Installation procedures – Pinnacle Systems MG User Manual
Page 21
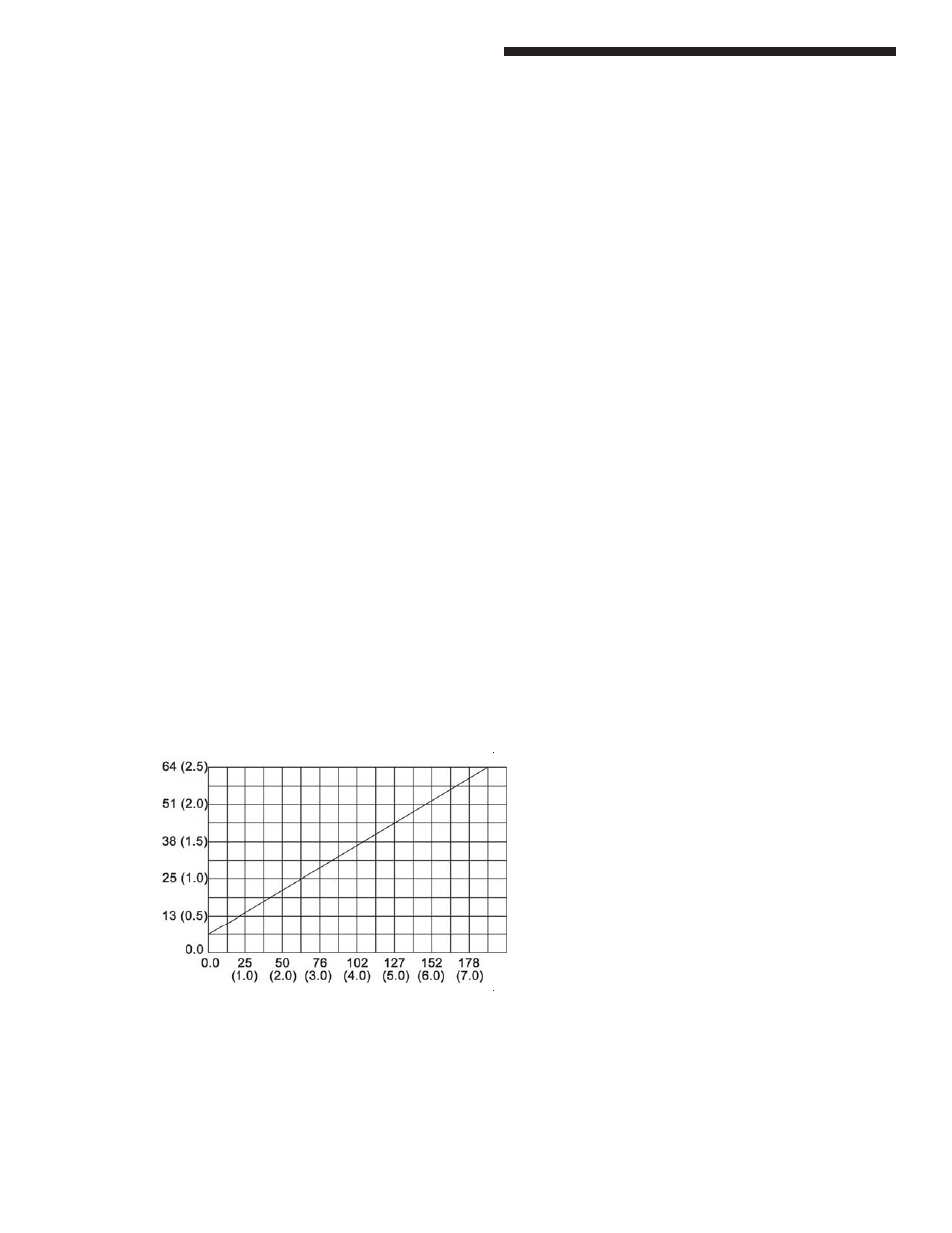
The following formula should be used when calculating
the safety distance:
Ds = K x (Ts + Tc + Tr + Tbm) + D(pf)
Ds = Minimum safety distance between the
device and the nearest point of operation
hazard (in inches).
K = Hand speed constant. This value has
been determined by various studies and,
although these studies indicate speeds of
63 in/sec to over 100 in/sec, they are not
conclusive determinations. The employer
should determine this value by considering
all factors, including physical ability of the
operator.
Ts = Stop time of the machine tool measured by
a stop time measurement device.
Tc = Response time of the control system (usually
is taken care of by the measurement
device).
Tr = Response time of the presence-sending
device and it’s interface, if any, as stated
by the manufacturer or measured by the
employer.
Tbm = Additional time allowed for the brake
monitor to compensate for variations in
normal stopping time.
D(pf) = Depth Penetration Factor. Added distance
as indicated by Figure 4 on this page. The
minimum object sensitivity is stated by the
manufacturer. If a Floating Blank is used,
use the Dpf numbers found in the Floating
Blank section of this manual.
Figure 4: Minimum Object Sensitivity and D(pf)
Minimum
Object
Penetration factor, Dpf, for presence-sensing
devices used in a vertical application with object
sensitivity less than 64 mm (2.5 inches)
Dpf, the distance added to the safety distance due
to the penetration factor compensates for varying
object sensitivities of electro-optical presence-sensing
devices.
When blanking features are used and when the
blanked area is not completely filled by the workpiece
or part, or by mechanical guarding, the minimum
object sensitivity can be calculated as:
Object sensitivity = size of the blanked area plus
minimum object sensitivity without blanking.
Once this value is found, then determine Dpf.
If the entre blanked area is filled with mechanical
guarding or other fixed material or guards, use the
device’s object sensitivity to determine Dpf.
Dpf = 3.4 (S-7) mm
(Dpf = 3.4 (S-0.275) in)
ANSI Standard B11.19-2003
Formula for calculating safety distance
of light curtains from hazardous point
of operation.
The effective sensing field of the device shall be located
at a distance from the nearest recognized hazards such
that the operator or others cannot reach the hazard with
a hand or other body part before cessation of motion
during the hazardous portion of the machine cycle.
The point at which a device responds to an intrusion may
vary. The devices should be located or adjusted such
that the device always responds to the intrusion at or
prior to the safety distance. Care should be exercised
when installing the device to ensure that it does not
detect false signals from other devices in the area.
Usually the electro-optical presence-sensing device is
used in a manner that provides a protected zone in front
of the primary work area with auxiliary devices or guards
used to protect secondary access areas. In some cases,
however, mirrors may be used in conjunction with the
device to provide 2-, 3-, or 4-sided protection.
The machine stop time should be measured with the
machine running at its fastest speed with its heaviest
die or tooling and the stop time being measured at the
90° position in the downstroke.
11
Installation Procedures
Metal Box Controller Module
13
Installation Procedures
Metal Box Controller Module
The following formula should be used when calculating
the safety distance:
Ds = K x (Ts + Tc + Tr + Tbm) + D(pf)
Ds =
Minimum safety distance between the
device and the nearest point of operation
hazard (in inches).
K =
Hand speed constant. This value has been
determined by various studies and, although
these studies indicate speeds of 63 in/sec to
over 100 in/sec, they are not conclusive
determinations. The employer should
determine this value by considering all factors,
including physical ability of the operator.
Ts =
Stop time of the machine tool measured by a
stop time measurement device.
Tc =
Response time of the control system (usually
is taken care of by the measurement device).
Tr =
Response time of the presence-sending
device and it’s interface, if any, as stated by
the manufacturer or measured by the
employer.
Tbm =
Additional time allowed for the brake monitor
to compensate for variations in normal
stopping time.
D(pf) =
Depth Penetration Factor. Added distance as
indicated by Figure 2. The minimum object
sensitivity is stated by the manufacturer. If a
Floating Blank is used, use the Dpf numbers
found on Tables 2 and 3.
Figure 4: Minimum Object Sensitivity and D(pf)
Minimum
Object
Sensitivity,
S
Penetration factor, Dpf, for presence-sensing
devices used in a vertical application with object
sensitivity less than 64 mm (2.5 inches)
Dpf, the distance added to the safety distance due to
the penetration factor compensates for varying object
sensitivities of electro-optical presence-sensing
devices.
When blanking features are used and when the
blanked area is not completely filled by the workpiece
or part, or by mechanical guarding, the minimum
object sensitivity can be calculated as:
Object sensitivity = size of the blanked area plus
minimum object sensitivity without blanking.
Once this value is found, then determine Dpf.
If the entre blanked area is filled with mechanical
guarding or other fixed material or guards, use the
device’s object sensitivity to determine Dpf.
Dpf = 3.4 (S-7) mm
(Dpf = 3.4 (S-0.275) in)
ANSI Standar
ANSI Standar
ANSI Standar
ANSI Standar
ANSI Standard B11.19-2003
d B11.19-2003
d B11.19-2003
d B11.19-2003
d B11.19-2003
F
F
F
F
For
or
or
or
orm
m
m
m
mula f
ula f
ula f
ula f
ula for calcula
or calcula
or calcula
or calcula
or calculating saf
ting saf
ting saf
ting saf
ting safety distance
ety distance
ety distance
ety distance
ety distance
of
of
of
of
of light cur
light cur
light cur
light cur
light curtains fr
tains fr
tains fr
tains fr
tains from hazar
om hazar
om hazar
om hazar
om hazardous point
dous point
dous point
dous point
dous point
of
of
of
of
of oper
oper
oper
oper
opera
a
a
a
ation.
tion.
tion.
tion.
tion.
The effective sensing field of the device shall be located
at a distance from the nearest recognized hazards such
that the operator or others cannot reach the hazard with a
hand or other body part before cessation of motion during
the hazardous portion of the machine cycle.
The point at which a device responds to an intrusion may
vary. The devices should be located or adjusted such that
the device always responds to the intrusion at or prior to
the safety distance. Care should be exercised when
installing the device to ensure that it does not detect false
signals from other devices in the area.
Usually the electro-optical presence-sensing device is used
in a manner that provides a protected zone in front of the
primary work area with auxiliary devices or guards used
to protect secondary access areas. In some cases,
however, mirrors may be used in conjunction with the
device to provide 2-, 3-, or 4-sided protection.
The machine stop time should be measured with the
machine running at its fastest speed with its heaviest die
or tooling and the stop time being measured at the 90°
position in the downstroke.
11