4 direction of rotation, 5 guarding, 6 priming and auxiliary supplies – Flowserve WUC Worthington User Manual
Page 31
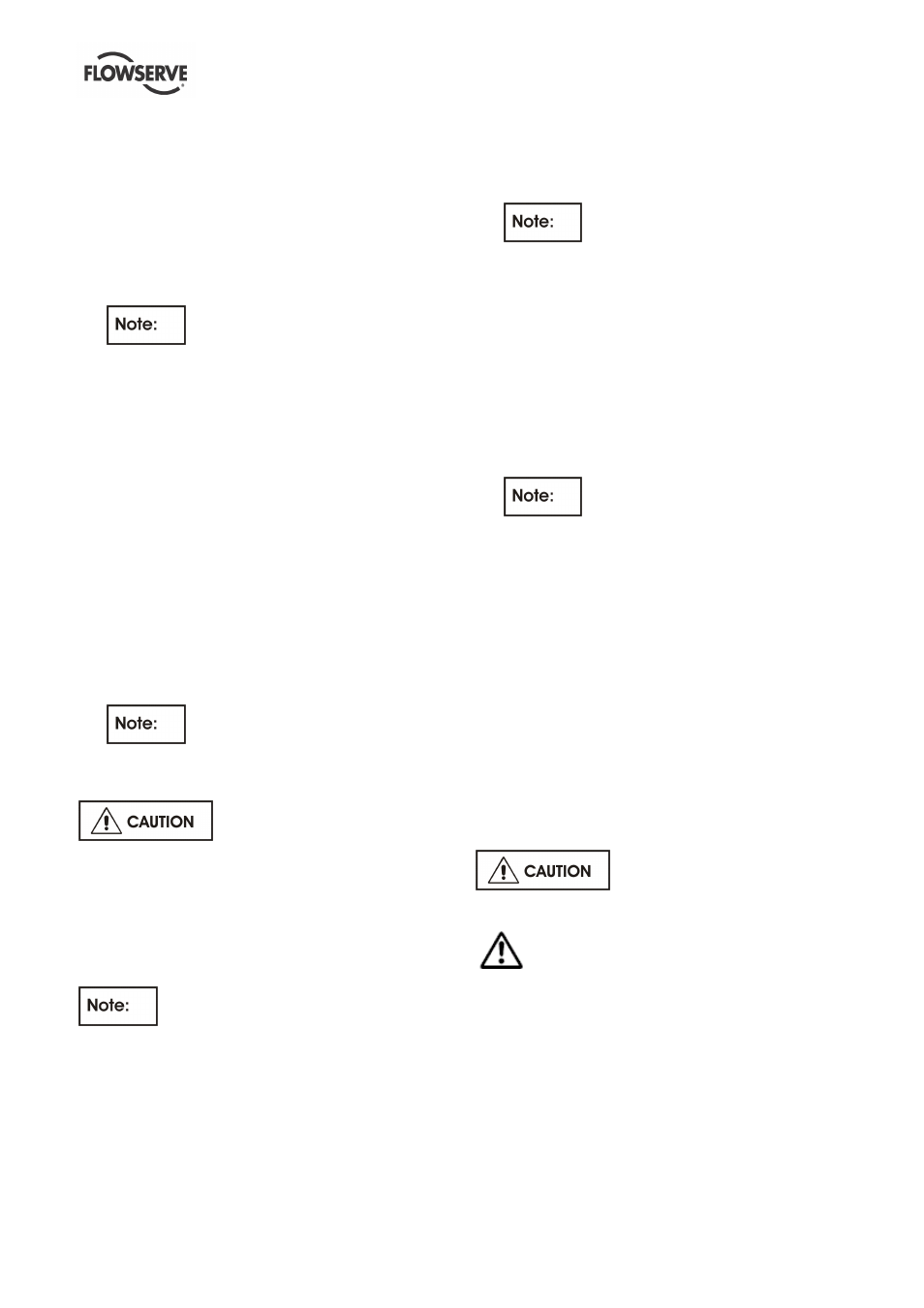
WUC USER INSTRUCTIONS ENGLISH - 07/14
Page 31 of 52
c) Open screws from the clamping unit, located on
the end of the shaft sleeve (refer to shaft seal
drawing).
d) Loose and remove socket head cap screws
[6579.1] from the shaft nut [2910].
e) Turn shaft nut upside till the rotor moves in the
lowest position and cannot turned by hand.
f) Measure the dimension from the shaft nut to the
end of the shaft.
g) Now lift the rotor by turning the shaft nut in the
other direction till it is in the highest position.
For heavy pumps
(rotor weight > 150 kg (331 lb.)) we recommend
the following practice. The rotor is already in its
lowest position. Screw in an Eyebolt into the
thread at the top of the shaft. Use a lever or a
crane to lift the shaft (do it slowly, the axial
clearance is only a few millimeters).
h) Measure again the dimension from the shaft nut
to the end of the shaft.
i)
Take the mean value of the two dimensions and
adjust the rotor to this value by turning the shaft
nut.
j)
Fix the shaft nut with the socket head cap
screws.
k) Fix the shaft sleeve with the clamping unit and
turn the assembling jigs out of the groove from
the shaft sleeve and fix them on the seal end
plate.
l)
Check if the shaft can be turned easy by hand
m) Mount fan (when delivered) coupling hub and
spacer again.
If the pump is fitted with a rigid
spacer type coupling ensure that the coupling is
completely assembled and all screws are fixed.
For pumps with a setting length
above 5 m (16.4 ft) (distance between centerline
discharge and pump suction) all the tolerances of the
line shafts must be considered.
Therefore put rotor to its lowest position. Then lift
rotor to its highest position. Now lower the rotor 3 mm
(0.12 in.) to its final axial position.
3 mm (0.12 in.) axial setting applies also for rigid
spacer type couplings.
If the pump is delivered disassembled or
if the fluid temperature is below -100°C (-148°F) o r
above 150 °C (302°F), adjusting of the rotor is
necessary prior to the first start up. Rotor adjusting is
necessary after each pump maintenance.
5.3.2 Adjusting of the rotor for pump type
10 WUC-2H, 20, 45 & 80 WUC – 2L
a) Remove coupling spacer, coupling hub on pump
shaft and fan [8161] (when delivered).
Use an anaerobic adhesive for
securing the socket set screw for reassembly.
b) Fix the position of the mechanical seal by putting
the assembly jigs, mounted on the seal end
plate, into the groove in the shaft sleeve.
c) Open screws from the clamping unit, located on
the end of the shaft sleeve (refer to shaft seal
drawing).
d) Loose and remove socket head cap screws
[6579.1] from the shaft nut [2910].
e) Turn shaft nut upside till the rotor moves in the
lowest position and cannot turned by hand.
f) Now lift the rotor by turning the shaft nut in the
other direction till it is in the highest position.
For heavy pumps
(rotor weight > 150 kg (331 lb.)) we recommend
the following practice. The rotor is already in its
lowest position. Screw in an Eyebolt into the
thread at the top of the shaft. Use a lever or a
crane to lift the shaft (do it slowly, the axial
clearance is only a few millimeters).
g) Turn the shaft nut 180° in opposite direction to slip
down the shaft 1mm (0.04 in) from its highest
position.
h) Fix the shaft nut with the socket head cap screws.
i) Fix the shaft sleeve with the clamping unit and turn
the assembling jigs out of the groove from the
shaft sleeve and fix them on the seal end plate.
j) Check if the shaft can be turned easy by hand
k) Mount fan (when delivered) coupling hub and
spacer again.
5.4 Direction of rotation
The sense of rotation of the
pump is counter clockwise (CCW); looking from the
coupling to the shaft end of the pump.
The rotation of the driver shall be checked.
5.5 Guarding
Be sure that the coupling guards are mounted
correctly at the thrust motor stool prior to start up.
5.6 Priming and auxiliary supplies
The pump must be completely primed prior to start up
by using the vent connections as shown in the
general arrangement drawing.
The venting procedure depends on the kind of fluid.
To verify if the pump is filled with liquid check: