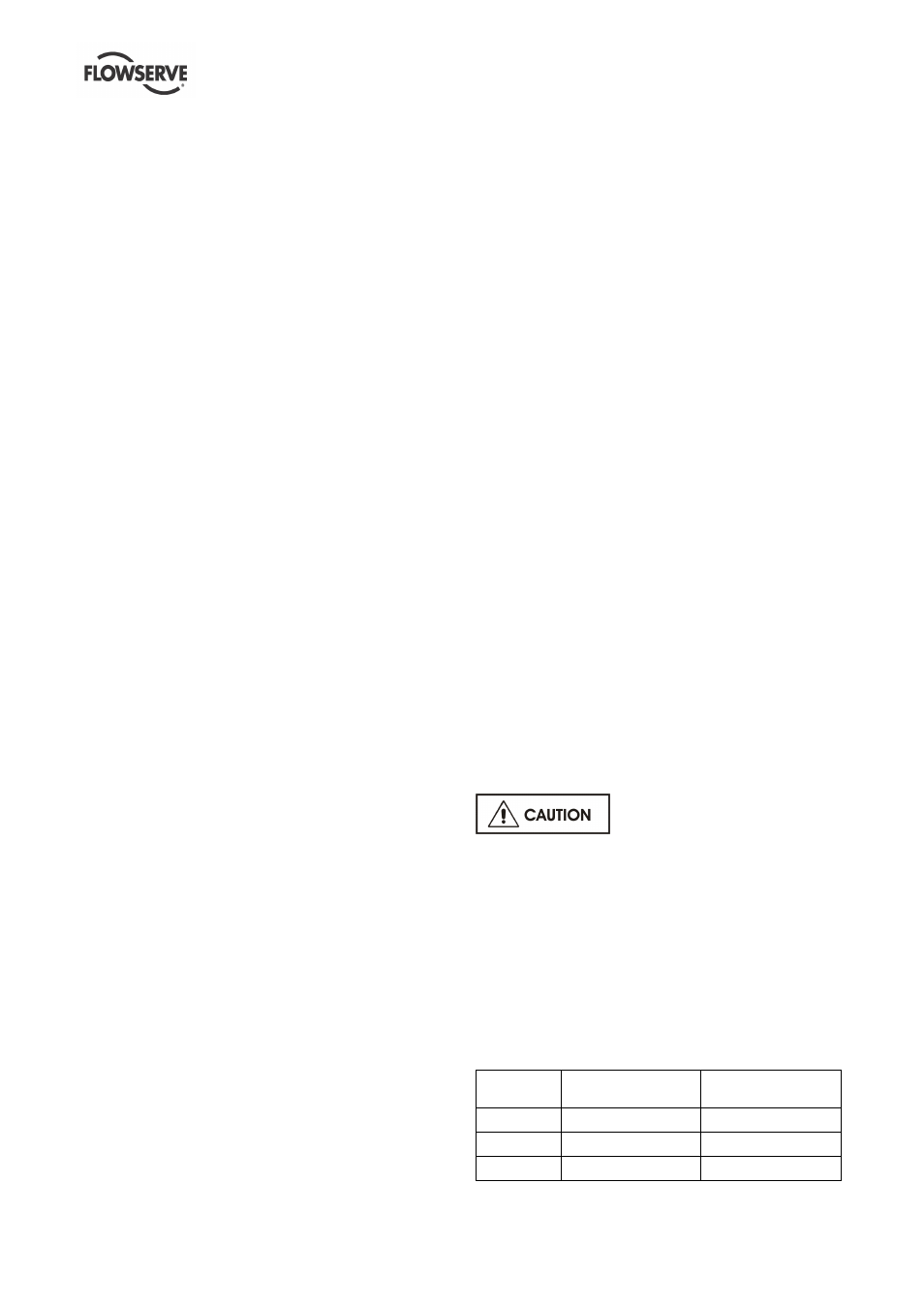
WUC USER INSTRUCTIONS ENGLISH - 07/14
Page 32 of 52
a) For non hazardous liquids close the vent valve
after 5 minutes and reopen it slowly to proof if
liquid escapes.
b) For hazardous liquids (Chemicals, non flashing
hydrocarbons) vent lines are usually piped back
to the suction tank or to the flare. Keep vent lines
open at least for 10 minutes and check suction
pressure und suction temperature against the
specification.
c) For flashing hydrocarbons vent lines are usually
piped back to the suction tank or to the flare.
Keep vent linesopen at least for 30 minutes
before starting the pump and check suction
pressure und suction temperature against the
specification. For flashing hydrocarbons, the vent
line shall remain continuously open during
operation in order to prevent build up of vapour
bubble or gas in the inlet area of the pump.
Otherwise we recommend to start the pump with
vent lines slightly open.
If a constant bypass line with a 3 mm (0.12 in.)
orifice is installed, it must be open at any time.
d) For cryogenic service (pumped fluid temperature
below 0 °C (32 °F)) refer to section 5.7 Cool
down procedure for cryogenic service.
e) Auxiliary systems, e.g. barrier /buffer fluid
systems, cooling circuits, shall be filled according
to the user instructions.
5.7 Cool down procedure for cryogenic
service
The following cool down procedure is based on field
experience with similar pumps. The procedure should
be used as a guide and adjusted as necessary to suit
each installation.
Three things must be accomplished:
1) Prior to cool down the pump must be purged
(derimed) with dry gas to remove all moisture
which might freeze and lock the pump. The pump
shaft should be checked to see that it rotates
freely by hand during all phases of cooling down
and filling.
2) The pump must be cooled slowly to prevent
unnecessary thermal shock. A cooling rate of
30 °C (54 °F) per hour is recommended.
3) Final temperature of liquid in the pump must be
low enough to prevent flushing (gasifying) when
the pump is started. When a pump is first filled,
the liquid temperature may be a few degrees
above final temperature because pump parts are
still warm contributing heat to the liquid. This is
evidenced by viewing only gas being vented out
to the atmosphere and little, if any liquid.
Additional cooling time is then required to reach a
suitable starting temperature.
Assuming all valves are closed, the cool down
procedure is as follows:
1) Open suction vent valve and discharge bypass
valve.
2) Slightly open suction valve to allow a small flow
of liquid into the pump. The liquid will vaporize,
travel through the pump, then through the suction
and discharge vent lines to the vapor phase of
the storage vessel.
3) See that the rotating element turns freely by hand
by rotating the coupling. If the coupling has been
spinning at a speed greater than approximately
500 rpm, restrain it until Step 5, then remove the
restraint.
4) Check cool down rate occasionally by opening
the drain valve and discharge bleed valve. Gas
temperature and eventual liquid presence will be
noted at these points. If desired, these valves
may be left partially open during the entire cool
down process. Adjust suction valve to control
cooling rate.
5) When liquid is observed at the suction vent valve,
gradually adjust the suction valve to fully open
position. If the coupling was restrained from
rotation in Step 3, remove the restraints.
6) When liquid appears at the discharge bleed
valve, close this valve and allow pump to cool
about 10 minutes longer. Re-open the discharge
bleed valve and close it when gas-free liquid
appears.
7) The cool down procedure is now completed and
the pump may be operated or put into cold
standby condition.
5.7.1 Cold standby condition
The pump is maintained in cold standby with only
suction valve, suction vent valve and discharge bleed
valve open.
Headstock must be fully covered
with ice up to the mechanical seal.
Check suction temperature and suction pressure to
verify cool down status.
If a gas coffer dam is installed, the balancing line shall
be led back to the suction vessel. The line must be
open during operation to avoid damage of the
equipment. The maximum back pressure created in
the balance line, shall not exceed 2 bar (29 psi)
above suction pressure. Therefore the balance line
shall be designed for a pressure loss of max. 1 bar
(14.5 psi). The following table gives the expected
balance flow rates:
Thrust
bearing No.
Bearing size
Balance flow rate
0 N
7210 BECBJ (M)
3 m³/h (13.2 gpm)
1 N
7313 BECBJ (M)
6 m³/h (26.4 gpm)
3 N
7315 BECBJ (M)
8 m³/h (35.2 gpm)